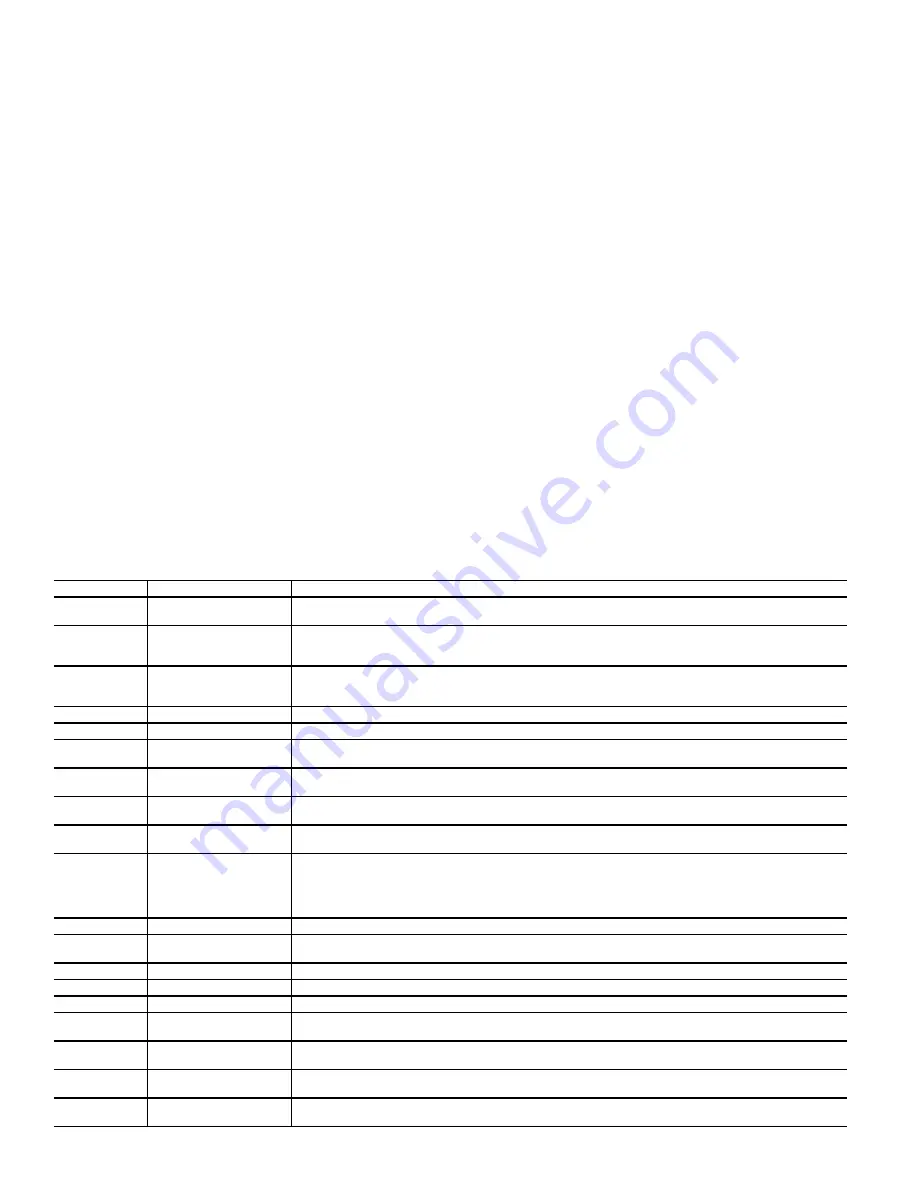
126
APPENDIX C — VARIABLE FREQUENCY DRIVE (VFD) (cont)
The fault code on the control panel display is temporary. Press-
ing the MENU, ENTER, UP button or DOWN buttons re-
moves the fault message. The message reappears after a few
seconds if the control panel is not touched and the fault is still
active.
ALARMS (GREEN LED FLASHING)
For less severe errors, called alarms, the diagnostic display is
advisory. For these situations, the drive is simply reporting that
it had detected something unusual. In these situations, the
drive:
1. Flashes the green LED on the drive (does not apply to
alarms that arise from control panel operation errors)
2. Sets an appropriate bit in an Alarm Word parameter (0308
or 0309)
3. Overrides the control panel display with the display of an
alarm code and/or name
Alarm messages disappear from the control panel display after
a few seconds. The message returns periodically as long as the
alarm condition exists.
CORRECTING FAULTS
The recommended corrective action for faults is shown in the
Fault Listing Table V. The VFD can also be reset to remove the
fault. If an external source for a start command is selected and
is active, the VFD may start immediately after fault reset.
To reset a fault indicated by a flashing red LED, turn off the
power for 5 minutes. To reset a fault indicated by a red LED
(not flashing), press RESET from the control panel or turn off
the power for 5 minutes. Depending on the value of parameter
1604 (FAULT RESET SELECT), digital input or serial com-
munication could also be used to reset the drive. When the
fault has been corrected, the motor can be started.
HISTORY
For reference, the last three fault codes are stored into parame-
ters 0401, 0412, 0413. For the most recent fault (identified by
parameter 0401), the drive stores additional data (in parameters
0402 through 0411) to aid in troubleshooting a problem. For
example, a parameter 0404 stores the motor speed at the time
of the fault. To clear the fault history (all of Group 04, Fault
History parameters), follow these steps:
1. In the control panel, Parameters mode, select parameter
0401.
