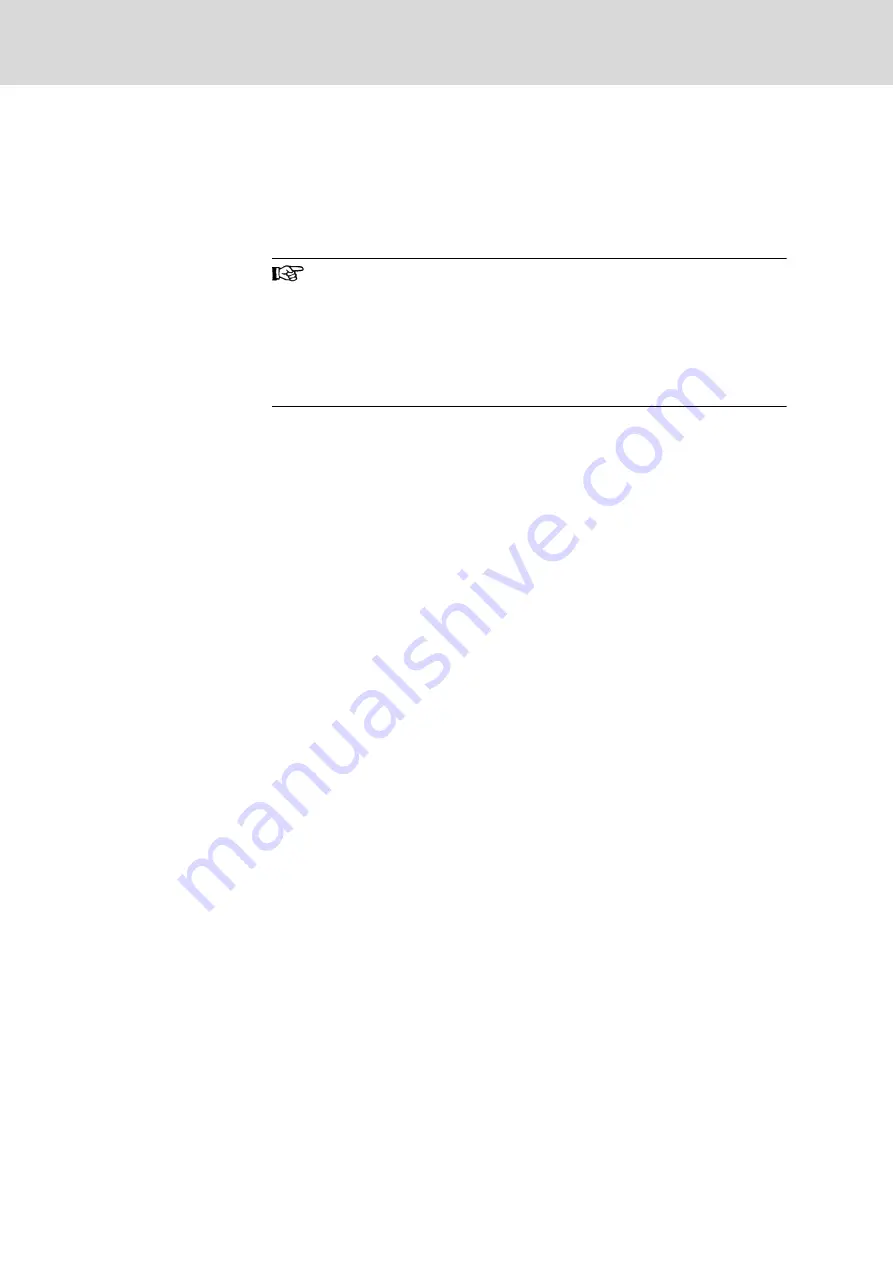
●
In drive systems with regenerative supply units, via a separate single-
phase (NFE type) or three-phase filter (HNF type) near the mains con‐
nection of the control cabinet
●
In drive systems with only infeeding supply units, via the available three-
phase filter of the drive system
When switching power off, make sure the blower is not switched off.
Loads at Mains Filter of Drive Sys‐
tem
Only operate allowed loads at the mains filter of the drive system!
At the three-phase filter for the power connection of regenerative
supply units, it is only allowed to operate the following loads:
●
HMV supply unit with mains choke and, if necessary, mains
contactor
Do not operate any motor blowers, power supply units etc. at the
mains filter of the drive system.
Shielding Mains Supply Lines in
Control Cabinet
If there is a high degree of interference injection to the mains supply line within
the control cabinet, although you have observed the above instructions (to be
found out by EMC measurement according to standard), proceed as follows:
●
Only use shielded lines in area A
●
Connect shields to the mounting plate at the beginning and the end of the
line by means of clips
The same procedure may be required for long cables of more than 2 m between
the point of power supply connection of the control cabinet and the filter within
the control cabinet.
Mains Filters for AC Drives
Ideally, mount the mains filter on the parting line between area A and B. Make
sure the ground connection between filter housing and housing of the drive
controllers has good electrically conductive properties.
If single-phase loads are connected on the load side of the filter, their current
may be a maximum of 10% of the three-phase operating current. A highly im‐
balanced load of the filter would deteriorate its interference suppression ca‐
pacity.
If the mains voltage is more than 480 V, connect the filter to the output side of
the transformer and not to the supply side of the transformer.
Grounding
In the case of bad ground connections in the installation, the distance between
the lines to the grounding points E1, E2 in area A and the other grounding points
of the drive system should be at least d4 = 400 mm, in order to minimize inter‐
ference injection from ground and ground cables to the power input lines.
See also
6.2.2 Division Into Areas (Zones), page 46
Point of Connection for Equipment
Grounding Conductor at Machine,
Installation, Control Cabinet
The equipment grounding conductor of the power cable of the machine, instal‐
lation or control cabinet has to be permanently connected at point PE and have
a cross section of at least 10 mm
2
or to be complemented by a second equip‐
ment grounding conductor via separate terminal connectors (according to EN
61800-5-1:2007, section 4.3.5.5.2). If the cross section of the outer conductor
is bigger, the cross section of the equipment grounding conductor must be ac‐
cordingly bigger.
6.2.5
Design and Installation in Area B - Interference-Susceptible Area of
Control Cabinet
Arranging Components and Lines
Modules, components and lines in area B should be placed at a distance of at
least d1 = 200 mm from modules and lines in area A.
Bosch Rexroth AG
DOK-INDRV*-HMS02*UL***-IB03-EN-P
Rexroth IndraDrive Drive Controllers Power Sections HMS02
52/67
EMC Measures for Design and Installation