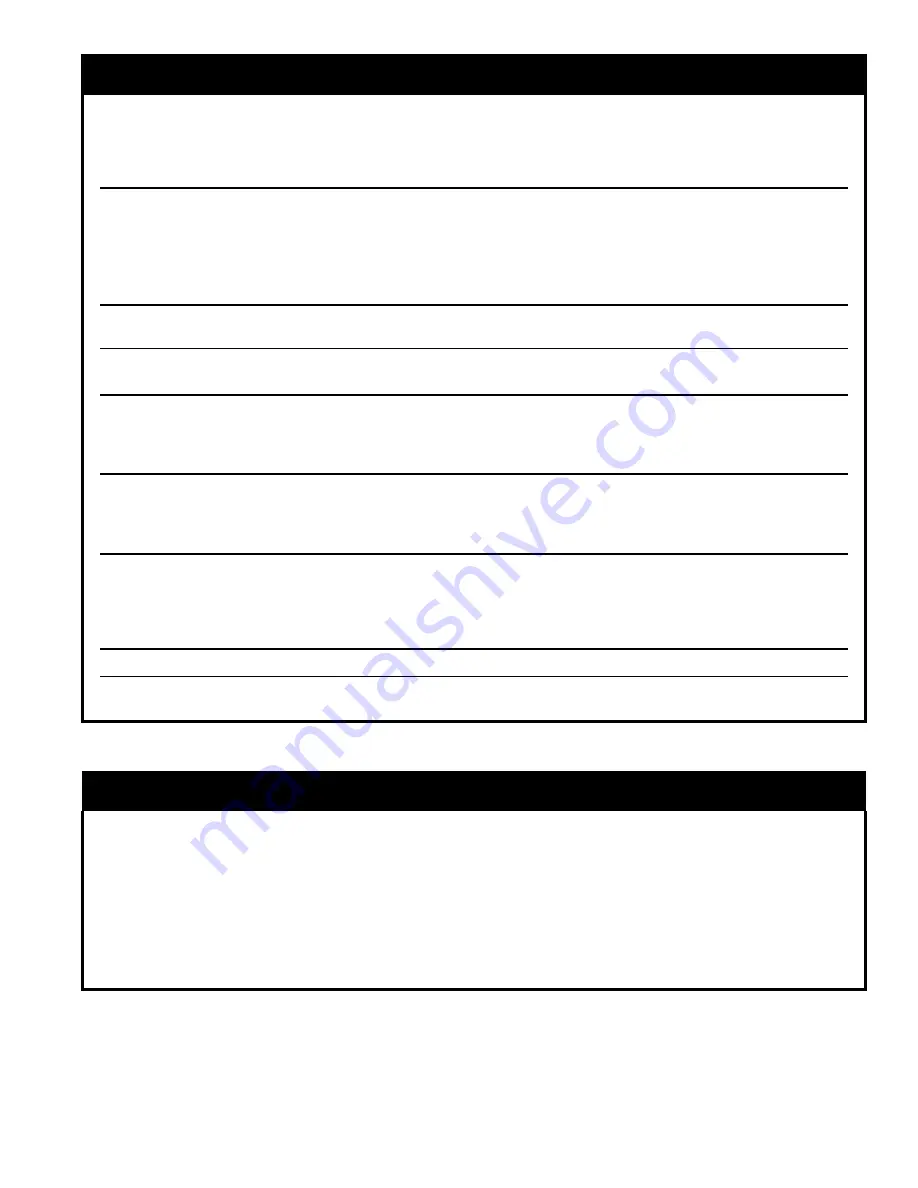
7
WARNING
Appliance materials of construction, products of combustion and the fuel contain alumina, silica, heavy
metals, carbon monoxide, nitrogen oxides, aldehydes and/or other toxic or harmful substances which
can cause death or serious injury and which are known to the state of California to cause cancer, birth
defects and other reproductive harm. Always use proper safety clothing, respirators and equipment when
servicing or working nearby the appliance.