2. Press EDIT.
3. Press the UP and DOWN buttons simultaneously.
4. Press SAVE.
CORRECTING ALARMS
To correct alarms, first determine if the Alarm requires any
corrective action (action is not always required). Use Table W
to find and address the root cause of the problem.
If diagnostics troubleshooting has determined that the drive is
defective during the warranty period, contact ABB Automation
Inc., at 1-800-435-7365, option 4, option 3. A qualified techni-
cian will review the problem with the caller and make a deter-
mination regarding how to proceed. This may involve dis-
patching a designated service station (DSS) representative
from an authorized station, dispatching a replacement unit, or
advising return for repair.
Table V — Fault Codes
FAULT CODE FAULT NAME IN PANEL
DESCRIPTION AND RECOMMENDED CORRECTIVE ACTION
1
OVERCURRENT
Output current is excessive. Check for excessive motor load, insufficient acceleration time (parameters
2202 ACCELER TIME 1, default 30 seconds), or faulty motor, motor cables or connections.
2
DC OVERVOLT
Intermediate circuit DC voltage is excessive. Check for static or transient over voltages in the input
power supply, insufficient deceleration time (parameters 2203 DECELER TIME 1, default 30 seconds),
or undersized brake chopper (if present).
3
DEV OVERTEMP
Drive heat sink is overheated. Temperature is at or above 115°C (239°F). Check for fan failure,
obstructions in the air flow, dirt or dust coating on the heat sink, excessive ambient temperature, or
excessive motor load.
4
SHORT CIRC
Fault current. Check for short-circuit in the motor cable(s) or motor or supply disturbances.
5
OVERLOAD
Inverter overload condition. The drive output current exceeds the ratings.
6
DC OVERVOLT
Intermediate circuit DC voltage is not sufficient. Check for missing phase in the input power supply,
blown fuse, or under voltage on main circuit.
7
Al1 LOSS
Analog input 1 loss. Analog input value is less than AI1 FLT LIMIT (3021). Check source and connection
for analog input and parameter settings for AI1 FLT LIMIT (3021) and 3001 AI<MIN FUNCTION.
8
Al2 LOSS
Analog input 2 loss. Analog input value is less than AI2 FLT LIMIT (3022). Check source and connection
for analog input and parameter settings for AI2 FLT LIMIT (3022) and 3001 AI<MIN FUNCTION.
9
MOT OVERTEMP
Motor is too hot, as estimated by the drive. Check for overloaded motor. Adjust the parameters used for
the estimate (3005 through 3009). Check the temperature sensors and Group 35 parameters.
10
PANEL LOSS
Panel communication is lost and either drive is in local control mode (the control panel displays LOC), or
drive is in remote control mode (REM) and is parameterized to accept start/stop, direction or reference
from the control panel. To correct check the communication lines and connections. Check parameter
3002 PANEL COMM ERROR, parameters in Group 10: Command Inputs and Group 11:Reference
Select (if drive operation is REM).
11
ID RUN FAIL
The motor ID run was not completed successfully. Check motor connections.
12
MOTOR STALL
Motor or process stall. Motor is operating in the stall region. Check for excessive load or insufficient
motor power. Check parameters 3010 through 3012.
13
RESERVED Not
used.
14
EXT FAULT 1
Digital input defined to report first external fault is active. See parameter 3003 EXTERNAL FAULT 1.
15
EXT FAULT 2
Digital input defined to report second external fault is active. See parameter 3004 EXTERNAL FAULT 2.
16
EARTH FAULT
The load on the input power system is out of balance. Check for faults in the motor or motor cable. Verify
that motor cable does not exceed maximum specified length.
17
UNDERLOAD
Motor load is lower than expected. Check for disconnected load. Check parameters 3013 UNDERLOAD
FUNCTION through 3015 UNDERLOAD CURVE.
18
THERM FAIL
Internal fault. The thermistor measuring the internal temperature of the drive is open or shorted. Contact
Carrier.
19
OPEX LINK
Internal fault. A communication-related problem has been detected between the OMIO and OINT
boards. Contact Carrier.
Summary of Contents for /50HC 04-28
Page 69: ...69 Fig 24 Typical Control Diagram for 48HC 04 14 Units 48HC 08 09 shown ...
Page 70: ...70 Fig 25 Typical Power Diagram for 48HC 04 14 Units 48HC 08 09 shown ...
Page 71: ...71 Fig 26 Typical Control Diagram for 50HC 04 14 Units 50HC 14 shown ...
Page 72: ...72 Fig 27 Typical Power Diagram for 50HC 04 14 Units 50HC 14 Non Humidi MiZer shown ...
Page 73: ...73 Fig 28 Typical Control Diagram 48HC 17 28 Units ...
Page 74: ...74 Fig 29 Typical Control Diagram 50HC 17 28 Units ...
Page 75: ...75 Fig 30 Typical Humid MiZer Power Diagram and Component Arrangement 48 50HC 17 28 Units ...
Page 76: ...76 Fig 31 Typical Non Humid MiZer Power Diagram and Component Arrangement 48 50HC 17 28 Units ...
Page 89: ...89 Fig 42 Modulating ERV Wiring Schematic ...
Page 90: ...90 Fig 43 EnergyX ERV Control Box Component Layouts ...
Page 101: ...101 Fig 59 Exhaust Fan Assembly Removal Exhaust Fan Assembly ...
Page 141: ......