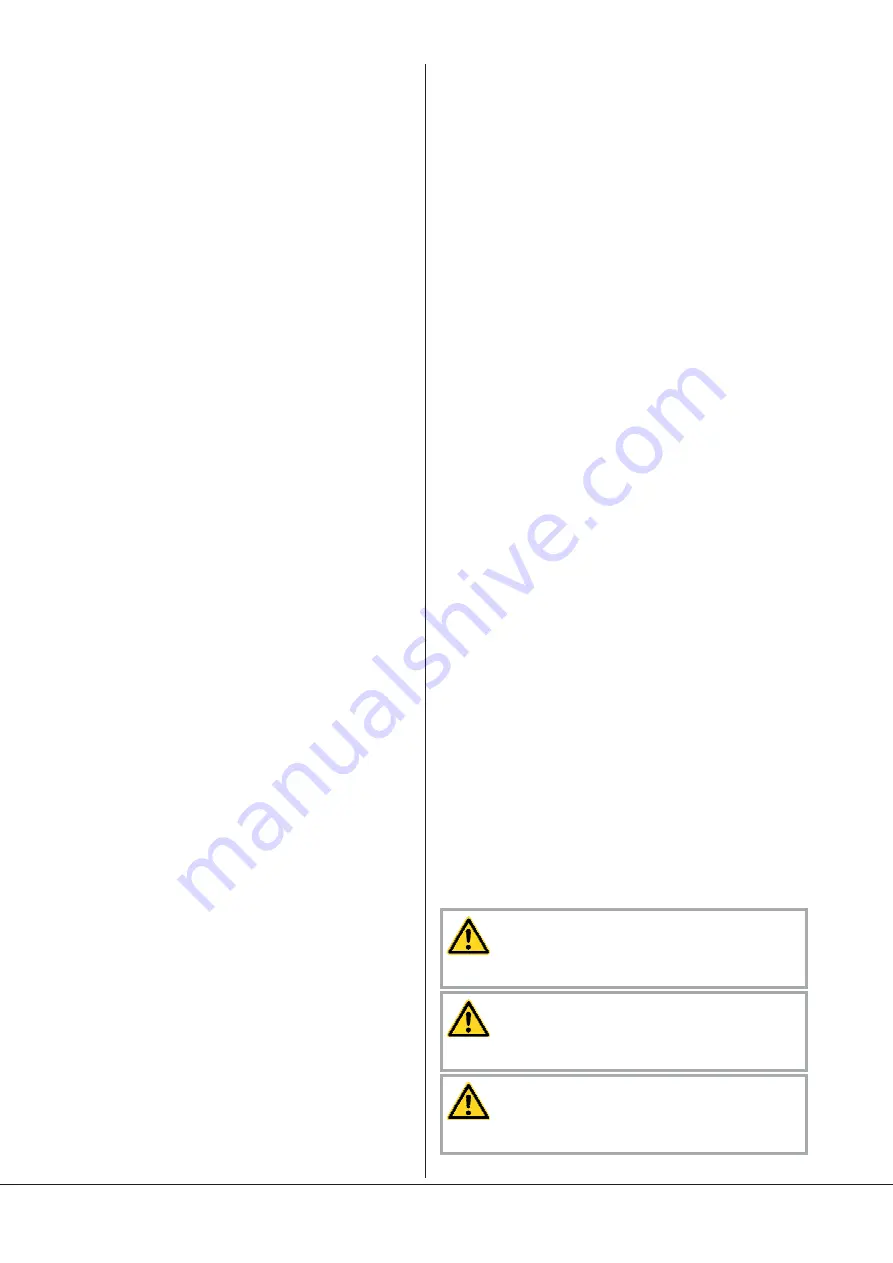
of the screws and the pump body. The gases are conveyed by the rota-
tion of the screws to the exhaust, where they are discharged.
The COBRA NW screw vacuum pumps are driven by water-cooled
motors.
Oil circuit
Since the complete operating principle works without contact, no oil
circuit is needed in the work area.
Cooling
The vacuum pump is cooled by
–
a cooling water circuit (4) in the cylinder and motor. This cooling
water circuit is used to cool the motor of the pump, the frequency
inverter and also the body of the NW pump.
NOTE
: The COBRA BC vacuum pumps are always delivered without oil
and without cooling water. Operation without these coolants can result
in damage to the vacuum pump.
