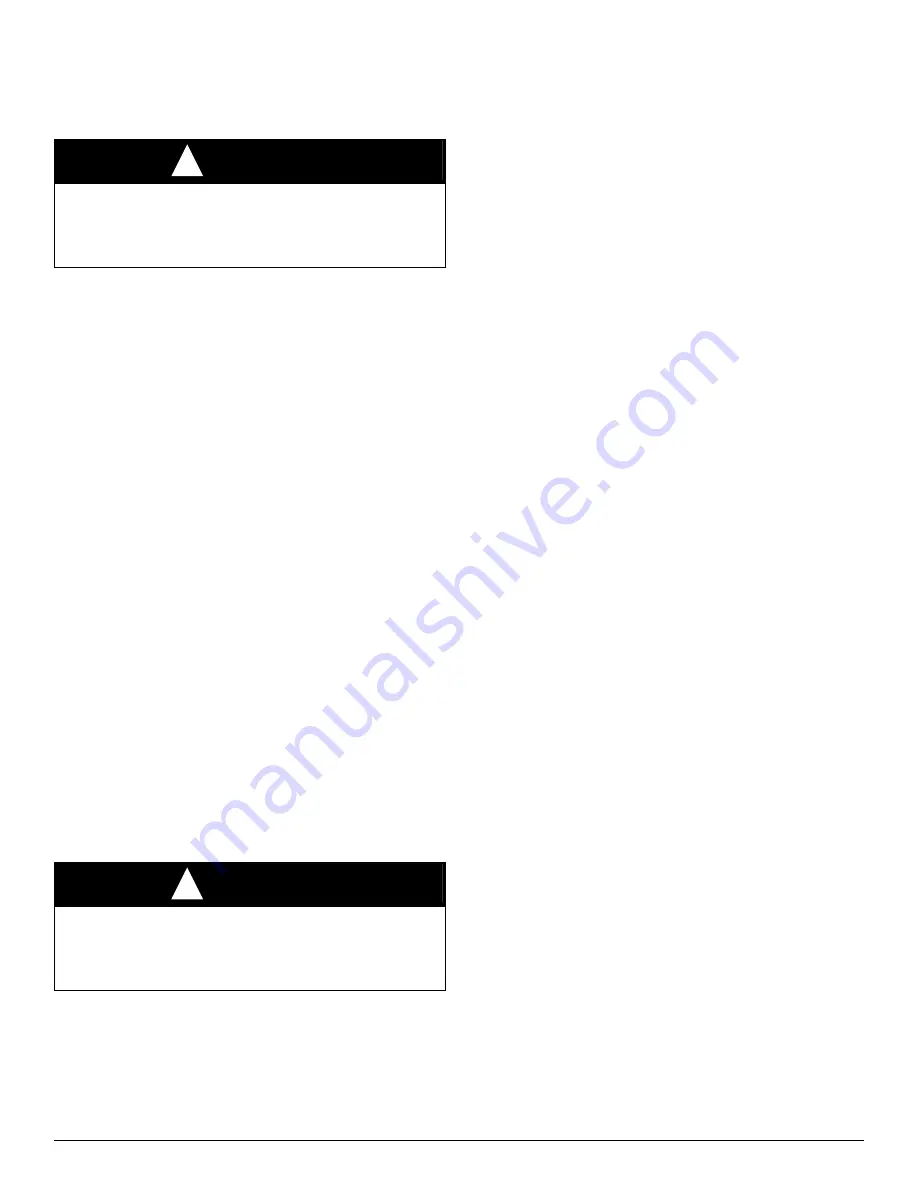
186CNV / 284ANV: Service Manual
Manufacturer reserves the right to change, at any time, specifications and designs without notice and without obligations.
35
The service valve cannot be field repaired; therefore, only a complete
valve or valve stem and service-port caps are available for replacement.
If the service valve is to be replaced, a metal barrier must be inserted
between the valve and the unit to prevent damaging the unit exterior
from the heat of the brazing operations.
Pumpdown & Evacuation
If this system requires either a Pump Down or Evacuation for any
reason, the procedures below must be followed:
Pump Down
Because this system has an inverter controlled, compressor, suction
pressure transducer and EXV, conventional procedure cannot be used to
“pump down” and isolate the refrigerant into the outdoor unit. The UI
(User Interface) has provisions to assist in performing this function.
1. Connect gages to outdoor unit liquid and vapor or suction capillary
service ports to monitor operating pressures during and at
completion of the procedure.
