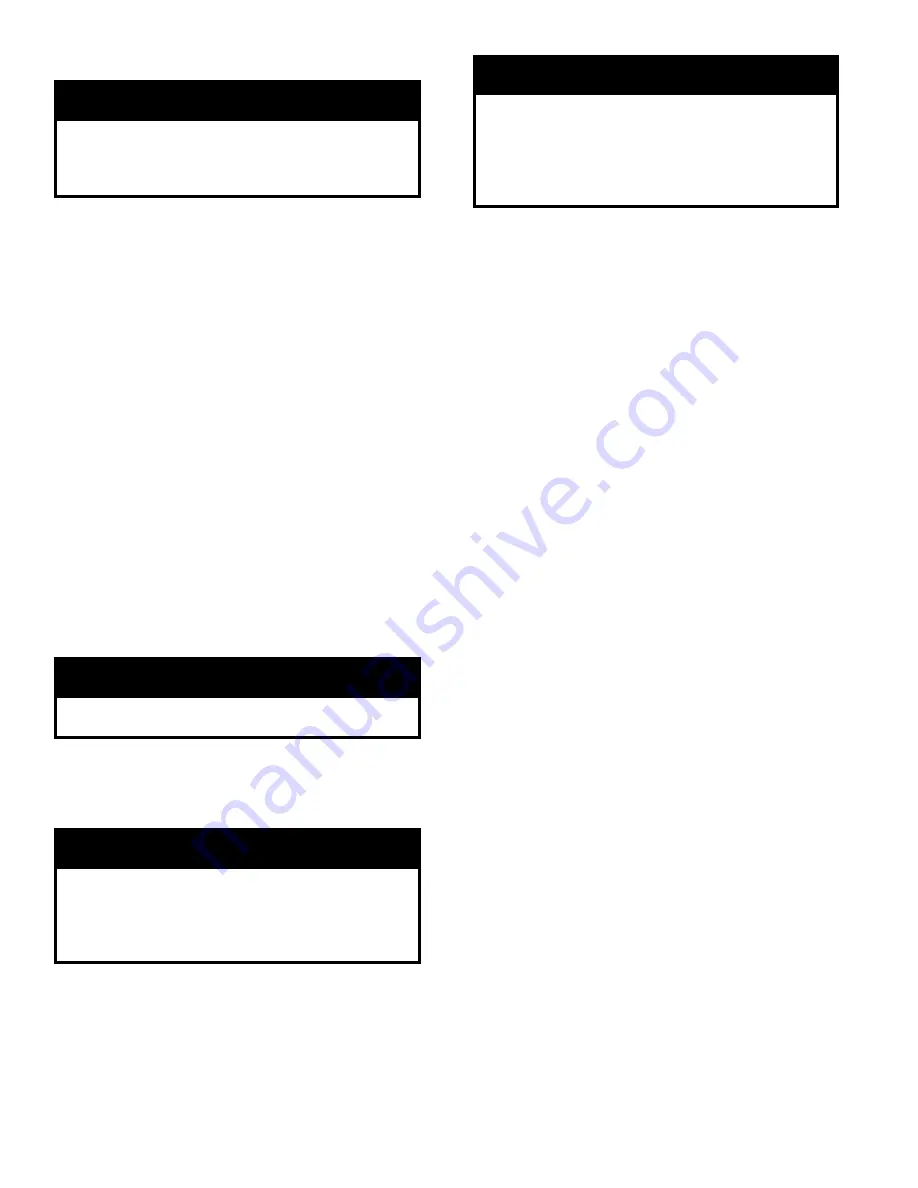
66
E.
TEsT cONTROLs
WARNING
Before installation of the boiler is considered
complete, the operation of the boiler controls
should be checked, particularly the low water
cutoff and the high limit control.
1. CHECK OPERATING CONTROL OPERATION.
Raise and lower operating control setting as required
to start and stop burner.
2. CHECK OPERATION OF HIGH LIMIT
CONTROL.
Jumper operating control terminals. Allow burner to
operate until shutdown by limit. Installation is not
considered complete until this check has been made.
