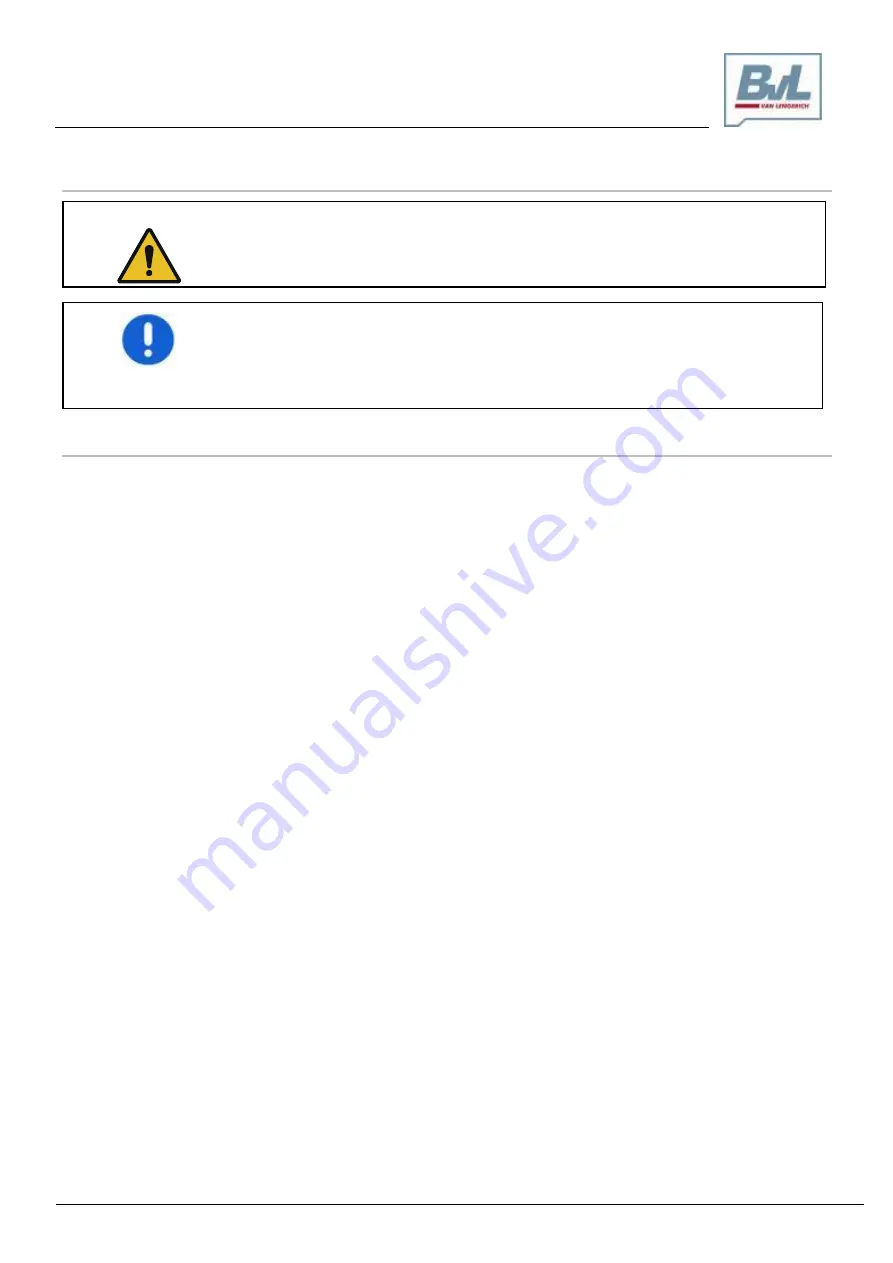
Transport, setup, and initial commissioning
V-MIX Fix Plus
Translation of the Original Operating Manual
61
5.4
Connecting the electrical system
DANGER
Hazards due to electrical voltage can arise if the machine is not connected correctly,
whereby inadvertent contact with live parts is possible.
Only allow authorized qualified personnel to carry out electrical installation of ma-
chine parts as specified in the circuit diagram.
Pay attention to the motor's direction of rotation when putting the machine into opera-
tion. The mixing auger must turn clockwise.
A sticker showing the correct connections can be found on the cover of the gear mo-
tor. They are also indicated in the operating manual of the motor manufacturer. For
an overview of the supplied third-party documents, refer to chapter 9 "Appendix".
5.5
Checking the machine for proper operation
Inspect all functions of the machine before the initial commissioning and before each use:
1. Grease the entire machine. For this purpose, observe the information given in chapter "Cleaning,
maintenance, and repairs", starting on page 71.
2. Check the oil level of the gear unit in the oil expansion tank. For this purpose, refer to chapter
"Cleaning, maintenance and repairs", starting on page "70".
3. Check the oil level in the hydraulic oil tank. For this purpose, refer to chapter "Cleaning,
maintenance and repairs", starting on page "70".
4. Check all functions of the machine before filling container for the first time.