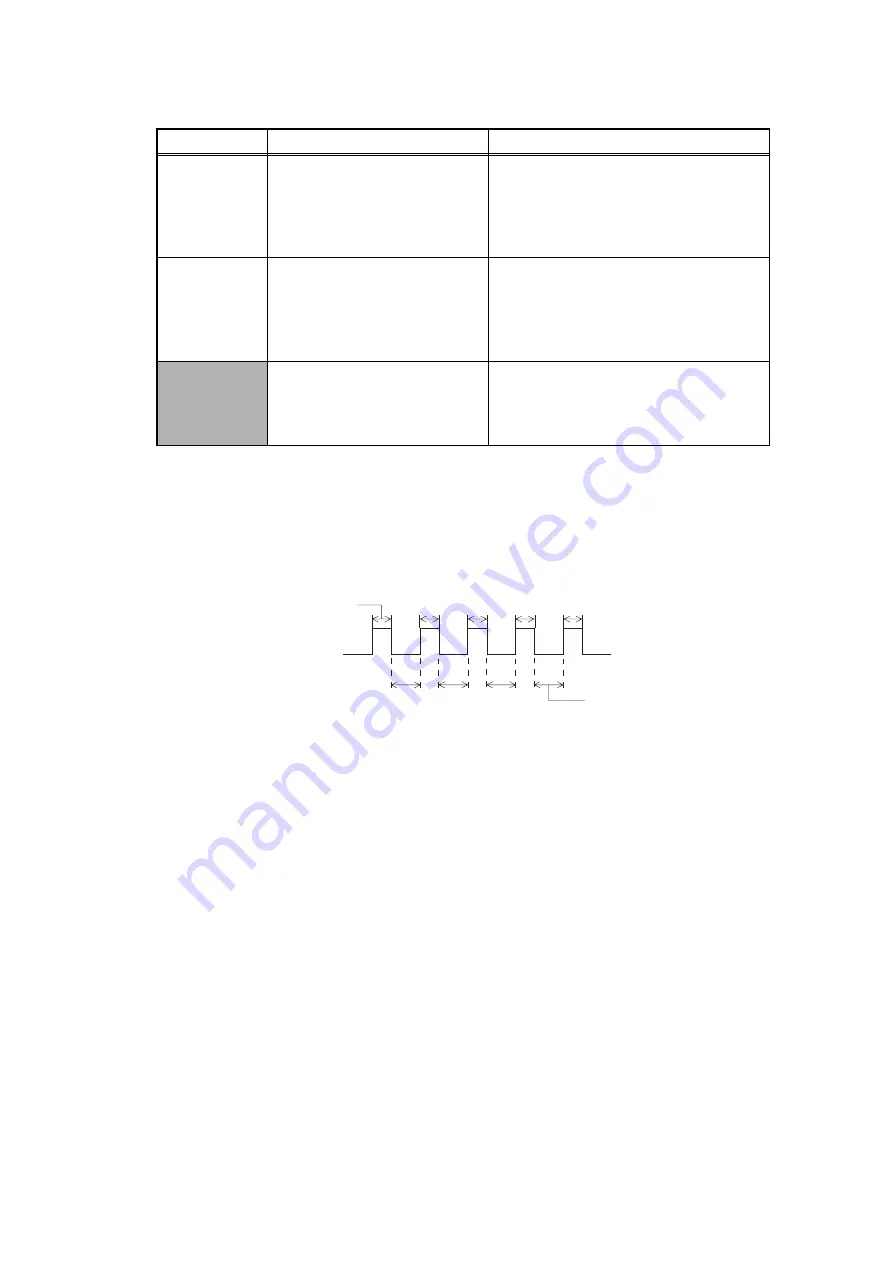
App. 1-5
Confidential
<WSW02>
• Selectors 1 through 4:Tone signal transmission time length and Min. pause in tone
dialing
These selectors set the tone signal transmission time length and minimum pause in tone
dialing.
(Example: If "1," "2," "3," "4," and "5" are dialed.)
• Selectors 5 through 8: Attenuator for pseudo ring backtone to the line
These selectors are used to adjust the sound volume of a ring backtone in the F/T mode,
an on-hold sound, or a beep generated as a signal during remote control operation or at
the start of ICM recording.
The larger the value specified by these selectors, the greater the attenuation.
Selector No.
Function
Setting and Specifications
1
2
Tone signal transmission time
length
No. 1 2
0 0 : 70 ms
0 1 : 80 ms
1 0 : 90 ms
1 1 : 100 ms
3
4
Min. pause in tone dialing
No. 3 4
0 0 : 70 ms
0 1 : 80 ms
1 0 : 90 ms
1 1 : 140 ms
5
I
8
Attenuator for pseudo ring
backtone to the line (selectable
in the range of 0-15 dB, in 1 dB
increments)
0: 0 dB
1: 8 dB
0: 0 dB
1: 4 dB
0: 0 dB
1: 2 dB
0: 0 dB
1: 1 dB
"1"
"2"
"3"
"4"
"5"
Min. pause set by
selectors 3 and 4
Tone signal transmission time
length set by selectors 1 and 2
Summary of Contents for DCP-7030
Page 201: ...5 5 Confidential Print sample Fig 5 1 ...
Page 226: ...5 30 Confidential Location of fans Fig 5 13 Fan motor 60 unit Right side ...
Page 234: ...6 2 Confidential LVPS PCB Circuit Diagram 100V ...
Page 235: ...6 3 Confidential LVPS PCB Circuit Diagram 200V ...
Page 239: ...6 7 Confidential Wiring Diagram ...