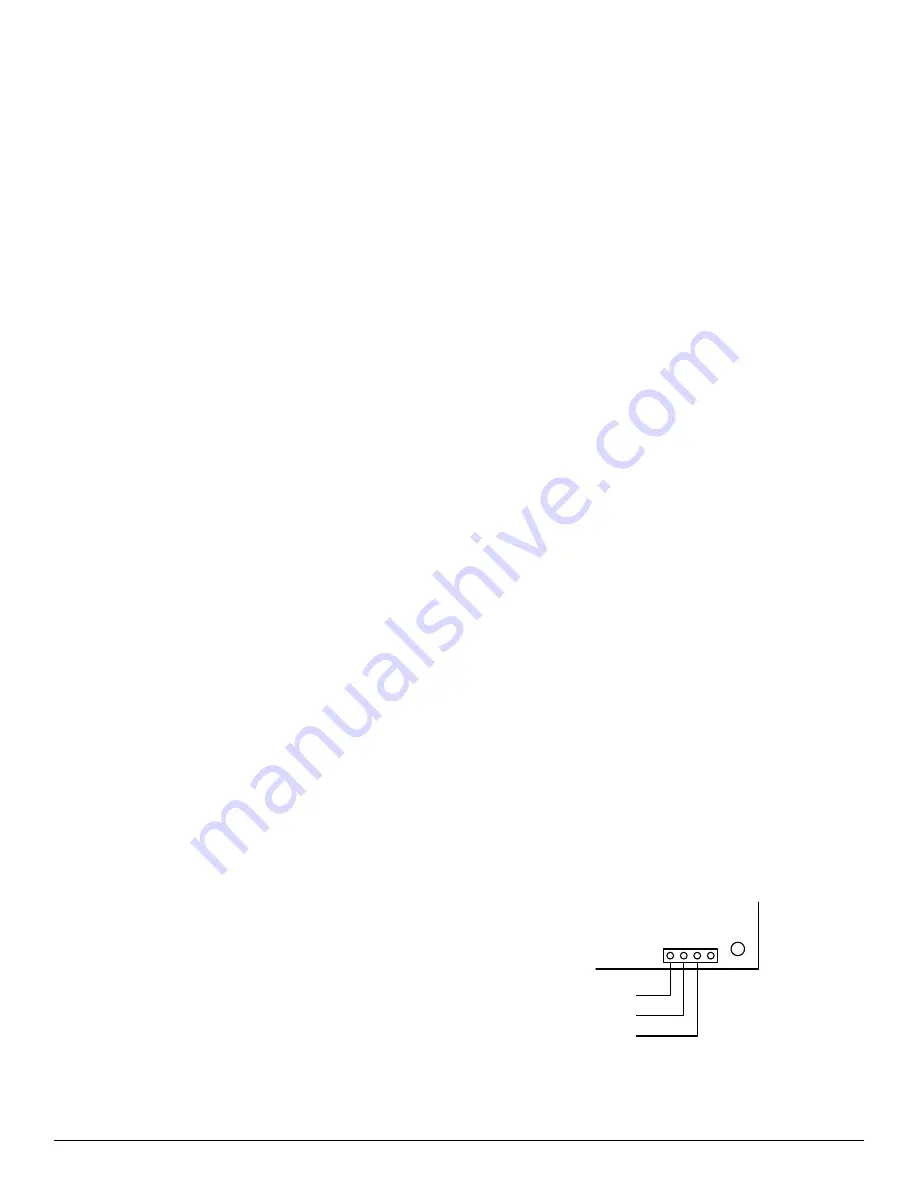
186CNV / 284ANV: Service Manual
Manufacturer reserves the right to change, at any time, specifications and designs without notice and without obligations.
5
Variable Frequency Drive (VFD)
The VFD converts single phase 60 Hz line power into a variable
frequency, variable voltage, 3-phase output to drive the compressor at
the speed requested by the control system. This function is performed
by first converting the incoming line power to an intermediate high
voltage DC supply. The high voltage DC supply is then converted to a
3-phase output by a variable frequency inverter for driving the
compressor. The VFD also provides high voltage DC supply power to
the fan motor.
The VFD contains numerous protection modes for maximizing
reliability and preventing faults in wiring or the compressor and fan
components from causing failures within the VFD.
