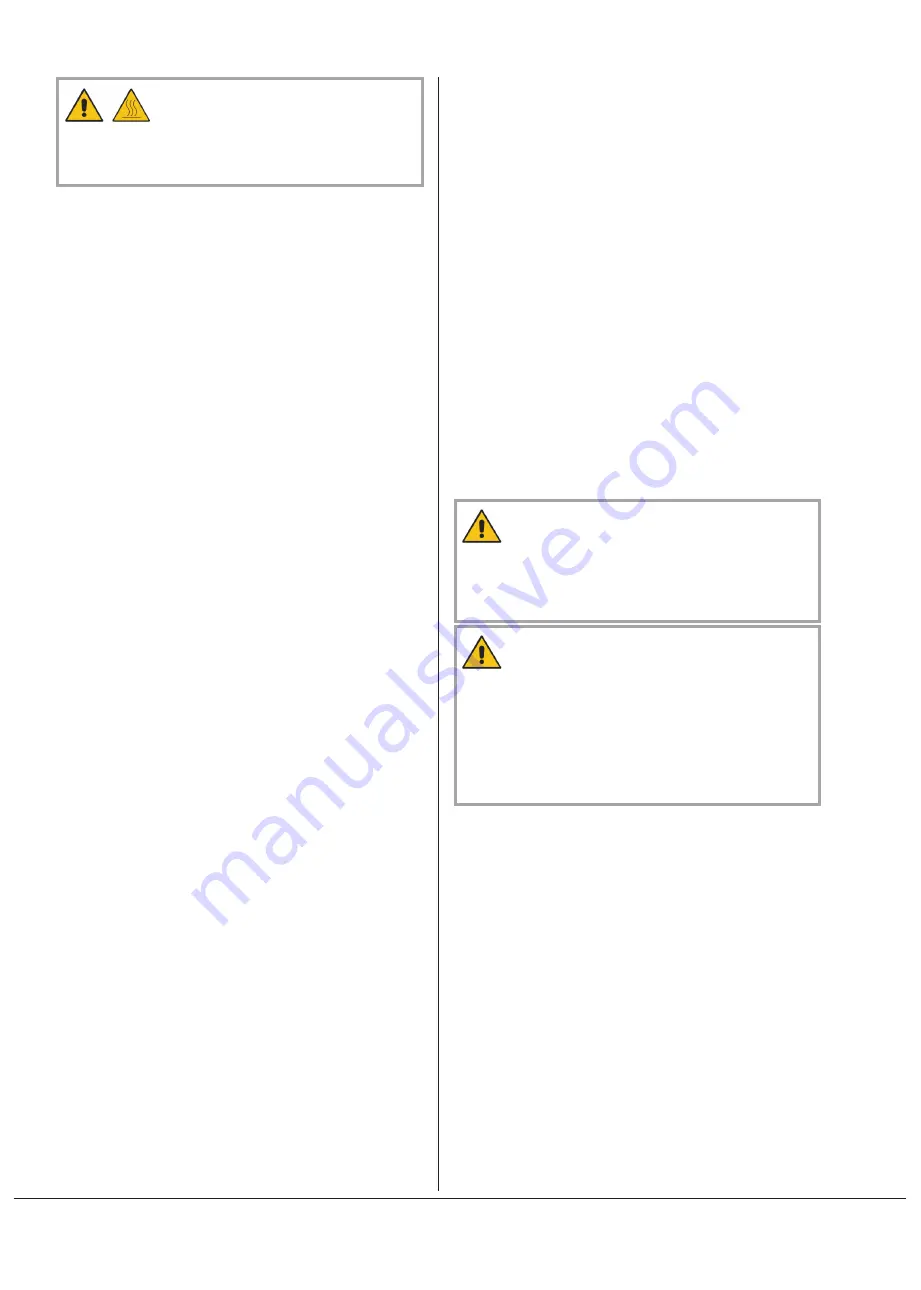
CAUTION
Du ring ope ra tion the sur face of the va cuum pump may reach tem -
pe ra tu res of more than 70°C.
Risk of burns!
●
Prior to ac tion that re qui res tou ching of the va cuum pump, let the
va cuum pump cool down.
In case of oil drai ning:
◆
Let the va cuum pump cool down for no more than 20 mi nu tes
●
Prior to dis con nec ting connec tions make sure that the connec ted
pi pes/li nes are ven ted to at mos phe ric pressure
Maintenance Schedule
NOTE
: The main te nance in ter vals de pend very much on the in di vi dual
ope ra ting condi tions. The in ter vals gi ven be low shall be consi de red as
star ting va lues which should be shor te ned or ex ten ded as ap pro priate.
Par ti cu lar ly hea vy duty ope ra tion, such like high dust loads in the en vi -
ron ment or in the pro cess gas, other conta mi na tions or in gress of pro -
cess ma te rial, can make it ne ces sa ry to shor ten the maintenance
intervals significantly.