This boiler contains very hot water under high pressure. Do not unscrew any pipe fittings nor attempt
to disconnect any components of this boiler without positively assuring the water is cool and has no
pressure. Always wear protective clothing and equipment when installing, starting up or servicing this
boiler to prevent scald injuries. Do not rely on the pressure and temperature gauges to determine the
temperature and pressure of the boiler. This boiler contains components which become very hot when
the boiler is operating. Do not touch any components unless they are cool.
This appliance must be properly vented and connected to an approved vent system in good condition.
Do not operate boiler with the absence of an approved vent system.
This boiler needs fresh air for safe operation and must be installed so there are provisions for adequate
combustion and ventilation air.
The interior of the venting and air intake systems must be inspected and cleaned before the start of the
heating season and should be inspected periodically throughout the heating season for any obstructions.
Clean and unobstructed venting and air intake systems are necessary to allow noxious fumes that could
cause injury or loss of life to vent safely and will contribute toward maintaining the boiler’s efficiency.
This boiler is supplied with controls which may cause the boiler to shut down and not re-start without
service. If damage due to frozen pipes is a possibility, the heating system should not be left unattended in
cold weather; or appropriate safeguards and alarms should be installed on the heating system to prevent
damage if the boiler is inoperative.
This boiler is designed to burn No. fuel oil only. Do not use gasoline, crankcase drainings, or any oil
containing gasoline. Never burn garbage or paper in this boiler. Do not convert to any solid fuel (i.e.
wood, coal). Do not convert to any gaseous fuel (i.e. natural gas, LP). All flammable debris, rags, paper,
wood scraps, etc., should be kept clear of the boiler at all times. Keep the boiler area clean and free of
fire hazards.
Always keep the oil supply valve shut off if the burner is shut down for an extended period of time.
Probe and float type low water cutoff devices require annual inspection and maintenance. Refer to
instructions in Section VI, Paragraph C for inspection and cleaning instructions.
NOTICE
Model MPC cast iron boilers are designed, built, marked and tested in accordance with the ASME Boiler
and Pressure Vessel Code, Section IV, Heating Boilers. An ASME Data Label is factory applied to each MPC
jacket, which indicates the boiler Maximum Allowable Working Pressure (MAWP). Each cast iron section is
permanently marked with the MAWP listed on the boiler’s ASME Data Label. This value for the MPC is as
follows:
MAWP, Water (USA and Canada) - 80 PSI
It is common and acceptable practice to install these boilers in lower pressure systems, below the boiler
MAWP. Therefore, Burnham offers safety relief valves set at or below the MAWP of the boiler. See Page 1
for available safety relief valve set pressures.
Summary of Contents for MPC
Page 19: ...19 Figure 5 Manual or Hydraulic Draw up Section Assembly ...
Page 28: ...28 Table VII Modular Return Water Mixing Tube RWMT RC ...
Page 29: ...29 Figure 13 Return Water Mixing Tube RC Assembly and Installation ...
Page 78: ...78 Figure 56 MPC Common Bare Boiler Components ...
Page 80: ...80 Figure 56 MPC Common Bare Boiler Components continued ...
Page 82: ...82 Figure 57 MPC Front Center Section Frame Rail Assembly ...
Page 84: ...84 Figure 58 MPC Rear Section Frame Rail Assembly ...
Page 86: ...86 Figure 59 MPC Return Water Mixing Tube RC Assembly ...
Page 88: ...88 Figure 60 MPC Heat Exchanger Insulation Wrapper ...
Page 90: ...90 Figure 61 MPC Internal Wiring Harness Components ...
Page 92: ...92 Figure 62 MPC Jacket Panel Assembly ...
Page 94: ...94 Figure 62 MPC Jacket Panel Assembly continued ...
Page 96: ...96 Figure 63 MPC 2 nd and 3 rd Pass Flueway Baffles ...