Nitrogen system
The nitrogen system performs three main functions
–
nitrogen is used as dilution gas. It is injected inside the cylinder on
two different places. Nitrogen flow injected in the middle hole is
preset at 2 l/ min and can be adjusted with valve DGR 1, depen-
ding on the application. When flow is too low a warning then an
alarm signal is generated by flowmeter DGF to the PLC. Status of
the pump depends on the alarm function set by user (factory set-
ting : None, pump continues running with an alarm). Dilution im-
proves the screws functioning, especially when sucking corrosive
gases.
–
nitrogen is used as sealing gas. The nitrogen is injected between
the transmission and the process gas to achieve good closeness.
–
nitrogen is used as purge gas. The purge eliminates traces of gases
remaining in the vacuum pump. The vacuum pump purge cycle is
programmed in the control and starts, either after a STOP opera-
tion or after an alarm function.
For a correct purge execution, the shut-off valve at the inlet flange
must be closed. The purge cycle lasts about 30 min. (Program-
mable time in the basic parameters).
Optional functions/ Use of available
accessories
A heating jacket attached to the exhaust heats the exhaust up to the li-
mit of 130°C in order to eliminate any condensate.
A handle can be attached to the eyebolt screw in order to facilitate the
handle of the vacuum pump (option)
A pressure receiver mounted at the exhaust , controls the overpressure
at the exhaust. If overpressure is above 0,2 bar, pressure switch gives a
warning signal. If overpressure is above 0,3 bar an alarm is generated.
Status of the pump depends on the alarm function set by user (factory
setting: None, pump continues running with an alarm).
A temperature sensor mounted on the cylinder, measures the tempera-
ture inside the cylinder.
A silencer or sound absorber (optional) at the exhaust reduces the
noise of the pump and collects any condensate.
A leak-protection non-return valve (optional) at the exhaust traps the
condensate in the pump when the pump is switched off.
The LCD controller processes the data of the sensors (see chapter
“Communication with the equipment”) as follows:
–
discharge pressure
–
temperature in the cylinder and at the exhaust
–
current
–
nitrogen flow rate (dilution, sealing)
–
cooling water flow rate
–
speed
–
frequency
–
power
The data process with the C.M.S. (Central Monitoring System) (acces-
sory) has the same function as the LCD controller (see operating ins-
tructions of Central Monitoring System).
On/ Off switch
The vacuum pump is delivered with on/ off switch.
Versions
Further vacuum pump descriptions state the nominal displacement and
the design level.
Example: BC 0200 F
BC = standard version
0200 = 165 m
3
/h (80 Hz)
F = Design
Safety
Intended use
DEFINITION
: To rule out any misunderstanding, the term “handling”
of the vacuum pump covers transport, storage, installation and opera-
tion of the pump as well as effects on operating states and troublesho-
oting on the vacuum pump.
The vacuum pump is intended for industrial use. It may only be opera-
ted by qualified personnel.
The different application possibilities and limit values for operation des-
cribed in “Product description” and “Installation requirements” must
be observed by the manufacturer of the system into which the vacuum
pump is to be integrated and by users.
The need for personal safety regulations depends in principle on the
type of use. The operator must provide the users with the necessary
means and must inform his personnel about the dangers emanating
from the processed product.
The operator of the vacuum pump must observe the safety regulations
and must train and instruct his personnel accordingly.
Local regulations regarding the motors and electric control elements
must be observed when installing the pump in potentially explosive
environments.
The maintenance instructions must be followed and observed.
These installation and maintenance instructions must be read and un-
derstood before the vacuum pump is used. If you have any doubts,
contact your Busch representative.
Safety information
The vacuum pump is designed and manufactured in compliance with
the latest technical standards and safety regulations. Nevertheless an
element of residual risk remains.
Various safety instructions are to be found in this handbook and on the
pump. These instructions must be followed. You can recognise these
instructions by the signal words DANGER, WARNING and CAUTION,
which are defined as follows:
DANGER
Disregard of this safety instruction will always result in death, se-
rious injuries or severe damage.
WARNING
Disregard of this safety instruction may result in death, serious in-
juries or severe damage.
CAUTION
Disregard of this safety instruction may result in minor or moderate
injuries or damage.
Safety
BC 0200 F
Page 6
0870767417 (En)
Summary of Contents for COBRA BC 0200 F
Page 4: ...BC 0200 F Page 4 0870767417 En MB CPC DPS DGF DGR2 DGR1 PSA TS CWR CWM VFD...
Page 22: ...Note...
Page 23: ...Note...