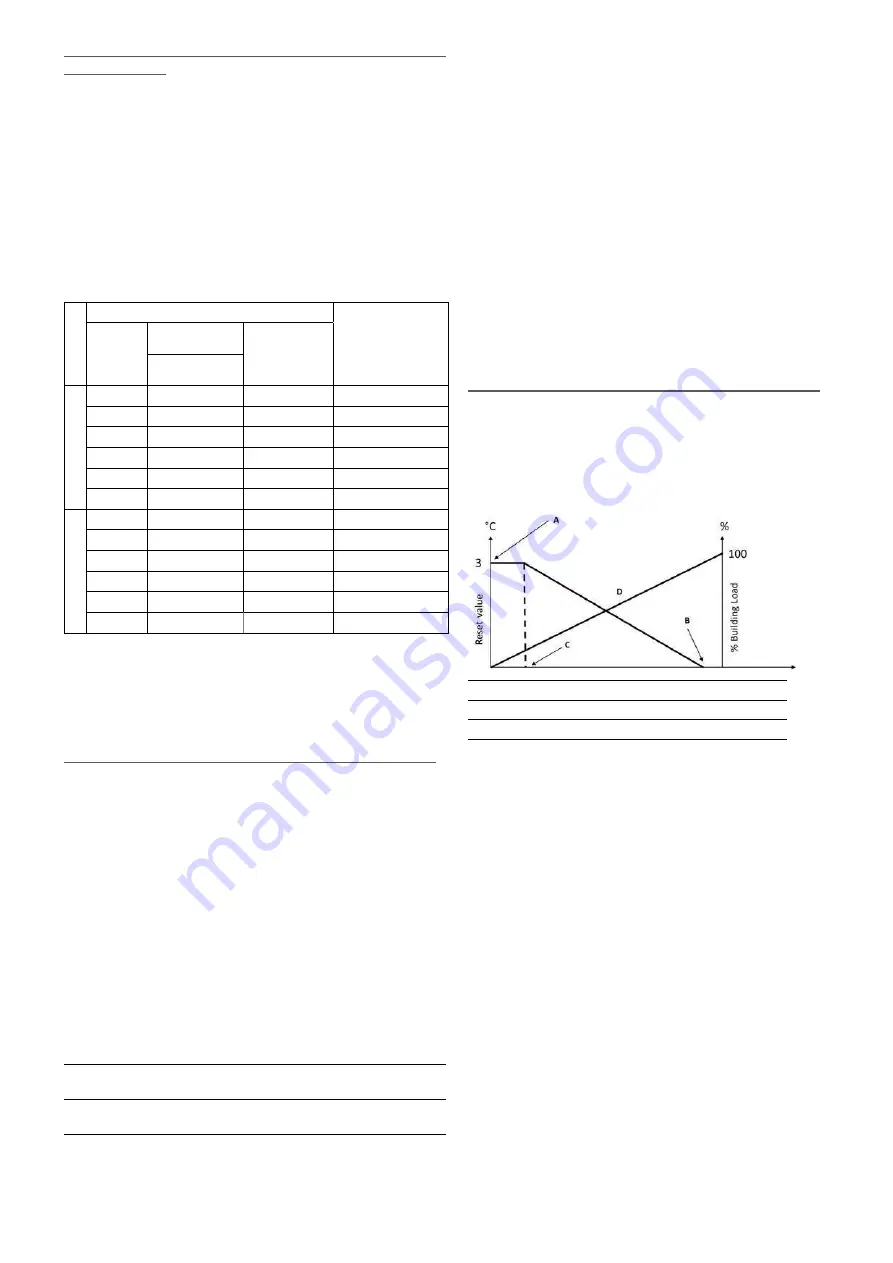
27
Depending on the current operating type, the active setpoint
can be selected:
• By choosing the active setpoint in the General
Parameters menu (Setpoint Select, GENUNIT).
• Via the volt-free contacts (see section 3.7.3).
• Via network commands [SP_SEL].
• Via the schedule setting (schedule 2).
The following table summarises the possible setpoint selections
based on the control type (local, remote, network) and the
following parameters:
• Heating/Cooling operating mode.
• Setpoint select.
• Setpoint selection contact status.
