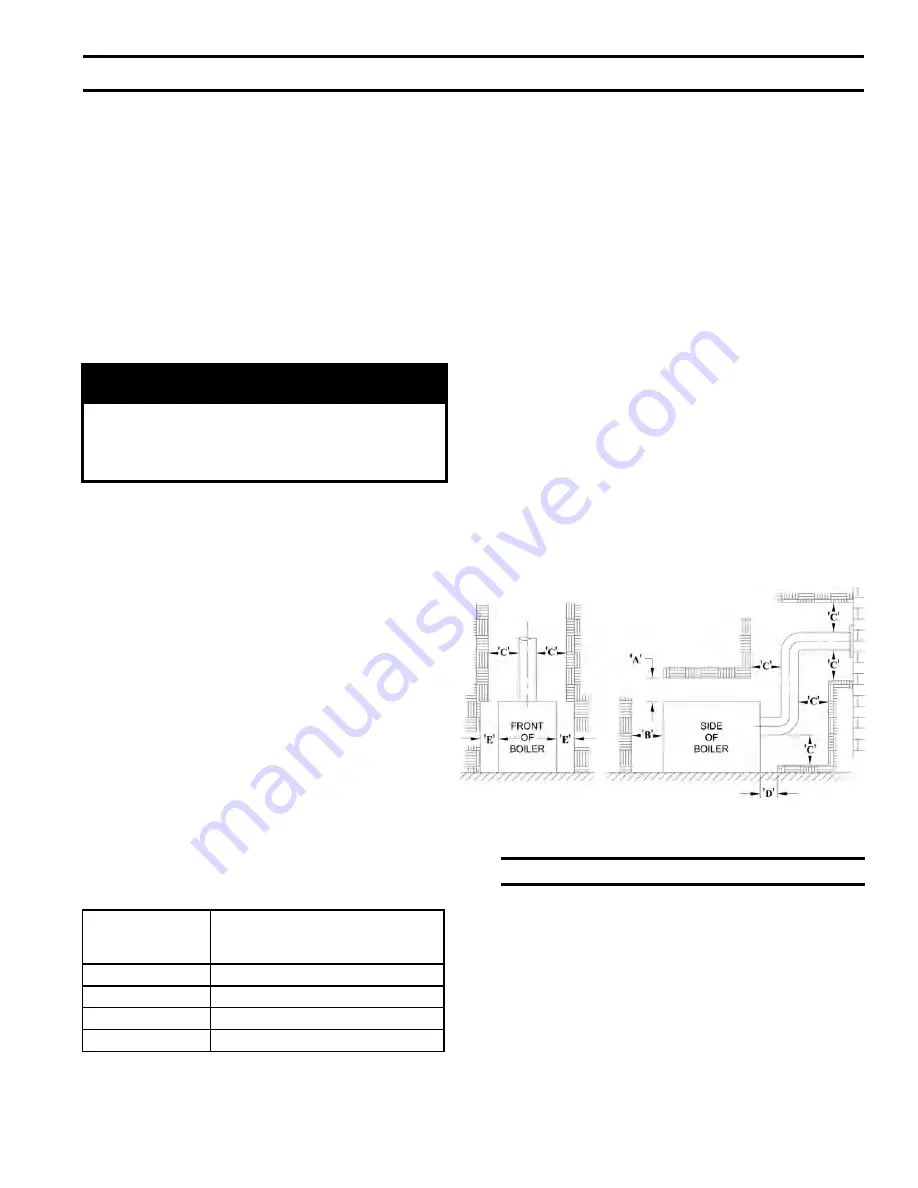
1
SECTION I - GENERAL INFORMATION (Continued)
A.
INSPECT SHIPMENT carefully for any signs of
damage.
1. ALL EQUIPMENT is carefully manufactured,
inspected and packed. Our responsibility ceases
upon delivery of crated Boiler to the carrier in good
condition.
2. ANY CLAIMS for damage or shortage in shipment
must be filed immediately against the carrier by
the consignee. No claims for variances from,
or shortage in orders, will be allowed by the
manufacturer unless presented within thirty (30)
days after the receipt of goods.
