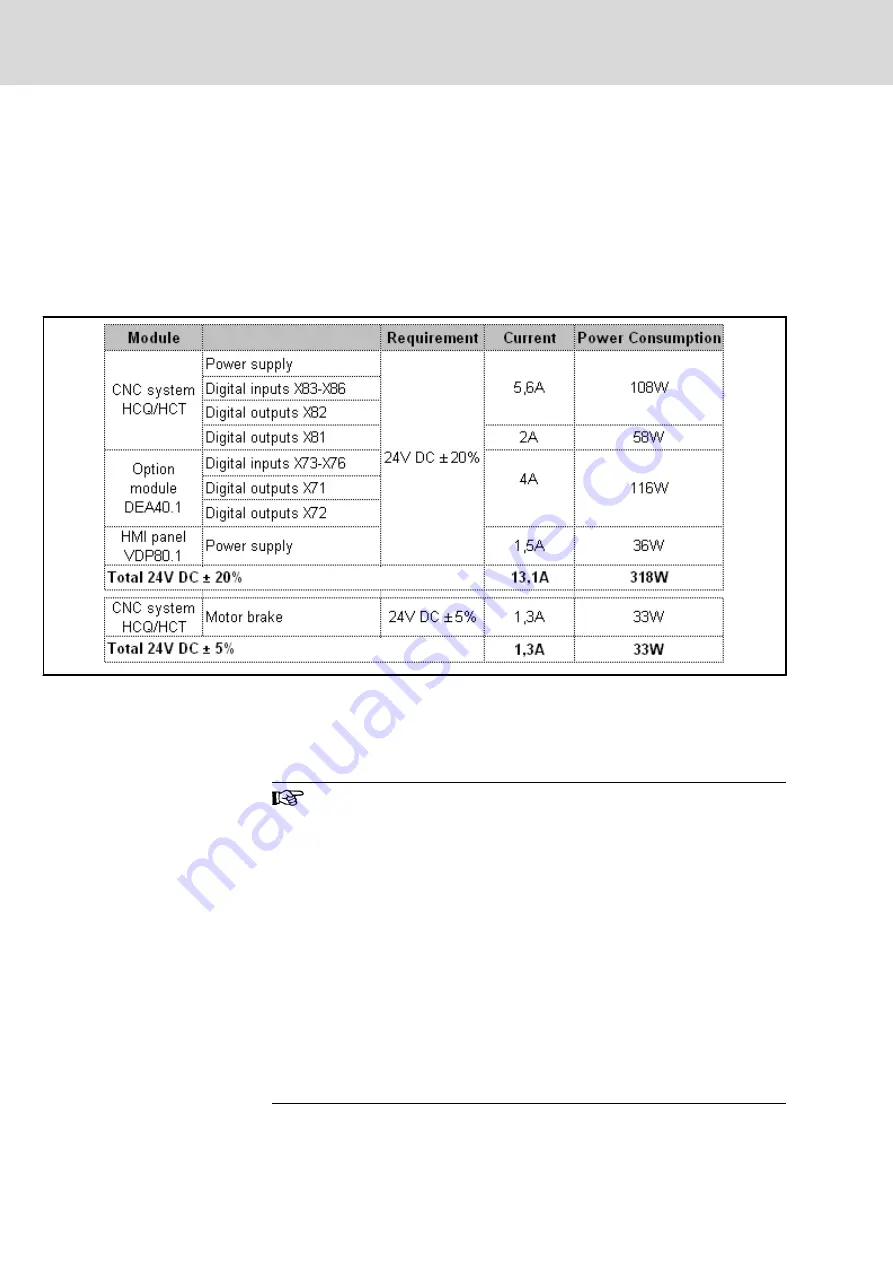
Calculation example
Configure the 24-V voltage supply for the following example MTX micro sys‐
tem:
●
CNC system HCQ02.1 with
–
spindle, 11 kW, without brake
–
2 servo motors, 12 Nm, without brake
–
1 servo motor, 17 Nm, with brake
–
1 optional module DEA40.1
●
HMI control panel VDP80.1
Fig. 5-20:
Calculating the power consumption of an example system
According to the calculation, approx. 320 W are required for 24 V DC ± 20%,
and approx. 35 W are required for 24 V DC ± 5%. If less than the maximum
possible 2 A is used for each of the outputs X81, X71 and X72, the power
consumption can be reduced accordingly.
●
Use an AC-adaptor or a PELV-protected control transformer
according to IEC 60204-1 (Section 6.4) for the 24-V control
voltage supply
●
Overvoltages exceeding 33 V must be discharged by means
of measures in the electrical equipment of the machine or
plant. Such measures include AC-adaptors and overvoltage
limiters which are provided at the input of the control cabinet
and limit incoming overvoltages. This also applies to longer
24-V lines which are placed in parallel to power and line sup‐
ply cables and are able to receive overvoltages through in‐
ductive or capacitive coupling.
●
Please be absolutely sure to observe the instructions on
grounding of the 24-V control voltage supply described in
chapter "Grounding concept" on page 47
●
A current of 0.5 A can be delivered at each digital output.
However, the sum total of all currents may not exceed 2 A
per terminal (BYTE)
Bosch Rexroth AG
DOK-MTXMIC-EASY*******-CO06-EN-P
50/177
IndraMotion MTX micro Easy Setup for Standard Turning and Milling Machines
Selecting and connecting the hardware