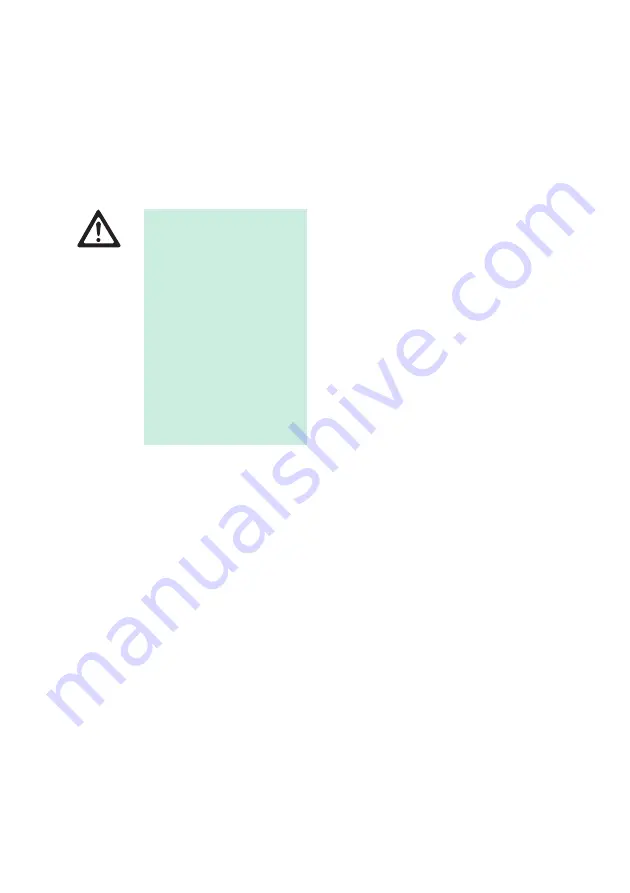
19
Inspection, maintenance and checks
►
Allow the product to cool down to room tempera-
ture.
►
After each complete cleaning, disinfecting and dry-
ing cycle, check that the instrument is dry, clean,
operational, and free of damage (e.g. broken insu-
lation or corroded, loose, bent, broken, cracked,
worn, or fractured components).
►
Dry the product if it is wet or damp.
►
Repeat cleaning and disinfection of products that
still show impurities or contamination.
►
Check that the product functions correctly.
►
Immediately put aside damaged or inoperative
products and send them to Aesculap Technical Ser-
vice, see Technical Service.
►
Assemble separable products, see Trocar assembly.
►
Check for compatibility with associated products.
Packaging
►
Place the product in its holder or on a suitable tray.
Ensure that all cutting edges are protected.
►
Pack trays appropriately for the intended steriliza-
tion process (e.g. in sterile Aesculap containers).
►
Ensure that the packaging provides sufficient pro-
tection against recontamination of the product
during storage.
Steam sterilization
Note
The product may only be sterilized when dismantled.
►
Check to ensure that the sterilizing agent will come
into contact with all external and internal surfaces
(e.g. by opening any valves and faucets).
►
Validated sterilization process
–
Disassemble the instrument
–
Steam sterilization through fractionated vac-
uum process
–
Steam sterilizer according to DIN EN 285 and
validated according to DIN EN ISO 17665
–
Sterilization using fractionated vacuum pro-
cess at 134 °C/holding time 5 min
►
When sterilizing several instruments at the same
time in a steam sterilizer, ensure that the maxi-
mum load capacity of the steam sterilizer specified
by the manufacturer is not exceeded.
CAUTION
Damage (metal seizure/fric-
tion corrosion) to the product
caused by insufficient lubrica-
tion!
►
Prior to function checks,
lubricate moving parts (e.g.
joints, pusher components
and threaded rods) with
maintenance oil suitable
for the respective steriliza-
tion process (e.g. for steam
sterilization: Aesculap
STERILIT® I oil spray JG600
or STERILIT® I drip lubrica-
tor JG598).
Summary of Contents for Aescualp MINOP inVent trocar 30
Page 2: ......
Page 3: ...11 10 1 4 3 2 9 8 7 5 6...
Page 165: ...163 MINOP inVent 30...
Page 167: ...165 5 MINOP inVent 1 2 6 5 3 MINOP inVent 1 2 3 5 3 4 5 6 3 1 5 1 5 1...
Page 168: ...166 Aesculap MINOP inVent 30 5 5 6 7 6 5 1 5 1...
Page 169: ...167 7 3 5 MINOP inVent 1 8 8 5 1 5 3 1...
Page 170: ...168 Aesculap MINOP inVent 30 7 MINOP inVent 1 9 9 3 8 MINOP inVent 1 10 10 7 8 1 8 3 1...
Page 171: ...169 3 5 MINOP inVent 1 11 11 4 12 12 7 1 3 1 4...
Page 173: ...171 15 5 8 6 9 5 8 3 7 12 16 16 1 9 3 8 7...
Page 174: ...172 Aesculap MINOP inVent 30 10 11 17 17 11 2 18 18 11 10 11 2...
Page 175: ...173 10 11 19 MINOP inVent 1 19 4 20 20 11 1 9 4...
Page 176: ...174 Aesculap MINOP inVent 30 Aesculap Extranet www aesculap extra net Aesculap 6 45 C...
Page 177: ...175 VAH FDA CE pH 8 www a k i org Rote Brosch re 6...
Page 178: ...176 Aesculap MINOP inVent 30 H2O2 55 C...
Page 179: ...177 TA013543 20...
Page 180: ...178 Aesculap MINOP inVent 30 FDA CE BBraun Stabimed T C F t I 15 2 pH 9 II 1...
Page 181: ...179 I 35 15 1 5 II...
Page 183: ...181 Aesculap Aesculap STERILIT I lspray JG600 STERILIT I Tropf ler JG598...
Page 185: ...183 FH620R MINOP 30 inVent PE204A 30 MINOP RT068R MINOP inVent...