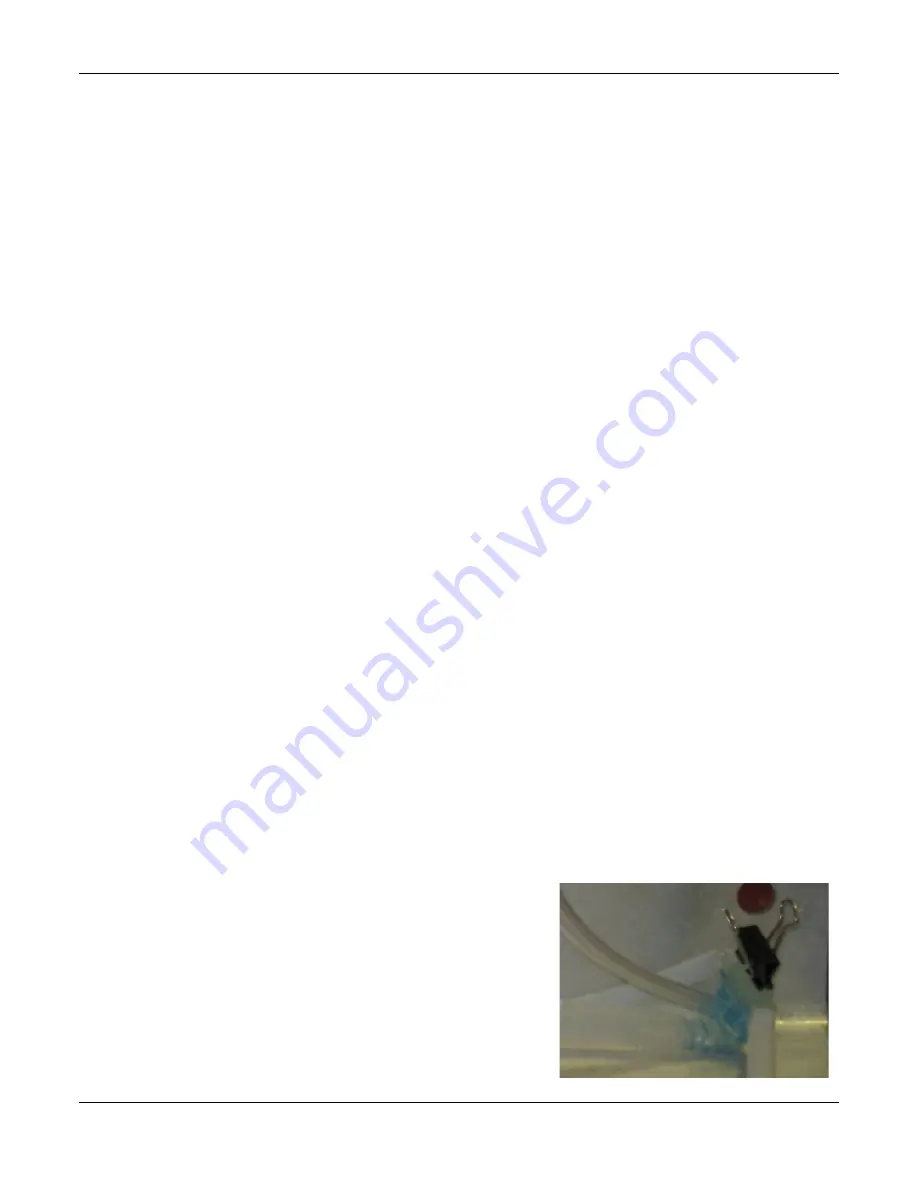
Air
Life
®
nCPAP Driver Service Manual
2008, Cardinal Health
Page 66 of 81
42. Re-connect the Air source and allow at least 60 seconds for the valves to adjust and re-stabilize.
Verify that the system returns to the original FiO
2
setting
43. Press the Alarm/Mute button to clear the latched alarm. Do not proceed until the alarms clear and
the system has re-stabilized.
44. Disconnect the Oxygen source.
45. Verify an audible alarm occurs (High priority, red flashing).
46. Verify that ‘Oxygen Pressure Low’ appears in the message bar (alternating between low oxygen
pressure and low FiO
2
).
47. Verify that CPAP pressure is maintained utilizing the air source. Note that the FiO
2
will be 21% and
the Low FiO
2
alarm will be active.
48. Re-connect the Oxygen source and allow at least 60 seconds for the system to re-stabilize.
49. Verify that the system returns to the original FiO
2
setting.
50. Press the Alarm/Mute button to clear alarm.
51. If all alarm conditions were met and the auto-recovery returned the system to original condition,
then circle PASS. Otherwise circle FAIL.
Low Pressure/ Disconnect Alarm Test:
52. Occlude both prongs and set CPAP to 5 cm H
2
O. Allow valves to stabilize for at least 60 seconds.
FiO
2
may be set to 21% for this test.
53. Remove the occlusion of the prongs (or remove the prongs from the generator).
54. Verify that a medium priority audible alarm is actived (yellow flashing LED) and ‘Disconnect’ or “Low
Pressure” alarm text appears in the message bar within 15 seconds (normal alarm delay).
55. Verify that the flow rate displayed by the Driver is at “Target” flow +/- 3 lpm.
56. If the Low Pressure/ Disconnect alarm activated within 15 seconds, then circle PASS. If this test
fails, verify that both prongs are open. If no alarm occurs, then circle FAIL.
High Pressure Alarm Test:
57. Completely remove the white exhaust tubing from the
generator’s exhaust Port.
58. Occlude the prongs and set CPAP to 5 cm H
2
O. Allow
valves to stabilize for approximately 60 seconds.
59. Completely occlude the exhaust port momentarily and then
release the occlusion.