• Schedule 2 status for setpoint selection [SP_OCC].
Parameters status
Active
setpoint
Mode
SP_SEL
(Local/Net)
Setpoint select
(Local/Net)
Setpoint
occupancy
[SP_OCC]
Setpoint switch
(Remote)
cooling
1
sp 1
-
cooling setpoint 1
2
sp 2
-
cooling setpoint 2
3
sp 3
-
ice storage setpoint
0
auto
occupied
cooling setpoint 1
0
auto
unoccupied
cooling setpoint 2
0
auto
holiday
cooling setpoint 2
heating
1
sp 1
-
heating setpoint 1
2
sp 2
-
heating setpoint 2
3
sp 3
-
heating setpoint 3
0
auto
occupied
heating setpoint 1
0
auto
unoccupied
heating setpoint 2
0
auto
holiday
heating setpoint 3
8.5.2 - Reset
Reset.means.that.the.active.control.point.is.modified.so.that.
the machine capacity required is adjusted to be as close as
possible to the demand.
The reset source can be provided by one of the following:
• Outdoor air temperature (that gives a measure of the
load trends for the building).
• Return water temperature (heat exchanger delta T
gives an average building load).
• 4-20 mA reset signal (4-20 mA signal / external
temperature reading indicates the load trend).
The.source.of.the.reset.can.be.configured.in.the.Heat/Cool.
Config.menu.(HCCONFIG)..In.response.to.a.change.in.the.
outside temperature, delta T, or 4-20 mA reset signal reading,
the control point is reset to optimise unit performance.
To set Cooling / Heating Reset Select
1..Navigate.to.the.Configuration.menu.
2. Select
Heat/Cool Config
(HCCONFIG).
3. Set
Cooling Reset Select
[cr_sel] OR
4. Set Heating Reset Select [hr_sel].
Cooling Reset Select [cr_sel]
Heating Reset Select [hr_sel]
0 = none
1 = OAT
2 = delta T
3 = 4-20mA
The units use two control point reset types, cooling control
point reset or heating control point reset. Dry cooler condenser
option has condensing setpoint reset which can be applied if
the condensing setpoint control depends on outdoor air
temperature reading (reset source = OAT).
Cooling mode (30WG / 30WGA / 61WG)
Cooling control point reset is used to control the evaporator
water temperature reset. Heating control point reset is not
used for temperature control in the condenser water loop.
Heating reset may be used to reset the condensing setpoint
for optimised condenser operation. This is only possible on
the outside temperature. Delta T is not used.
Heating mode (30WG / 61WG)
Heating control point reset is used to control the condenser
water temperature reset.
In both cases (cooling and heating mode) the reset parameters,
i.e..slope,.reset,.and.maximum.value,.are.configurable.in.the.
Reset.Configuration.menu.(RESETCFG).
Reset is a linear function based on three parameters:
• A reference at which reset is zero (outdoor temperature
or delta T or 4-20 mA signal – no reset value).
• A reference at which reset is maximum
(OAT or delta T or 4-20 mA signal – full reset value).
• The maximum reset value.
Reset example in Cooling mode
10
Outdoor air temperature (OAT)
20
3
Heat exchanger delta T
5
4
Analogue input
20
no reset
selection
full reset
Legend:
A: Maximum reset value
B: OAT / delta T / 4-20 mA for no reset
C: OAT / delta T / 4-20 mA for full reset
D: Building load
8.6 - Capacity control
The Touch Pilot Junior control adjusts the number of active
compressors to keep the heat exchanger temperature at its
setpoint. The precision with which this is achieved depends
on.the.capacity.of.the.water.loop,.the.flow.rate,.the.load,.and.
the number of stages available on the unit.
To determine the optimum moment at which to add or
withdraw a capacity stage, the control system continuously
takes account of the temperature error with respect to the
control point, as well as the rate of change in this error and the
difference between entering and leaving water temperatures.
If the unit undergoes too many starts within an hour or the
compressor runs below one minute each time it is started, this
automatically brings about reduction of compressor starts, which
makes the controlled leaving water temperature less precise.
The high pressure, low pressure or water loop conditions can
also affect temperature control accuracy. Compressors are
started and stopped in a sequence designed to equalise the
number of start-ups (value weighted by their operating time).