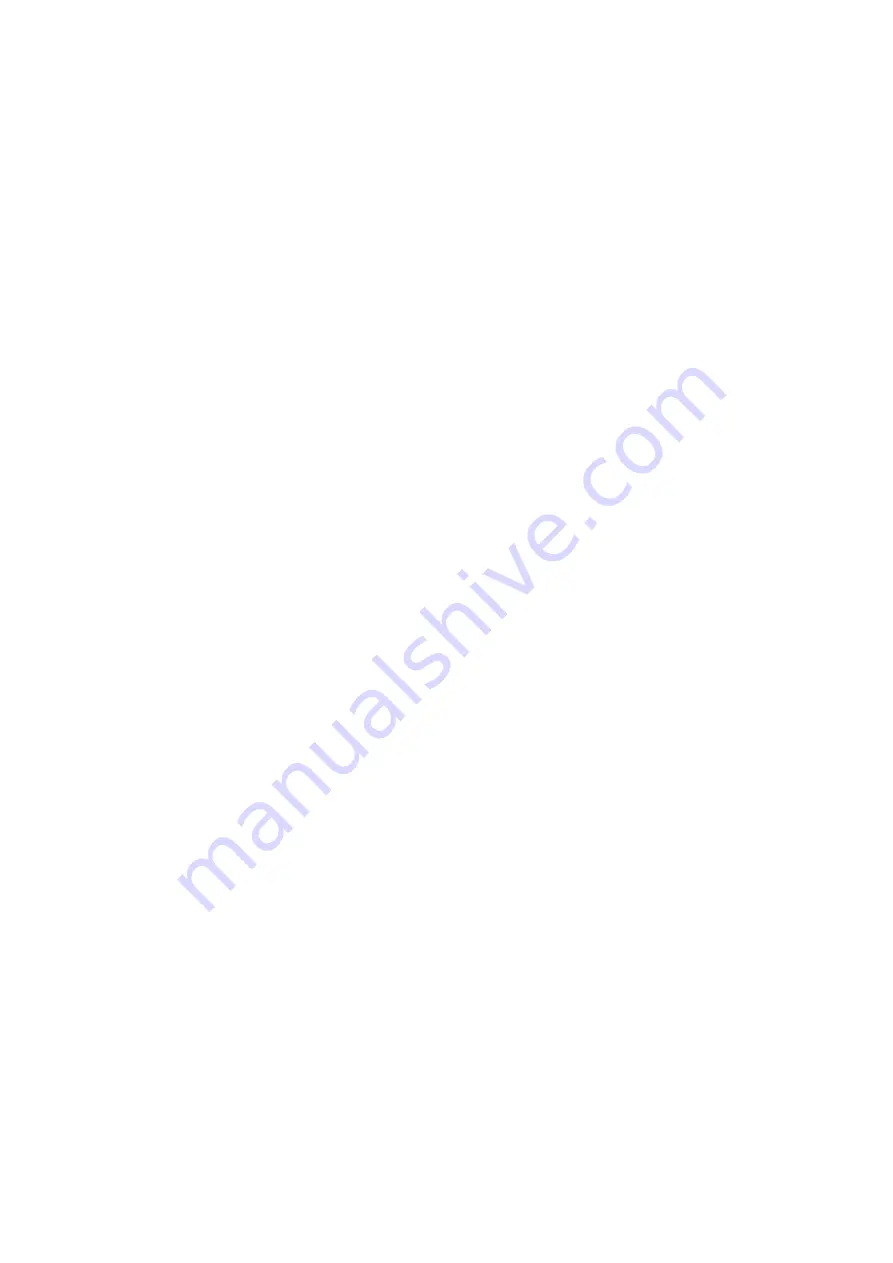
RE 63124-B, Edition: 08.2021, Bosch Rexroth AG
Contents |
Press modules Type IH04 3/56
Contents
About this documentation ........................................................................ 5
1.1 Validity of the documentation ...................................................................... 5
1.2 Required and additional documentation ...................................................... 5
1.3 Representation of information ..................................................................... 6
1.3.1 Safety instructions ....................................................................................... 6
1.3.2 Symbols ....................................................................................................... 7
1.3.3 Abbreviations ............................................................................................... 7
2.1 About this chapter ....................................................................................... 8
2.2 Intended use ............................................................................................... 8
2.3 Improper use ............................................................................................... 9
2.4 Qualification of personnel ......................................................................... 10
2.5 General safety instructions ........................................................................ 10
2.5.1 General safety instructions for press modules .......................................... 11
2.6 Product- and technology-dependent safety instructions ............................ 12
2.7 Personal protective equipment .................................................................. 15
2.8 Information of the machine manufacturer .................................................. 15
2.9 Obligations of the machine end-user ......................................................... 15
General information on damage to property and damage to product ...... 16
6.1 Transporting the press module .................................................................. 20
6.1.1 Use of attachment points .......................................................................... 21
6.1.2 Transport using forklifts and similar floor conveyors ................................. 22
6.1.3 Transport using cranes and similar lifting gear .......................................... 22
6.2 Storing the press module .......................................................................... 23
7.1 Unpacking .................................................................................................. 24
7.2 Installation conditions ............................................................................... 24
7.3 Assembling the press module .................................................................... 25
7.3.1 Installing the press module ....................................................................... 25
7.3.2 Hydraulically connecting the press module ............................................... 26
7.3.3 Electrically connecting the press module .................................................. 29