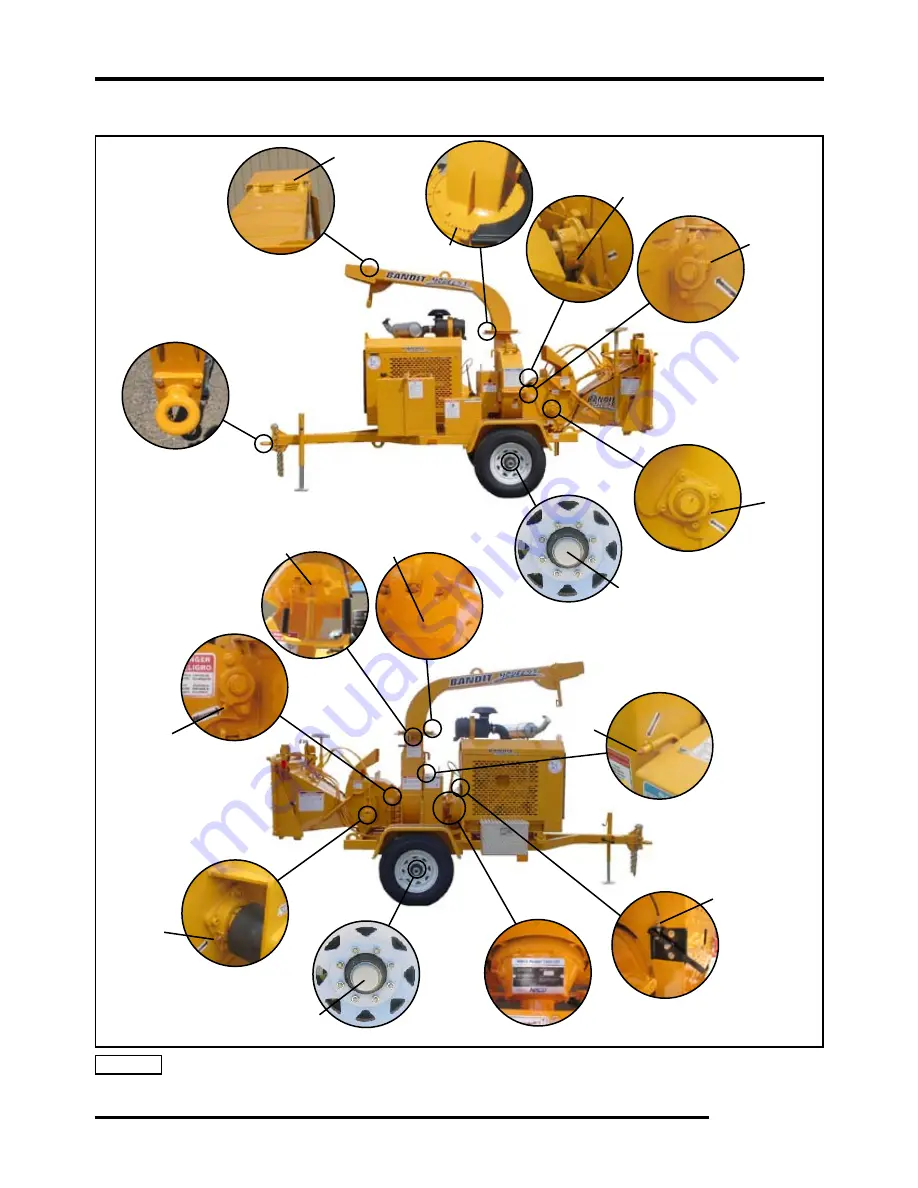
Bandit
Copyright 1/10
PAGE 9
MODELS 65XP(XL)/95
MAINTENANCE SECTION
LUBRICATION CHART
NOTICE Use as a reference only, locations may vary depending on options or component manufacturer.
Lubrication point instructions are described on the machine, in the Lubrication & Coolant Section
and Maintenance Section of this manual, or component manufacturer’s manual.
11
9
7
8
10
11
1
1