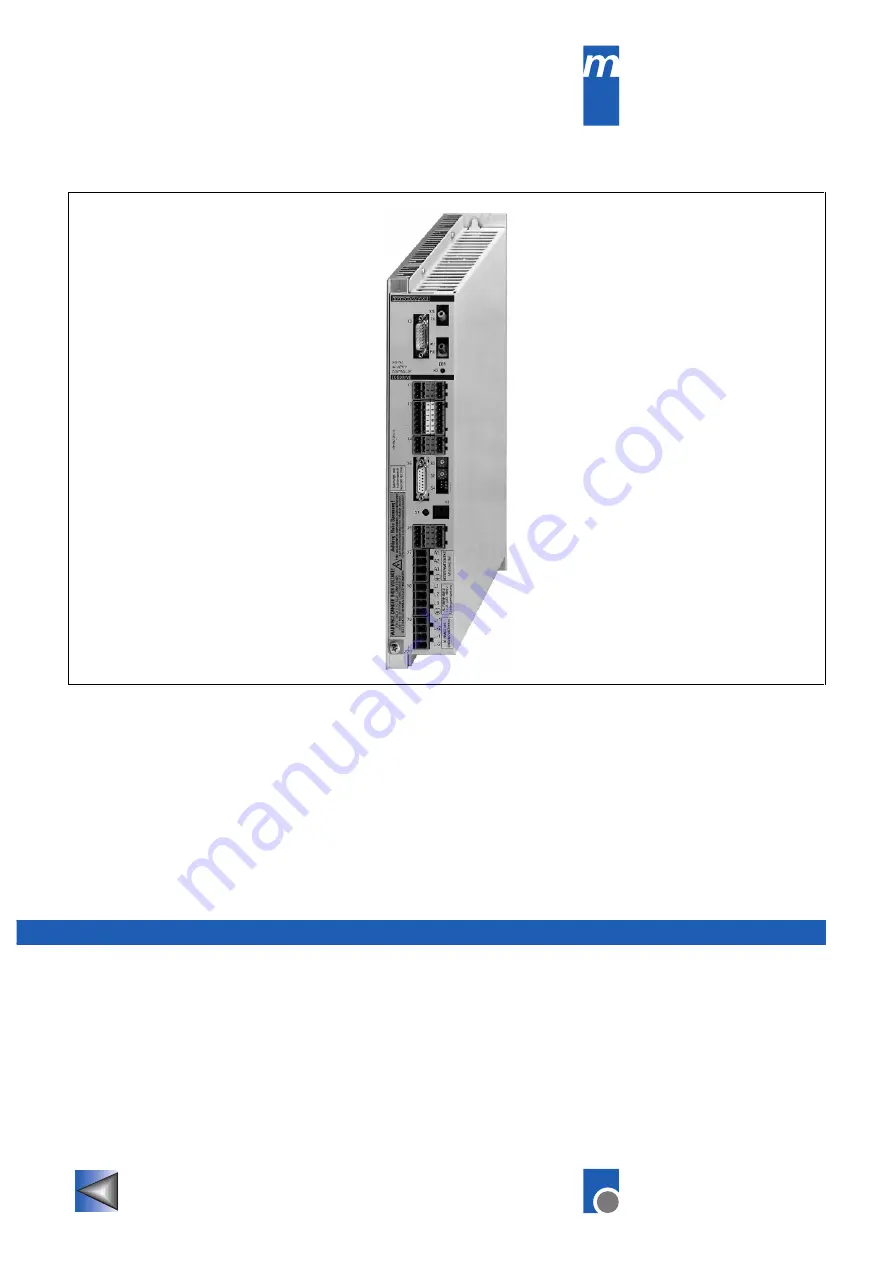
ECODRIVE
DKC02.1 Drive Controller
DOK-ECODRV-DKC02.1****-PRJ2-EN-P
Project Planning Manual
mannesmann
Rexroth
engineering
Indramat
267473
LSA Control S.L. www.lsa-control.com [email protected] (+34) 960 62 43 01
ECODRIVE
DKC02.1 Drive Controller
DOK-ECODRV-DKC02.1****-PRJ2-EN-P
Project Planning Manual
mannesmann
Rexroth
engineering
Indramat
267473
LSA Control S.L. www.lsa-control.com [email protected] (+34) 960 62 43 01