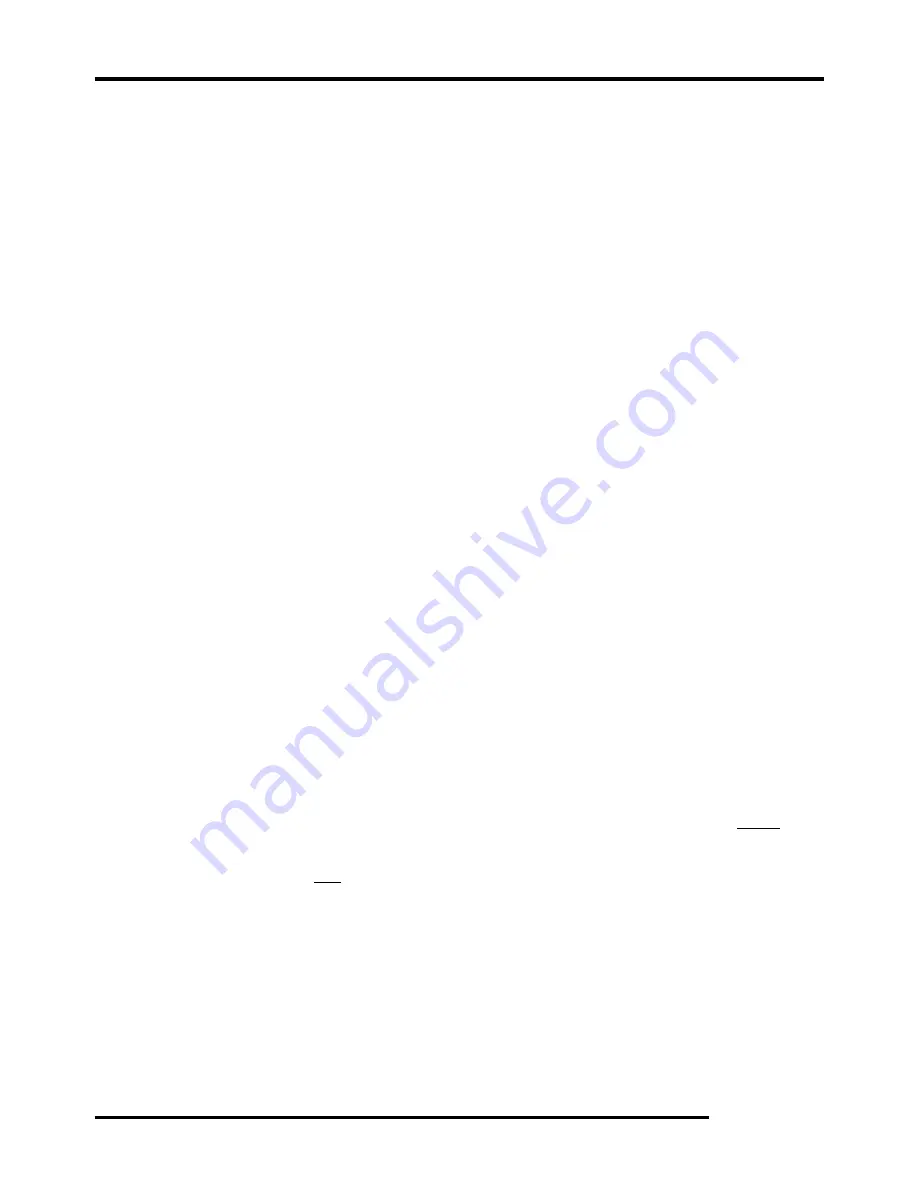
Bandit
Copyright 1/10
PAGE
MODELS 65XP(XL)/95
MAINTENANCE SECTION
DAILY START UP & MAINTENANCE (cont.)
13) Grease yoke pivot bearings:
Grease yoke pivot bearings with one shot of an
EP-2 Lithium type grease. Wipe off excess grease.
