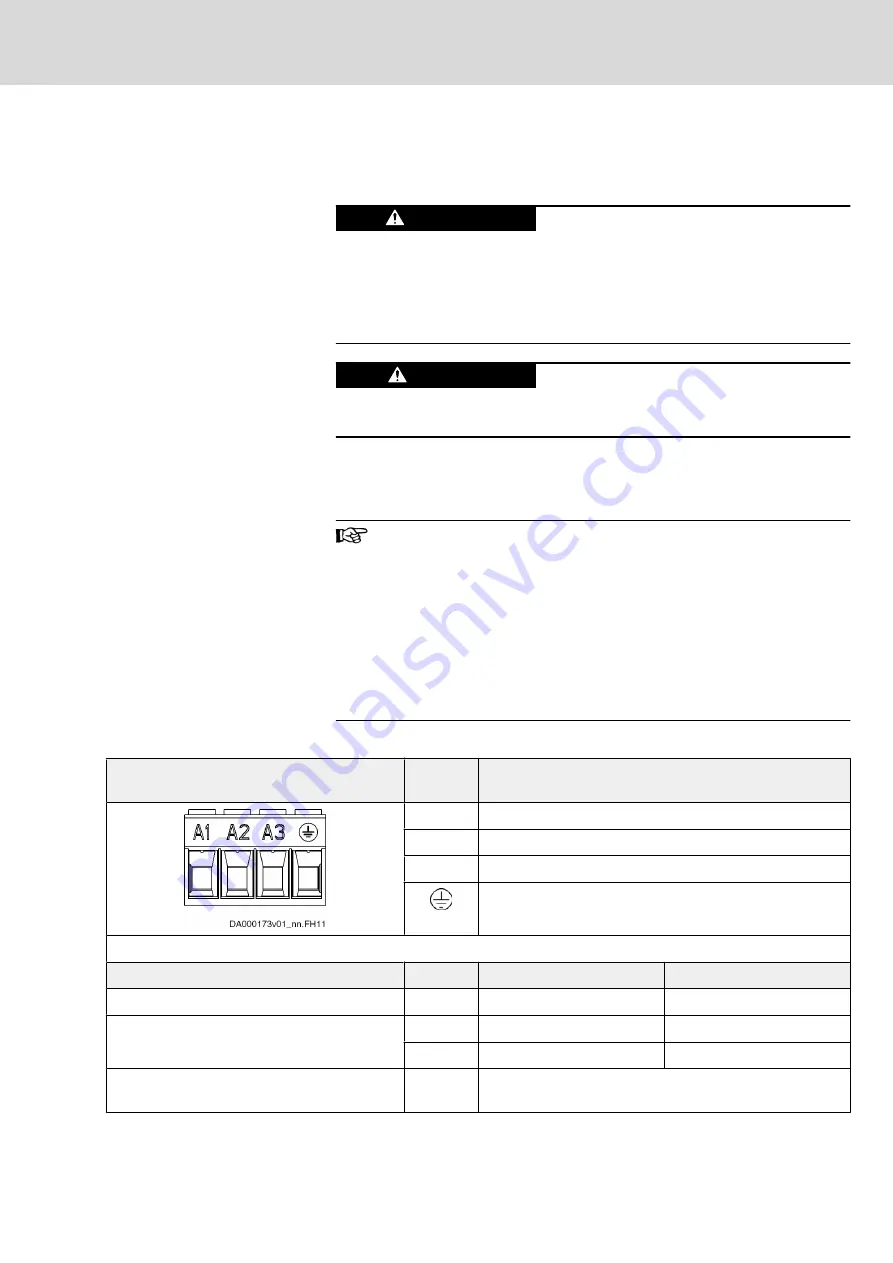
5.2.3
X5, Motor Connection
Important Notes
Lethal electric shock by live parts with more
than 50 V!
WARNING
Exclusively operate the device
●
with plugged on connectors (even if there haven't been any lines connec‐
ted to the connectors) and
●
with connected equipment grounding conductor!
Damage to the device!
CAUTION
Provide strain relief for the terminal connectors of the device in the control cab‐
inet or use the optionally available connection accessory HAS02.
Notes on Installation
The indicated connection cross sections are the cross sections which can be
connected. Dimension the required cross section of the connecting lines ac‐
cording to the occurring current load.
●
For optimum shield contact of the motor power cable, use our
accessory HAS02, where possible.
●
For the connection between drive controller and motor use our
ready-made motor power cables, where possible (see docu‐
mentation "Rexroth Connection Cables").
●
When using NFD03.1 mains filters, the maximum allowed con‐
ductor cross section is limited to 4 mm
2
.
●
For selecting the motor cables, observe the information con‐
tained in the Project Planning Manual "Rexroth IndraDrive
Drive System" → "Connection Cables to Motor".
HMS02.1N-W0028
View
Identifica‐
tion
Function
A1
For power connection U1 at motor
A2
For power connection V1 at motor
A3
For power connection W1 at motor
For equipment grounding conductor of motor
Screw connection at connector
Unit
Min.
Max.
Tightening torque
Nm
0,5
0,6
Connection cable
Stranded wire
mm
2
1,5
4
AWG
16
10
Ooccurring current load and minimum required
connection cross section
A
See Technical Data of device used (I
out
)
DOK-INDRV*-HMS02*UL***-IB03-EN-P
Rexroth IndraDrive Drive Controllers Power Sections HMS02
Bosch Rexroth AG
29/67
Instructions for Use