2. In the "installation and service" menu of the wall control, go to
"refrigerant charging" and then "pump down
3. Select mode to pump down in (COOL or HEAT), COOL mode
allows refrigerant to be isolated in outdoor unit. HEAT mode allows
the refrigerant to be isolated in indoor coil and lineset. Set desired
time period. Default time period for the procedure is 120 minutes.
4. Select ”Start” on wall control to begin the pumpdown process. Unit
will begin running in selected mode after a brief delay and a status
screen will be displayed.
5. Close the liquid service valve.
6. The unit will run in selected mode with the low pressure protection
set to indicate pumpdown is complete when the suction pressure
drops below 20 psig. Compressor protections are still active to
prevent damage to the compressor or inverter (high pressure, high
current, etc.).
7. Once system indicates pumpdown complete or failure to complete
shutdown, close vapor service valve.
8. A recovery system will be required to remove final quantity of
refrigerant from indoor coil and line set.
9. Remove power from indoor and outdoor unit prior to servicing unit.
NOTE:
A small quantity of charge remains in the OD unit that must be
manually recovered if isolating refrigerant to indoor coil and lineset via
HEAT mode PUMP DOWN.
Evacuation and Recovery of Refrigerant from 284ANV
NOTE:
All outdoor unit coils will hold only factory-supplied amount of
refrigerant. Excess refrigerant, such as in long-line applications, may
cause unit to relieve pressure through internal pressure-relief valve
(indicated by sudden rise of suction pressure) before suction pressure
reaches 5 psig (35kPa). If this occurs, shut unit off immediately, front
seat suction valve, and recover remaining pressure. connection to the
suction port of the compressor.
Reversing Valve (284ANV)
In heat pumps, changeover between heating and cooling modes is
accomplished with a valve that reverses flow of refrigerant in system.
This reversing valve device is easy to troubleshoot and replace. The
reversing valve solenoid can be checked with power off with an
ohmmeter. Check for continuity and shorting to ground. With control
circuit (24v) power on, check for correct voltage at solenoid coil. Check
for overheated solenoid.
NOTE:
Reversing valve diagnostic can only detect an open coil when
reversing valve is not energized, thus a damaged coil during cooling
operation will not trigger diagnostic. In this case the HP will operate in
heating mode when wall controller is requesting cooling operation.
Manual troubleshooting of coil will be required to confirm failure.
With unit operating, other items can be checked, such as frost or
condensate water on refrigerant lines.
The sound made by a reversing valve as it begins or ends defrost is a
"whooshing" sound, as the valve reverses and pressures in system
equalize. An experienced service technician detects this sound and uses
it as a valuable troubleshooting tool.
Using a remote measuring device, check inlet and outlet line
temperatures. DO NOT touch lines. If reversing valve is operating
normally, inlet and outlet temperatures on appropriate lines should be
close to each other. Any difference would be due to heat loss or gain
across valve body. Temperatures are best checked with a remote reading
electronic-type thermometer with multiple probes. Route thermocouple
leads to inside of coil area through service valve mounting plate area
underneath coil.
show test points (TP) on reversing
valve for recording temperatures. Insulate points for more accurate
reading.If valve is defective:
1. Shut off all power to unit and remove charge from system.
2. Remove solenoid coil from valve body. Remove valve by cutting it
from system with tubing cutter. Repair person should cut in such a
way that stubs can be easily re-brazed back into system. Do not use
hacksaw. This introduces chips into system that cause failure. After
defective valve is removed, wrap it in wet rag and carefully unbraze
stubs. Save stubs for future use. Because defective valve is not
overheated, it can be analyzed for cause of failure when it is
returned.
3. Braze new valve onto used stubs. Keep stubs oriented correctly.
Scratch corresponding matching marks on old valve and stubs and
on new valve body to aid in lining up new valve properly. When
brazing stubs into valve, protect valve body with wet rag to prevent
overheating.
4. Use slip couplings to install new valve with stubs back into system.
Even if stubs are long, wrap valve with a wet rag to prevent
overheating.
5. After valve is brazed in, check for leaks. Evacuate and charge
system. Operate system in both modes several times to be sure
valve functions properly.
CAUTION
!
PERSONAL INJURY HAZARD
Failure to follow this caution may result in personal injury.
Wear safety glasses, protective clothing, and gloves when handling
refrigerant.
CAUTION
!
ENVIRONMENTAL HAZARD
Failure to follow this caution may result in environmental damage.
Federal regulations require that you do not vent refrigerant to the
atmosphere. Recover during system repair or final unit disposal.