Excessive grease will attract dirt.
14) Check / adjust the chipper drive belt tension:
The belts will need to be tightened several times in the
first few days of operation. A loose belt will slip and
then glaze over. Once they slip you must replace them.
Check hydraulic pump drive belts also if equipped. See
pages - for procedures.
15) Check the hydraulic pump and motor shafts:
Check the hydraulic pump and hydraulic motor shafts
for fit and tightness.
16) Check hydraulic oil level:
The hydraulic oil reservoir tank level should always
remain at 7/8 full. Remember to check DAILY to avoid
excessive heat build up.
17) Check for any fluid leaks:
Inspect for any oil, fuel, hydraulic oil, or engine
coolant leaks. Check all hoses, fittings, lines, and
tanks. DO NOT use fingers or skin to check for
hydraulic leaks. Repair or replace any damaged or
leaking components.
18) Check hydraulic control valves:
Inspect all hydraulic control valves and insure they
operate smoothly and shift correctly.
19) Check the fuel level:
Check the fuel level, running out and repriming is time
consuming. Do not over fill, and you must leave fuel
expansion space in the top of the tank.
20) Check engine oil and coolant level:
Follow the engine manufacturer manual
recommendations for fluid levels. You MUST
follow
specific ENGINE MFG. manual recommendations for
radiator coolant, additives, lubrication, correct engine
speed, ETC.
21) Check radiator, debris screen:
Thoroughly clean radiator fins at least once a day and
twice in excessive conditions. Make sure debris is not
packed between fins. Use pressurized water spray to
clean. Do not rely on air pressure. The radiator will
only appear to be clean. A partially plugged radiator will
not allow the engine to cool properly. Clean cooling fan,
shroud on air cooled engines, and the debris screen
(if so equipped). Improper service, maintenance, or
neglect will cause overheating problems and engine
failure.
7) Check chipper disc assembly:
Check for elongated bolt holes, secure welds, torqued
bolts, excessive wear and impact cracks. If a problem
is found contact the chipper manufacturer or an
authorized Bandit dealer. Also check the chipper
housing at this time. Check the chipper base, belly
band, and hoods for wear or damage. Also inspect
the chipper bearings.
8) Check chipper disc/drum to turn:
Very carefully, manually with a pry bar or wood bar,
turn the chipper disc/drum a full revolution. This is to
ensure the anvil and knives have proper clearance. If
the chipper disc/drum is jammed with debris or frozen in
place, DO NOT attempt to start the engine and engage
clutch until the chipper disc/drum rotates freely.
9) Check the condition of your fan blades,
knives, anvil, and attaching hardware:
Grind, file, or replace your knives to keep them sharp.
Check the fan blades, anvil, and attaching hardware
for the knives and anvil. Replace if necessary.
10) Properly torque the knife mounting hardware:
All knife mounting hardware must be factory approved.
Knife mounting hardware must be replaced after
maximum of 4-5 knife rotations/changes to insure safe
clamping ability.
Torque set, AT ALL TIMES to:
See TORQUE CHART on page 45.
11) Hood lock pin and padlock:
After closing chipper hood, reinsert the hood pin and
padlock, make sure pin is tight and secure. If worn
replace immediately. Don’t use a worn or makeshift
hood pin. Make sure the spring lock for the hood pin is
in the correct position on disc chippers. Make sure the
chipper hood engine disable plug is installed correctly
and that it is also operating properly.
12) Grease all feedwheel and chipper bearings daily:
Use an EP-2 Lithium type grease
only for all bearings.
Purge chipper bearings with grease. You can not over
grease these bearings. Grease feedwheel bearings
with one shot of grease. Both types of bearings
are designed with a relief system that will not allow
over greasing. In other words, you can not hurt the
bearing seals by pumping in too much grease. Most
of the failures related to bearings are diagnosed as
“Contamination”. Contamination is caused by improper
lubrication. Wipe off excess grease.
Excessive
grease will attract dirt.