B.
LOCATE THE UNIT
NOTICE
Recommended clearance for service may be
reduced to minimum clearance to combustible
material.
However,
increased
service
and
maintenance difficulty will result.
1. RECOMMENDED SERVICE CLEARANCE
- Locate the unit in the boiler room so as to
provide ease of venting and adequate clearance
for maintenance, serviceability, and installation of
piping. Refer to Figure 1b and Table 1 for boiler
dimensional data.
from Jacket front Panel
:
•
Provide 54” service clearance for removal,
maintenance, and servicing of burner and
controls.
•
Provide service clearance for removal
of baffles to perform annual cleaning of
flueways, refer to Table I, Dimension “C”.
from Jacket Rear Panel
:
•
Provide a minimum service clearance from
the boiler jacket for access to boiler supply
and return piping, relief valve, drain valve,
flue collector clean-out covers, vent piping
and optional flue damper assembly. See
Table III.
Table IV: Minimum Installation Clearances To
Combustible Materials (Inches) per
ANSI/NFPA 1 (Knockdown/Non-UL
Packaged Boiler)
C
A
B
Chimney
D
E
Boiler
Above
Front
Connector
Rear
Sides
MPC
6
24
18
6
6
Note:
See Table III for recommended service clearance
to access rear of boiler.
from Jacket Left side Panel
:
•
Provide clearance per Table I, Dimension
‘B’, for burner swing door (BSD), opened
fully with burner mounted, otherwise 12”
with burner removed.
•
18” access clearance to service rear of boiler
if right side clearance is less than 12”.
•
12” minimum if right side clearance is 18”
or larger to access and service rear of boiler.
from Jacket Right side Panel
:
•
See Table I, Dimension ‘B’ if BSD is
hinged to swing to right side with burner
mounted, otherwise 12” minimum if left
side clearance is 18” or larger to access and
service rear of boiler.
from Jacket Top Panel
:
•
Provide a minimum clearance from the
boiler jacket of 24”.
2. FOR MINIMUM CLEARANCES to combustible
materials, See Table IV or Table V.
NOTE 1: Listed clearances comply with American National
Standard ANSI/NFPA 31, Installation of Oil Burning Equipment.
NOTE 2: MPC Series boilers can be installed in rooms with
clearances from combustible material as listed above. Listed
clearances cannot be reduced for alcove or closet installations.
NOTE 3: For reduced clearances to combustible material,
protection must be provided as described in the above ANSI/NFPA
31 Standard.
Table III: Recommended Rear Service Clearance
Flue Outlet Size
Combustible or Non-Combustible
Surfaces
7” Dia.
36
8” Dia.
36
10” Dia.
36
12” Dia.
36
Summary of Contents for MPC
Page 19: ...19 Figure 5 Manual or Hydraulic Draw up Section Assembly ...
Page 28: ...28 Table VII Modular Return Water Mixing Tube RWMT RC ...
Page 29: ...29 Figure 13 Return Water Mixing Tube RC Assembly and Installation ...
Page 78: ...78 Figure 56 MPC Common Bare Boiler Components ...
Page 80: ...80 Figure 56 MPC Common Bare Boiler Components continued ...
Page 82: ...82 Figure 57 MPC Front Center Section Frame Rail Assembly ...
Page 84: ...84 Figure 58 MPC Rear Section Frame Rail Assembly ...
Page 86: ...86 Figure 59 MPC Return Water Mixing Tube RC Assembly ...
Page 88: ...88 Figure 60 MPC Heat Exchanger Insulation Wrapper ...
Page 90: ...90 Figure 61 MPC Internal Wiring Harness Components ...
Page 92: ...92 Figure 62 MPC Jacket Panel Assembly ...
Page 94: ...94 Figure 62 MPC Jacket Panel Assembly continued ...
Page 96: ...96 Figure 63 MPC 2 nd and 3 rd Pass Flueway Baffles ...