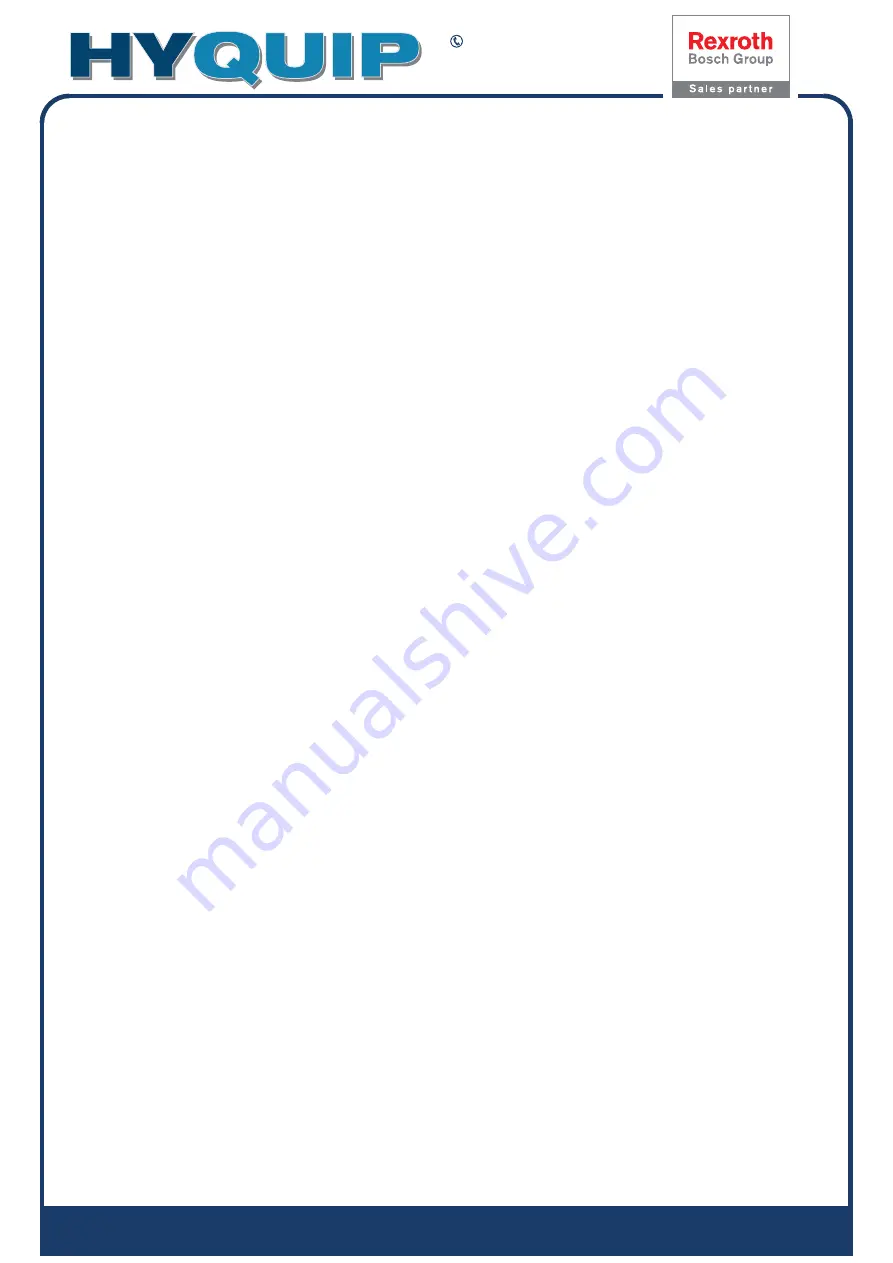
Company Registered in England No: 4167649 VAT Registration No: 732 5692 25 BS EN ISO 9001:2008 No: LRQ 0964389
+44 (0)1204 699 959
Hyquip Limited New Brunswick Street Horwich Bolton Lancashire BL6 7JB UK
www.hyquip.co.uk
/web/index
14/60
About this product
Bosch Rexroth AG
, VT-VPCD, RE 30028-B/09.13
5 About this product
5.1 Performance
description
The closed-loop control electronics VT-VPCD is part of a control system for the
electrohydraulic control of swivel angle and pressure and power limitation of axial
piston pumps of type A4VS... with HS4 control as well as axial piston pumps of type
A2V... with EO4 control, each fitted with a proportional valve and swivel angle and
position transducers for sensing the swivel angle and the valve spool travel. The
control electronics VT-VPCD provides all electrical functions required for the control
types HS4 and EO4. The control electronics VT-VPCD can be configured using the
software BODAC.
5.2 Product
description
The figures given in brackets refer to the block circuit diagrams in Chapter 5.2.2
“Block circuit diagrams“ from page 20 on.
The operating principle of the complete system is explained in data sheet RE 30028.
The digital control electronics VT-VPCD consists of a swivel angle controller, a
pressure controller and a valve controller as well as of a power limiter. The position
of the pump‘s swashplate is sensed by an inductive swivel angle transducer, the
actual pressure value is sensed by a pressure transducer. Both actual values are fed
to the control electronics and linked to each other by software. The actual power
value is formed by the product of actual pressure value and actual swivel angle value.
The controller software ensures with the help of a minimum value comparator that
only the controller is active, which is assigned to the relevant working point.
The control electronics is designed as double-sided printed-circuit board in Euro-
card format 100 x 160 mm. It comprises a switched-mode power supply unit [
1
],
which generates all the internally required voltages.
The central unit is a micro-controller, which controls the entire sequence and
realizes the functions of the controller. Configuration data, command values and
parameters are saved in a non-volatile FLASH.
Four binary-coded digital inputs are used for calling up parameter sets (command
values) from the memory, in which a maximum of 16 sets can be saved. A call-up
activates a command value for the swivel angle, pressure and power limitation as
well as ramp times for swivel angle and pressure.
Further control inputs assume the following functions:
“Command valid“: Enable of the parameter set addressed by the current call-up
(H-active)
“Enable“:
Activation of control (H-active)
Remark:
H-active = High-active Level
L-active = Low-active Level
L/H edge = Low/High edge
The analog command values for swivel angle, pressure and maximum power are
provided via differential inputs AI7, AI5 and AI4 [
3
]. With a positive swivel angle
command value, the pump swivels “to the left” (= direction of flow P -> B). The
digital call-up command values are added to the analog command values, and the
sum of both are fed via the relevant ramp generator to the input of the controller.