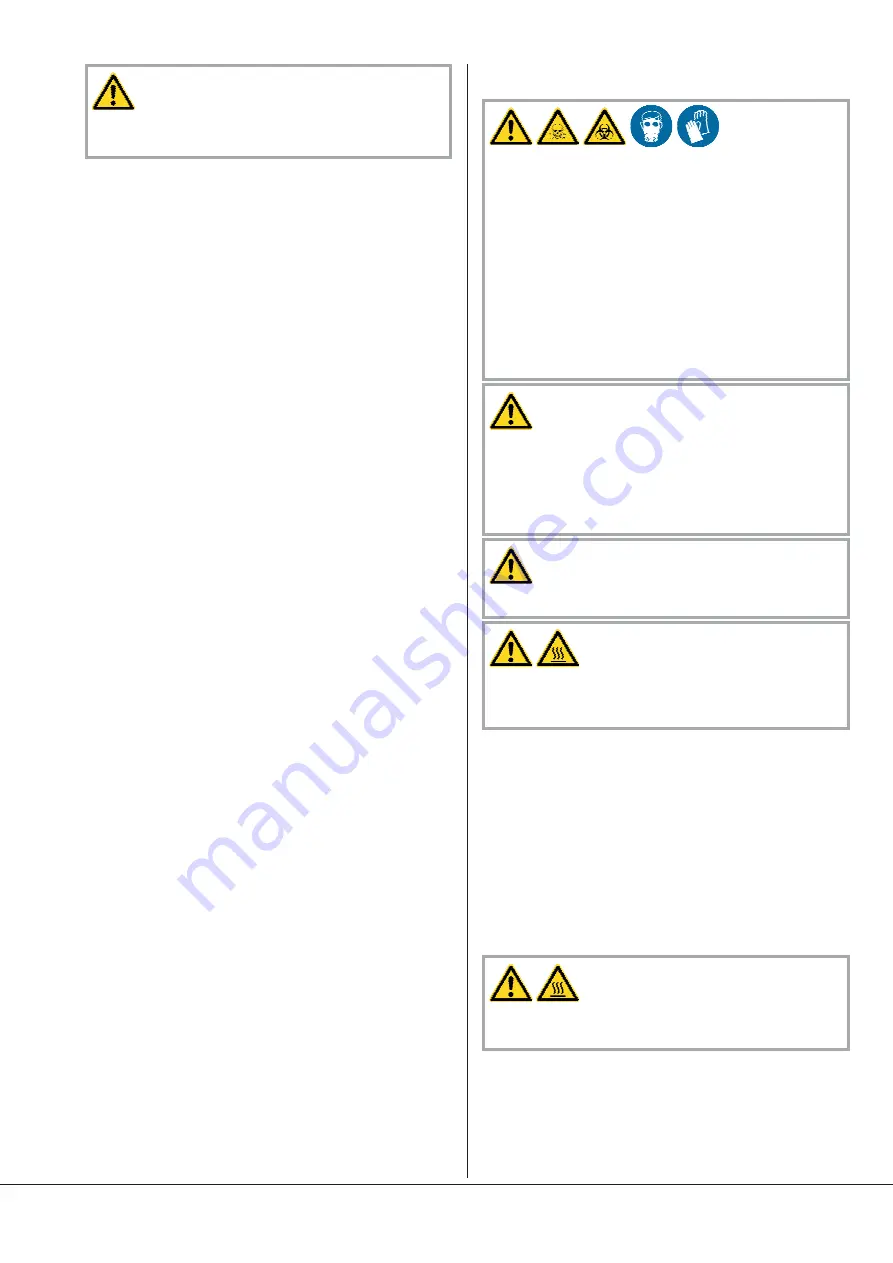
CAUTION
If there is a risk of frost, all the cooling water must be drained out
of the vacuum pump if the pump is shut down for a longer period
of time!
