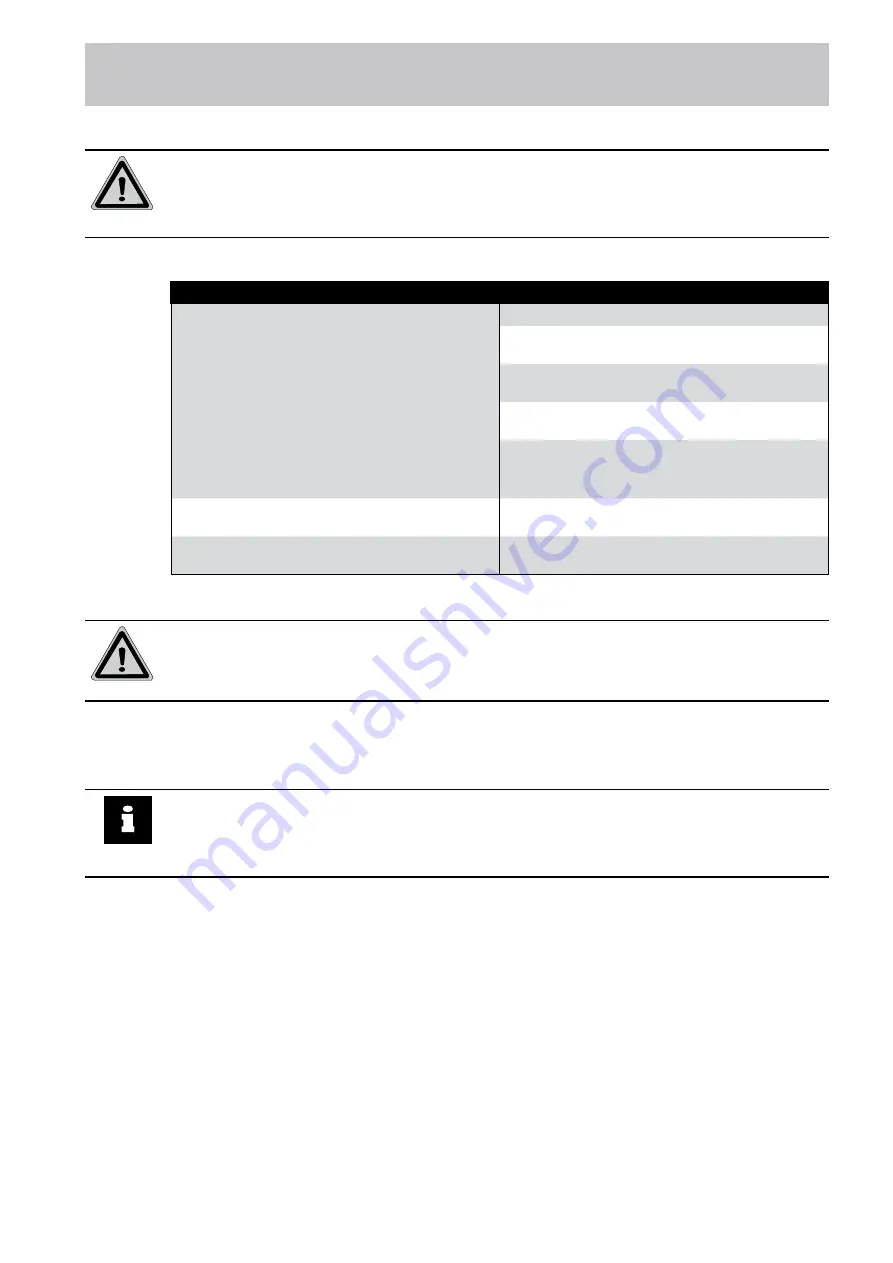
Maintenance / Servicing
37
8
Maintenance / Servicing
Danger!
Maintenance and service works may only be implemented by competent personnel.
Disregarding this note can cause damage to the tank system and/or injuries to the per-
sonnel.
8.1
Maintenance intervals
Interval
Activity
Daily
Check the tank system for completeness
Check all mechanical and electrical connections for
tight fit.
Remove hot melt material residues and other incrus-
tations from the tank system.
Check the tank for impurities and foreign objects
(remove immediately as necessary).
For tank systems with spray-air adapter kits:
Drain the maintenance unit. Replace the dirty filter
as needed.
Every 500 operating hours
Check the gear wheel pump for hot melt material
discharge.
Every 3 years
Replace the battery of the realtime clock in the con-
trol unit (see Chap. 8.3).
8.2
Cleaning
Attention!
Do not use any aggressive solvent or combustible cleaning agents to clean the tank sys-
tem and its components. Such substances can cause damage to the tank system.
Using a suitable tool (e.g. cloth, soft brush, wood spatula), mechanically remove hot melt
material residue and other pollution, especially from the inside walls of the tank.
To clean the conveying route, carry out the following work steps:
Info
Before cleaning the conveying routes, have your hot melt material manufacturer inform
you about suitable cleaning agents. Observe the processing data sheet and the security
advice contained therein.
1. Make sure that only minor amounts of hot melt material residue is in the tank.
2. Fill the cleaning agent into the tank. Place a collection basin under the nozzle of the
manual application unit.
3. Activate the trigger of the manual application unit until the cleaning agent has com-
pletely run through.
4. Fill fresh hot melt material into the tank. Continue activating the trigger of the manual
application unit until only hot melt material (without any cleaning agents) is dis-
charged.
Summary of Contents for HB 5010
Page 10: ...2...
Page 14: ...Special security advice 6...
Page 16: ...Technical data 8 Figure 2 1 2 Location of type plate on the inside of the unit...
Page 28: ...Operation 20...
Page 40: ...Operation 32...
Page 57: ...Repairs 49...
Page 60: ......
Page 62: ...Table of Contents 4 Table of contents...
Page 64: ...Specific security advice 6...
Page 68: ...Technical Data 10...
Page 76: ...Maintenance 18...
Page 80: ......
Page 82: ...4 Inhaltsverzeichnis...
Page 84: ...Specific safety instructions 6...
Page 90: ...Construction and function 12...
Page 92: ...Technical data 14...
Page 104: ...What happens if 26...
Page 107: ...Accessories 29...
Page 110: ...Ersatzteillisten...
Page 115: ...Spare parts list 3 1 HB 5010 Tank System basic unit Fig 1 1 Spare parts for basic unit Part 1...
Page 128: ...Spare parts list 16 2 3 Spare parts bead and spray 19 9 Fig 2 11 Grip casing both versions...
Page 129: ...Spare parts list 17 11 Fig 2 12 Heat insulation half shell both versions...
Page 130: ...18 Spare parts list 10 Fig 2 13 Trigger and mounting parts both versions...
Page 133: ...Table of contents 21...
Page 136: ...Table of Contents 2...
Page 138: ...4...