Monthly:
●
Make sure that the va cuum pump is shut down and loc ked against
inad ver tent start up
●
Check the le vel and the co lour of the oil (see “Chec king the Oil”)
●
Check the va cuum pump for oil leaks - in case of leaks have the
va cuum pump re pai red (Busch ser vice)
●
Check the func tion of the ex haust fil ters (l,120) (see “Exhaust Fil -
ters”)
In case an in let air fil ter is ins tal led:
◆
Check the in let air fil ter, if ne ces sa ry clean (with com pres sed
air) or re place
In case of ope ra tion in a dus ty en vi ron ment:
◆
Make sure that the hou sing is free from dust and dirt, clean if
ne ces sa ry (see “Eve ry 6 Months:”)
Every 6 Months:
●
Make sure that the va cuum pump is shut down and loc ked against
inad ver tent start up
●
Make sure that the hou sing is free from dust and dirt, clean if ne -
ces sa ry
●
Clean the fan co wlings, fan wheels, ven ti la tion pro tec tion screen
and co o ling fins
Yearly:
●
Make sure that the va cuum pump is shut down and loc ked against
inad ver tent start up
●
Re place the ex haust fil ters (l,120) (see “Exhaust fil ters”)
In case an in let fil ter is ins tal led:
◆
Clean (with com pres sed air) or re place the in let air fil ter
●
Check the in let screen (h, 261), clean if ne ces sa ry
Every 500 - 2000 Operating hours (see “Oil Life”)
●
Change the oil, re place the oil fil ter(s) (d,100) and clean the le vel
switch (m,194) (see “Oil and Oil Fil ter Change”)
Every 16000 Operating hours, at the latest after 4
Years:
●
Have a ma jor over haul on the va cuum pump (Busch ser vice)
Checking the oil
Checking the level
●
Make sure that the va cuum pump is shut down and loc ked against
inad ver tent start up
●
Make sure that the oil has col lec ted at the bot tom of the oil se pa -
ra tor (f,75)
●
Read the le vel on the sight glass (i,83)
In case the le vel has drop ped un der neath the MIN-mar king:
◆
Top up oil (see “Top ping up Oil”)
In case the le vel ex ceeds the MAX-mar king:
◆
Check the di lu tion with conden sa tes.
◆
Change the oil (see “Change the oil”)
If ap pro priate re tro fit a gas bal last (Busch Ser vice) and ob serve the
chap ter “Ope ra ting No tes, Con veying Con den sable Vapours”
Topping up Oil
NOTE
: Under nor mal condi tions there should be no need to top up oil
du ring the re com men ded oil change in ter vals. A si gni fi cant le vel drop
in di ca tes a mal func tion (see “Trou bles ho o ting”).
NOTE
: Du ring ope ra tion the ex haust fil ter gets sa tu ra ted with oil. It is
the re fore nor mal that the oil le vel will drop sligh tly af ter re pla ce ment of
the exhaust filter.
CAUTION
Fil ling oil through the suc tion connec tion/gas in let (a,260) will re sult
in brea kage of the va nes (n,22) and des truc tion of the va cuum
pump.
Oil may be fil led through the oil fill port only (k,88).
CAUTION
Du ring ope ra tion the oil se pa ra tor is fil led with hot, pres su ri sed oil
mist.
Risk of in ju ry from hot oil mist with open oil in let plug (k,88).
Re move the oil in let port (k,88) only the va cuum pump is stop ped.
The va cuum pump must only be ope ra ted with the oil in let plug
(k,88) firmly inserted.
●
Make sure that the va cuum pump is shut down and loc ked against
inad ver tent start up
●
Re move the oil in let port (k,88)
●
Top up oil un til the le vel rea ches the middle of the oil sight glass
(i,83)
●
Make sure that the le vel is bet ween the MIN and the MAX-mar -
kings of the oil sight glass (i,83)
●
Make sure that the sea ling seat (89) on the oil fill plug (k,88) is un -
da ma ged, if ne ces sa ry re place the oil fill plug
●
Firm ly rein sert the oil fill plug (k,89) with its sea ling seat (89)
Checking the Colour of the Oil
NOTE
: The oil should be light, ei ther trans pa rent, a little foa my or a
little tar nis hed. A mil ky dis co lou ra tion that does not va nish af ter se da -
tion of the oil in di ca tes conta mi na tion with fo reign ma te rial. Oil that is
ei ther conta mi na ted with fo reign ma te rial or burnt must be changed
(see “Oil Change”).
Oil Life
The oil life de pends very much on the ope ra ting condi tions. A clean
and dry air stream and ope ra ting tem pe ra tu res be low 100°C are ideal.
Maintenance
Page 10