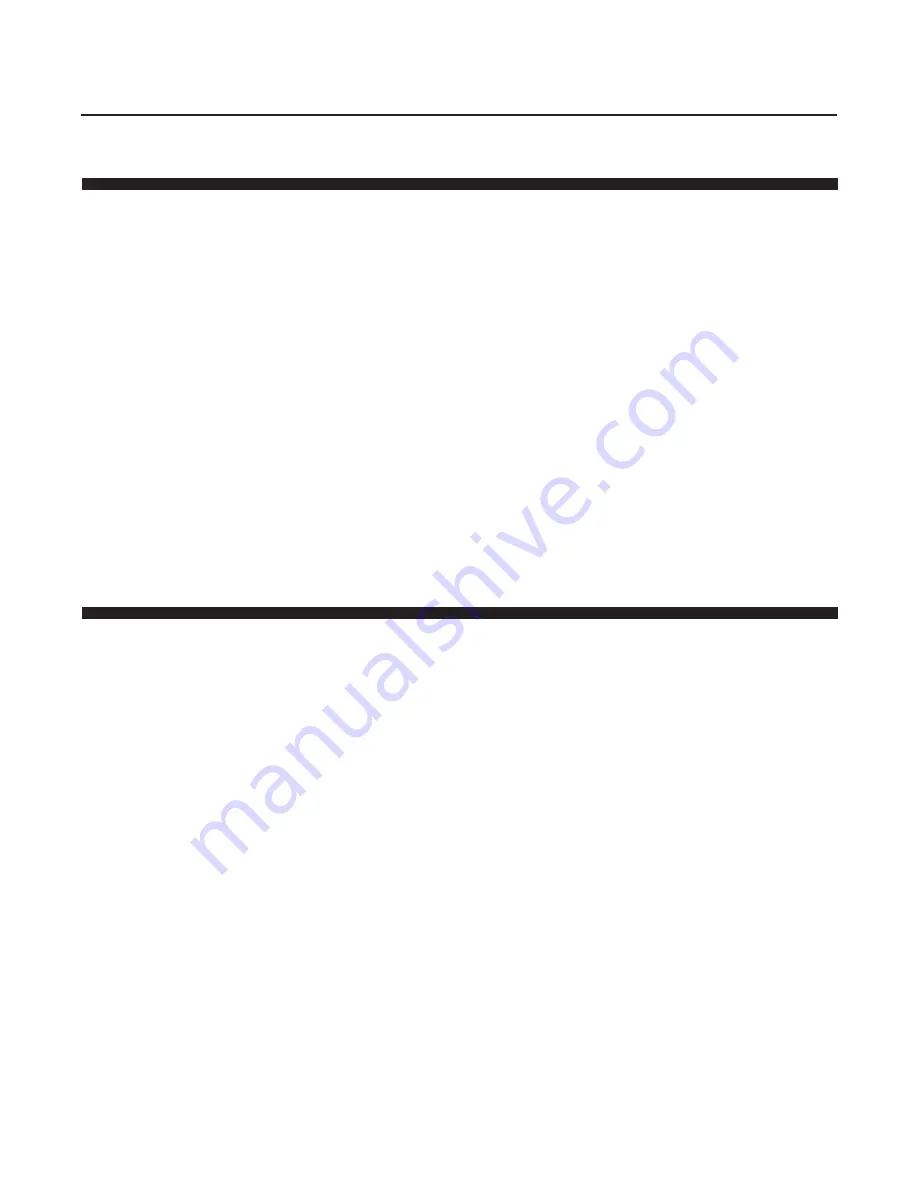
2-10
Brooks
®
Digital MFC's & MFM's
Section 2 Installation
Installation and Operation Manual
X-TMF-SLA5800-Series-RevB-MFC-eng
Part Number: 541B187AAG
January, 2017
2-12
Operation Check Procedure (Digital I/O)
a. Mount the MFC/MFM in its final orientation.
b. Apply power to the MFC/MFM and allow approximately 45 minutes for
the instrument to completely warm up and stabilize its temperature.
c. Turn on the gas supply. A positive flow signal may be present due to
slight valve leak-thru (MFC only).
d. Provide the proper UOM setpoint between 20% and 100% FS to the
MFC via the digital network controller.
e. Check the MFC Flow value. It should match the setpoint UOM. Value
within ± 0.2% FS in less than 10 seconds after setpoint change.
f. If flow output signal does not match the setpoint, and pressure settings
are correct, this could indicate a problem in the MFC. A secondary
issue could be the gas type. When checking with a surrogate gas,
ensure that there is enough pressure to the MFC in order to flow the
correct amount of the surrogate gas.
Example:
Checking an MFC calibrated for 100 ccm SF6 (sulfur hexafluoride).
The sensor factor N2 (nitrogen) is 0.27, therefore the equivalent N2
needed is 100/0.27 = 370.4 ccm. This may require a pressure increase
to make this flow rate.
2-13
Bus/Network (DeviceNet, Profibus, Foundation Fieldbus, EtherCAT)
Other problems that may occur in an operational checkout of a Bus/
Network MFC could be due to data mismatches of Input/Output I/O
assemblies. For proper communication over the Bus/Network network, the
MFC must be set up with the same I/O Assembly as the network master.
The Bus/Network specification defines Input and Output relative to the
network (i.e. the data being PRODUCED from the device (MFC) as an
INPUT into the network or the data is being CONSUMED by the device
(MFC) is an OUTPUT from the network).
NOTE: For additional DeviceNet, Profibus, Foundation Fieldbus and/or
EtherCAT details, please see Brooks Supplemental Instruction Manuals.