–
Drain the cooling water
u
Pull off the connections for the inlet and outlet of the cooling
water
u
Drain the cooling water completely
u
If necessary, drain the cooling water with the help of compres-
sed air to prevent any risk of frost or corrosion
Switching the vacuum pump on/ off
First start-up of the system
l
Make sure that the “Necessary installation instructions” are
followed
If the system is equipped with a solenoid gate valve in the cooling wa-
ter circuit:
u
Open the solenoid gate valve
l
Make sure that the cooling water flow is set correctly
–
The cooling water flow is factory set on 2 l/min and can be adjus-
ted at the regulating cock CWR. This water circuit is used to cool
the motor of the NW pump and also the body of the pump.
l
Make sure that the nitrogen flow is set correctly
–
dilution gas, injected in the cylinder is preset at 2 Nl/min and can
be adjusted with valves DGR 1 and DGR 2.
–
sealing gas, injected into the intermediate chamber in the cylinder
of the pump, between the drive and the process gas.
l
Switch on the vacuum pump
l
Make sure that the system does not leak
If the system is equipped with a solenoid gate valve at the intake:
u
Open the solenoid gate valve
Switching the system off
l
Flush the vacuum pump with nitrogen at the end of the process
(the duration of flushing can be programmed)
If the system is equipped with a solenoid gate valve at the intake:
u
Close the solenoid gate valve
l
Switch off the vacuum pump
l
Shut off the nitrogen supply
l
Shut off the cooling water supply
If the system is equipped with a solenoid gate valve in the cooling wa-
ter circuit:
u
Close the solenoid gate valve
l
Make sure that the system is currentless
Maintenance
DANGER
In case the vacuum pump has conveyed gases that have been
contaminated with foreign materials that are dangerous to health,
the oil and condensates will also be contaminated.
These foreign materials can infiltrate the pores, recesses and other
internal spaces of the vacuum pump.
Danger to health when the vacuum pump is dismantled.
Danger to environment.
Always wear protective clothing when carrying out maintenance
work.
Before any maintenance work, the inlet and outlet piping as well as
the vacuum pump itself must be flushed with nitrogen.
CAUTION
Only authorised personnel may carry out dismantling work on the
vacuum pump. Before work begins, the operator of the vacuum
pump must fill in a form or a “Declaration Regarding Contamination
of Equipment and Components” that provides information on pos-
sible dangers and appropriate measures.
If this form has not been filled in completely and signed, the
vacuum pump may not be dismantled.
CAUTION
Before maintenance work is started, a safety area of at least 610
[mm] around the machine must be set up.
CAUTION
The surface temperature of the vacuum pump can exceed 50°C
when the vacuum pump is in operation.
Danger of burns!
Before starting maintenance work, make sure that the vacuum pump
has been switched off and that it cannot be switched on again acciden-
tally. Follow the shutdown procedure in the section “Lock Out/ Tag
Out procedure”:
–
stop the pump with the remote control (press on STOP button
during 10s)
–
press on emergency stop button
–
switch off the main breaker
–
switch off the customer’s power supply
–
switch off the water and nitrogen quick connections (inlet first,
then outlet)
–
put the label or warning board “Maintenance processing” on or
next to the pump
CAUTION
The oil temperature can reach a value of 90°C!
Danger of burns!
l
Make sure that the oil circuit and the coolant circuit have been
emptied before moving the vacuum pump
l
Make sure that there are no cleaning tools in the pump anymore
according to local and national regulations
Before pulling off the different connections, make sure that the intake
and exhaust lines of the vacuum pump correspond to atmospheric
pressure
BC 0200 F
Maintenance
0870767417 (En)
Page 15
Summary of Contents for COBRA BC 0200 F
Page 4: ...BC 0200 F Page 4 0870767417 En MB CPC DPS DGF DGR2 DGR1 PSA TS CWR CWM VFD...
Page 22: ...Note...
Page 23: ...Note...