REMOvE JUMPER.
3. CHECK LOW WATER CUTOFF CONTROL
Raise operating control setting to allow burner to
operate. Close isolation valves in supply and return
near boiler piping. Open boiler drain to allow water
level to drop until burner operation is shut down by
low water cutoff. If necessary, open relief valve for
air to facilitate draining.
Close boiler drain and refill boiler. Burner should
automatically restart during fill, unless low water
cutoff control requires manual reset. Close relief
valve when water flows out discharge piping.
OPEN sUPPLY AND RETURN isOLATiON
vALvEs.
REsET OPERATiNG cONTROL.
CAUTION
Probe and float type low water cutoff devices
require annual inspection and maintenance.
Refer to Section VI step (C) for proper cleaning
instructions.
f.
BOiLER AND sYsTEM cLEANiNG
(water side)
NOTICE
A qualified water treatment chemical specialist
should be consulted for recommendations
regarding appropriate chemical compounds and
concentrations which are compatible with local
environmental regulations.
WARNING
Chemicals used in treating boiler water are
toxic and/or harmful. Always use protective
clothing and equipment when working with/
near chemicals. Contact local authorities
to determine if treated boiler water can be
discharged into local waste water system.
1. Filling of Boiler and System --- General --- In a hot
water heating system, the boiler and entire system
(other than the expansion tank) must be full of water
for satisfactory operation. Water should be added to
the system until the boiler pressure gauge registers
normal system design operating pressure. To insure
that the system is full, water should come out of all
air vents when opened.
2. Boiling Out of Boiler and System. The oil and
grease which accumulate in a new hot water boiler
can be washed out in the following manner.
a. Remove safety relief valve using extreme care to
avoid damaging it.
b. Add an appropriate amount of recommended
boilout compound.
c. Reinstall safety relief valve.
d. Fill the entire system with water.
e. Start firing the boiler.
f. Circulate the water through the entire system.
g. Vent the system, including the radiation.
h. Allow boiler water to reach operating
temperature, if possible.
i. Continue to circulate the water for a few hours.
j. Stop firing the boiler.
k. Drain the system in a manner and to a location
that hot water can be discharged with safety.
l. Remove plugs from all available returns and
wash the water side of the boiler as thoroughly as
possible, using a high-pressure water stream.
m. Refill the system with fresh water.
3. Add appropriate boiler water treatment compounds
as recommended by your local qualified water
treatment company.
4. Make pH or Alkalinity Test.
After boiler and system have been cleaned and
refilled as previously described, test the pH of
the water in the system. This can easily be done
by drawing a small sample of boiler water and
testing with hydrion paper which is used in the
same manner as litmus paper, except it gives
specific readings. A color chart on the side of the
small hydrion dispenser gives the reading in pH.
Hydrion paper is inexpensive and obtainable from
any chemical supply house or through your local
druggist.
Summary of Contents for MPC
Page 19: ...19 Figure 5 Manual or Hydraulic Draw up Section Assembly ...
Page 28: ...28 Table VII Modular Return Water Mixing Tube RWMT RC ...
Page 29: ...29 Figure 13 Return Water Mixing Tube RC Assembly and Installation ...
Page 78: ...78 Figure 56 MPC Common Bare Boiler Components ...
Page 80: ...80 Figure 56 MPC Common Bare Boiler Components continued ...
Page 82: ...82 Figure 57 MPC Front Center Section Frame Rail Assembly ...
Page 84: ...84 Figure 58 MPC Rear Section Frame Rail Assembly ...
Page 86: ...86 Figure 59 MPC Return Water Mixing Tube RC Assembly ...
Page 88: ...88 Figure 60 MPC Heat Exchanger Insulation Wrapper ...
Page 90: ...90 Figure 61 MPC Internal Wiring Harness Components ...
Page 92: ...92 Figure 62 MPC Jacket Panel Assembly ...
Page 94: ...94 Figure 62 MPC Jacket Panel Assembly continued ...
Page 96: ...96 Figure 63 MPC 2 nd and 3 rd Pass Flueway Baffles ...