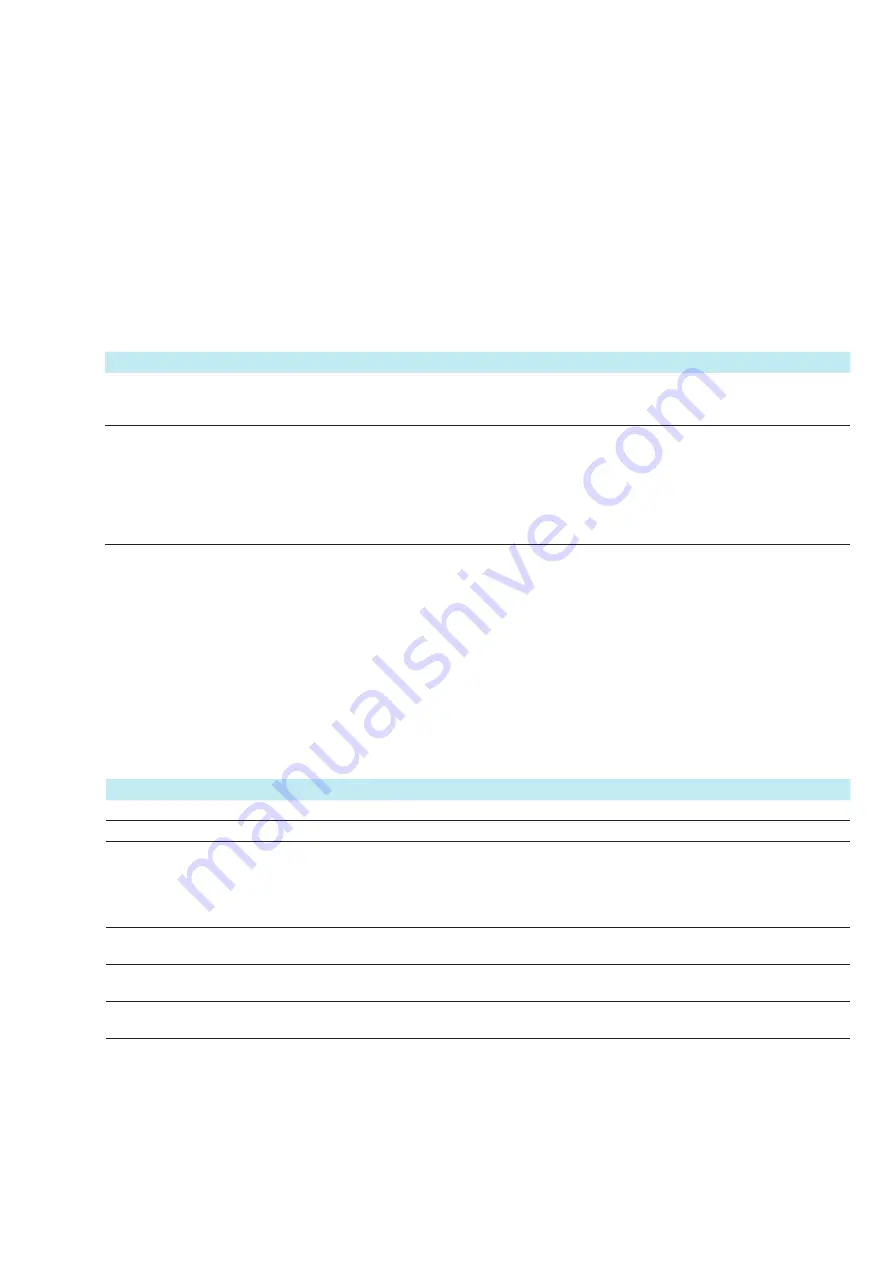
RE 63124-B, Edition: 08.2021, Bosch Rexroth AG
Maintenance and repair |
Press modules Type IH04 35/56
10.2 Inspection
The inspection on the press module can only be made in connection with the
machine/system.
▶ Document mandatory or unscheduled inspection work in a meaningful way and
retain it for verification purposes.
▶ For the scope and time intervals of inspection of the overall machine/system,
please refer to the operating instructions of the machine manufacturer.
The following inspection work is required for the press module:
Table 7: Inspection of the "press module"
Inspection activity
Implementation
Inspection interval
Pressure measurement with suitable pressure
gauge with suitable measurement range and with
hose and connection coupling
▶ Check the required pressure.
Regularly
Visual inspection
▶ Check all components for tight seat,
damage/corrosion, leakage (oil drop formation).
▶ Check the seals on the attached and mounted valves
1)
.
▶ Check for oil runs at connection surfaces of the
valves, flanges or fittings.
▶ Check whether all warning and information signs
are present.
Regularly
1)
The seals of attached and mounted valves are subject to a natural process of wear and
aging. Bosch Rexroth recommends replacement at appropriate time intervals. The intervals
are mainly determined by the operating conditions such as temperature and the cleanliness
of the hydraulic fluid.
10.3 Maintenance schedule
The following maintenance work is required for the press module and must be
included in the maintenance schedule of the machine manufacturer/end-user.
Table 8: Maintenance schedule for the "press module"
Maintenance activity
Implementation
Maintenance interval
Hydraulic system
Control of the hydraulic fluid
▶ Check the hydraulic fluid level in the tank.
Electric monitoring
Hydraulic fluid samples or
analyses
▶ Take a hydraulic fluid sample.
▶ Observe the safety data sheet of the hydraulic fluid.
▶ Document the product name including batch number.
• After flushing
• 50 operating hours after flushing
• 4 weeks after flushing
• 12 weeks after flushing
• Every six months
Change of hydraulic fluid
▶ Change the hydraulic fluid using a filter (5 µm).
According to manufacturer's
specifications
Temperature control
▶ Check the operating temperature
(comparable load condition).
Electric monitoring
Visual inspection
▶ Check all components for safe seat, damage, wear, leakage,
existence of all warning and information signs.
At least once annually