VFD Filter Board
The VFD filter board blocks electrical noise generated within the VFD
from back-feeding onto the line power feed to the equipment. It contains
non-replaceable fuses which will protect the VFD in the event of a
severe power surge condition.
Reactors
Reactors are part of the VFD incoming power conversion circuit. The
reactors enable boosting of incoming line power when necessary and
also provide power factor correction.
High Pressure Switch (HPS)
The HPS is a normally closed switch connected to VFD control circuitry.
The HPS opens when the compressor discharge pressure reaches 670
psig. When the switch opens, a control input to the VFD is disabled and
causes the compressor and fan to shut down. When compressor
discharge pressure decreases to 470 psig, the switch closes and allows
equipment operation to resume.
Compressor Brushless Permanent Magnet Motor
(BPM)
The compressor uses a highly efficient, brushless permanent magnet
motor. Motor speed is synchronized to, and controlled by the frequency
of the drive provided by the VFD.
VFD + Compressor BPM
Compressor runs at variable speeds controlled by the VFD.
The VFD controls acceleration and deceleration speeds of the
compressor. Speed changes are typically limited to 60 rpm per second.
The VFD will automatically limit compressor speed if compressor load
current reaches operating limits.
Fan Brushless Permanent Magnet Motor (BPM)
The fan uses a highly efficient, brushless permanent magnet motor.
Motor speed is synchronized to, and controlled by an on-board variable
frequency inverter (VFI) integrated with the motor and located within
the motor housing. The VFI uses the high voltage DC supply provided
by the VFD to drive the fan, and a low voltage control signal from the
VFD to determine fan speed. The fan provides a feedback signal to the
VFD indicating fan speed.
VFD + Fan BPM
The fan runs at a variable speed over a range of 200 rpm to 800 rpm
depending on air movement requirements.
The fan on-board VFI will automatically limit fan speed if fan load
current reaches operating limits.
Crankcase Heater
Some equipment has a crankcase heater band installed around the
compressor case near the bottom of the compressor. The heater is
energized when the outdoor ambient temperature drops below 65°F and
is de-energized when the outdoor ambient temperature goes above 85°F.
This prevents liquid refrigerant from accumulating in the compressor by
ensuring that the compressor is not the coldest part of the system. The
crankcase heater operates independently of indoor equipment and
Evolution Control and functions as needed any time the outdoor
equipment is powered.
CONTROL SUB-SYSTEM
The control sub-system provides the connection point for low voltage
field communication and control wiring. The control sub-system
controls all operation of the equipment.
Primary Control Module (PCM)
The PCM is the heart of the equipment control system. The PCM is the
connection point for all control components except for the high pressure
switch and the crankcase heater.
The PCM receives equipment control requests from a communicating
Evolution Control or from a non-communicating control (traditional
thermostat) in an emergency operating mode.
The PCM receives signals from numerous sensors, including:
• 4 thermistors: OAT, OCT, OST, PDT
• 2 pressure transducers: SPT, DPT.
The PCM controls numerous actuators and signals, including:
• 3 control solenoids: PEV, RVS and LLS
• 2 electronic expansion valves: EXV-H, EXV-VI
• VFD Control Interface
• Emergency Mode 24VAC Control Signals: O and W
The PCM performs numerous diagnostics and supports 120 diagnostic
codes. Each of these codes is described in the Troubleshooting section.
Diagnostics cover the following:
• Line voltage and communication
• Equipment configuration (model plug, etc.)
• Compressor and fan operation
• Sensors
• Actuators
The PCM contains indicators and displays to provide operating status
and conditions. The PCM also supports communication with the Bryant
Service Tech App through the Bluetooth Module which provides
detailed diagnostic information and reprogramming capability.
Control Connection (Communicating and
Non-Communicating)
The primary system control interface for the PCM is the communicating
Evolution Control. The PCM also supports traditional 24VAC discrete
control signals in an emergency mode of operation when a
communicating control is not available.
Communicating
Evolution
Control
The communicating Evolution Control uses a 2-wire connection as
shown in
and Fig. 4. An optional 3rd wire can be added for a
ground connection. The third wire is recommended for long
communication runs or if there are problems encountered with consistent
communication using a 2-wire setup. The Comm light indicates whether
communication is being received from a system control.
A200239
Fig. 4 – Evolution Control Connection
A B C
A
B
GND
(oponal)