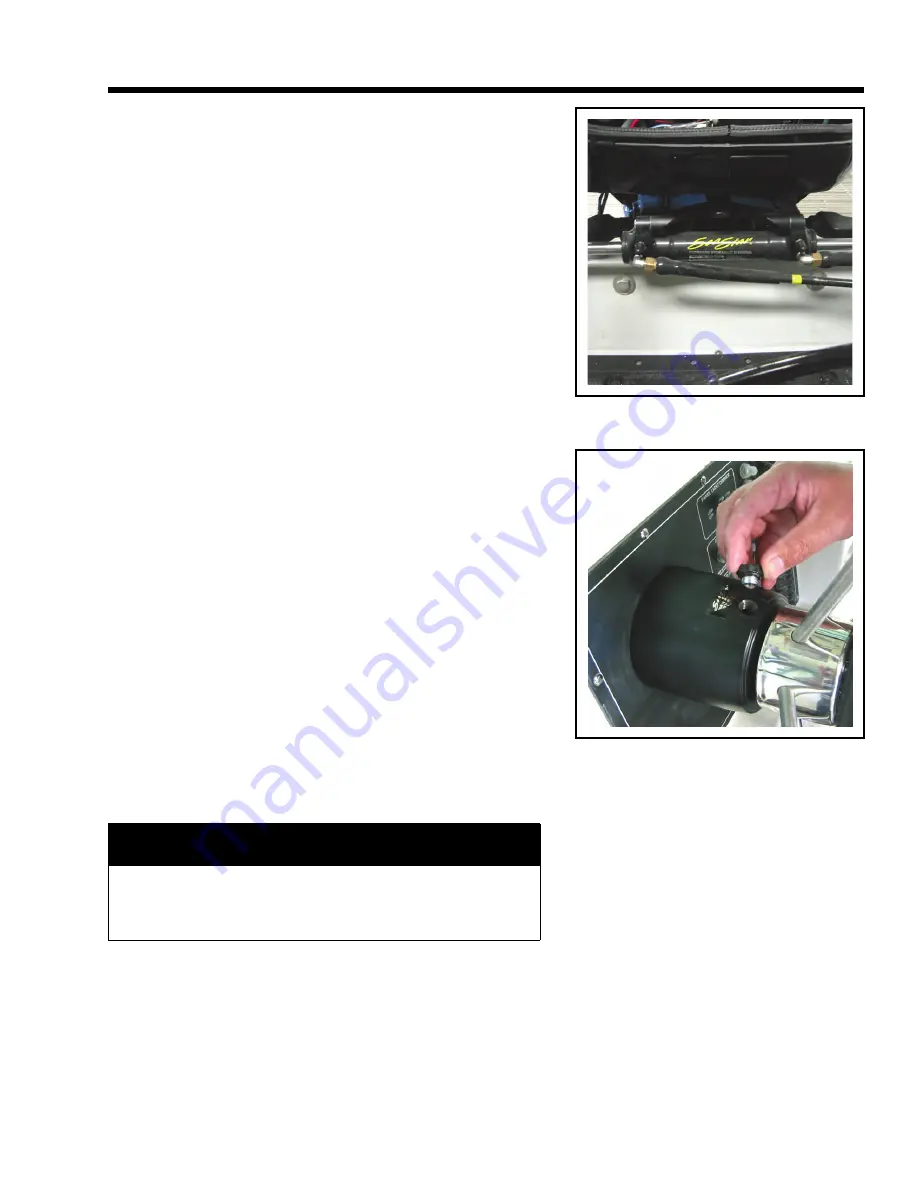
6-13
Boat Maintenance
Section 6
Every six months, a qualified marine technician
should check the following items:
• Check fluid level in the helm reservoir.
• Check outboard engine tilt tubes for salt deposits
or signs of corrosion. Clean and grease as
required.
• Check and grease slider assembly on front of the
engine steering cylinder assemblies.
• Check mechanical linkage and connections.
• Tighten loose parts and replace any worn items.
• Check all self-locking fasteners and locking tabs
for tightness.
• Check system for hydraulic fluid leaks. Refill and
purge system as necessary.
• Check steering hoses for signs of chafing, cuts,
and leaks. Replace any steering hose that shows
signs of damage.
• Inspect the bilge, console interior, and splashwell
for signs of leaking hydraulic fluid.
Approved Steering Fluids
The following fluids are approved for use in this man-
ual hydraulic steering system:
• Sea Star HA-5490
• Texaco H015
• Aero Shell #41
• Esso Univis N15 or J13
• Chevron Aviation fluid A
• Mobil Aero HFA
• Any MIL SPEC H5606C fluid
Dexron II automatic transmission fluid may be used in
an emergency.
!
WARNING
Never use brake fluid in your manual hydraulic
steering system. Brake fluid will damage the
system and can cause loss of steering control.
Summary of Contents for 750 IMPACT
Page 10: ...1 8 Operator Notes...
Page 12: ...1 10 Section 1 Safety Deck Occupancy Chart...
Page 14: ...1 12 Section 1 Safety 1 2 3 5 7 9 A 4 6 8 0 B C E D Warning Label Chart...
Page 16: ...1 14 Operator Notes...
Page 52: ...3 4 Section 3 Fuel Systems Fuel System Diagram 3 4 6 9 2 8 1 5 7 A B 0 C D E...
Page 68: ...3 20 Operator Notes...
Page 70: ...4 2 Section 4 Boat Systems Console Layout 1 2 3 4 7 8 9 0 A B C D E F G H I 1 6 5...
Page 72: ...4 4 Section 4 Boat Systems Deck Layout 1 2 3 4 5 6 7 8 9 0 A B C D E G F H...
Page 104: ...5 10 Operator Notes...
Page 136: ...6 22 Operator Notes...
Page 138: ...7 2 Section 7 Collar Maintenance 1 2 3 4 3 4 6 5 6 5 6 5 5 6 7 7 7...