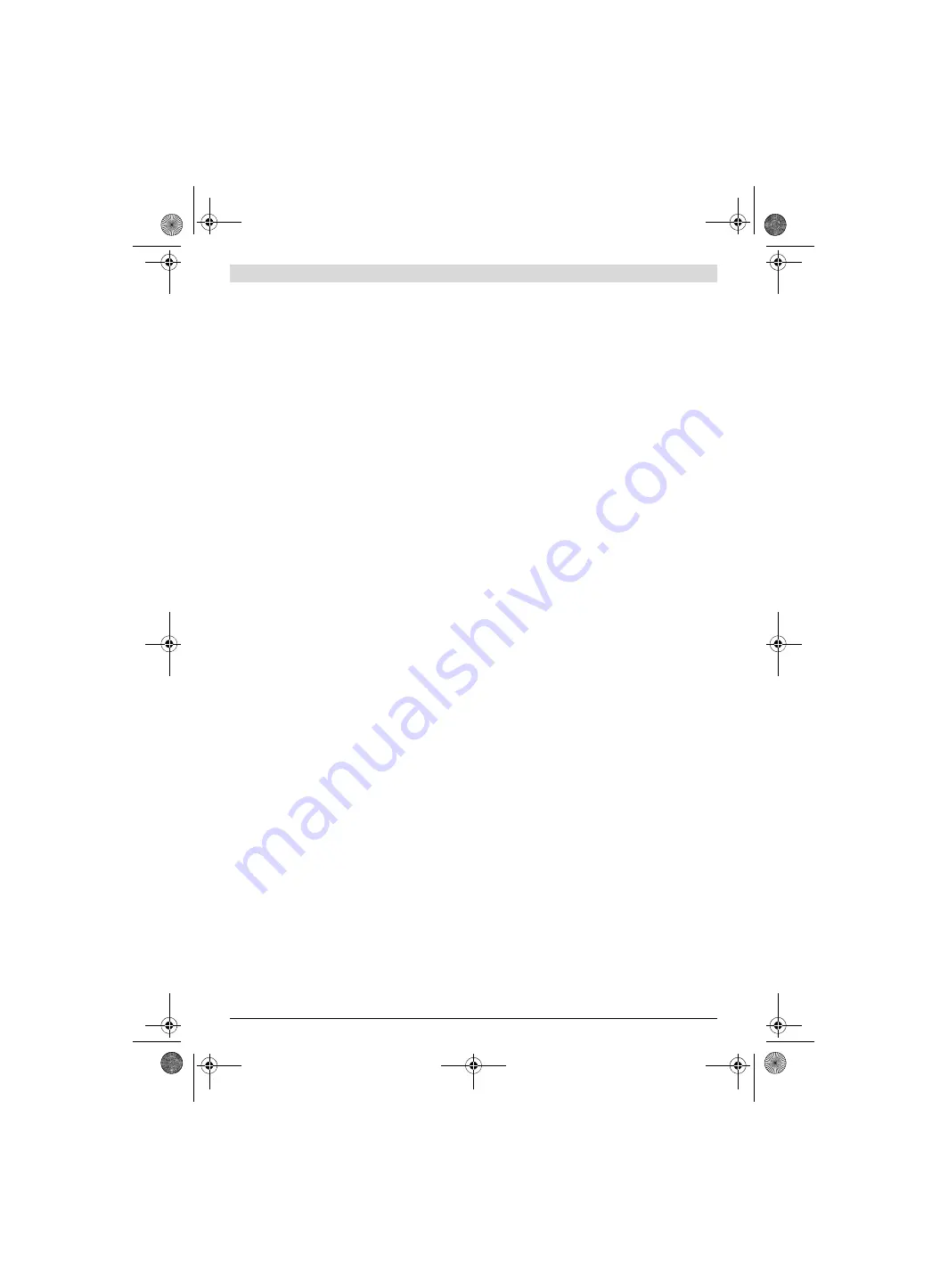
English |
17
Bosch Power Tools
1 609 92A 37V | (21.9.16)
– Turn the wing bolt for adjustment of the auxiliary handle in
anticlockwise direction and set the auxiliary handle
9
to
the required position. Then tighten the wing bolt again in
clockwise direction.
Clamping Fixture
0 607 460 401/... 400
– The pneumatic tool can be mounted in a clamping fixture
over the mentioned clamping area
8
. If possible, utilise the
entire clamping area. The smaller the clamping area, the
stronger the clamping forces act.
Exhaust-air Guidance
With exhaust-air guidance, the exhaust air can be diverted
through an exhaust-air hose away from your workplace, while
at the same time achieving optimal sound-proofing. Addition-
ally, your working conditions are improved, as your workplace
can no longer be contaminated though oil-containing air and
dispersed dust or chips.
Centralised Exhaust-air Guidance (see figure A)
0 607 460 001
– Loosen hose clamp
14
of supply-air hose
13
, mount the
supply-air hose to hose fitting
5
and retighten the hose
clamp.
– Work the exhaust-air hose (centralised)
15
, which con-
ducts the exhaust air away from your workplace, over the
supply-air hose
13
. Then connect the pneumatic tool to
the air supply (see “Connecting the Air Supply”, page 17)
and work the exhaust-air hose (centralised)
15
over the
mounted supply-air hose onto the end of the pneumatic
tool.
Connecting the Air Supply (see figure B)
Ensure that the air pressure is not lower than 6.3 bar
(91 psi) because the pneumatic tool is designed for
this operating pressure.
For maximum performance, the values for the inner hose di-
ameter as well as the connection threads must be adhered to
as listed in the “Technical Data” Table. To maintain the full
performance, only use hoses with a maximum length of 4 m.
The compressed air supplied should be free of foreign materi-
al and moisture to protect the tool from damage, contamina-
tion, and the formation of rust.
Note:
The use of a compressed-air maintenance unit is neces-
sary. This ensures proper function of the pneumatic tools.
Observe the operating instructions of the maintenance unit.
All fittings, connecting lines and hoses must be dimensioned
for the pressure and the required air volume.
Avoid restrictions in the air supply, e.g., from pinching, kink-
ing, or stretching!
When in doubt, check the pressure at the air inlet with a pres-
sure gauge with the pneumatic tool switched on.
Connecting the Air Supply to the Pneumatic Tool
– Screw hose fitting
5
into the connection socket at air inlet
6
.
To avoid damage to interior valve components of the pneu-
matic tool when screwing hose fitting
5
in or out, it is rec-
ommended to counter-hold the projecting connection
socket of air intake
6
with an open-end wrench (size
22 mm).
– Loosen hose clamp
14
of supply-air hose
13
, mount the
supply-air hose to hose fitting
5
and retighten the hose
clamp.
Note:
Always mount the supply-air hose to the pneumatic tool
first, then to the maintenance unit.
Changing the Tool (see figure C)
– Place the insertion tool into the tool holder
1
until you feel
it engage.
Operation
Starting Operation
The pneumatic tool works optimally at a working pressure of
6.3 bar (91 psi), measured at the air inlet when the pneumat-
ic tool is switched on.
Reversing the rotational direction
0 607 460 001
(see figure D)
–
Right rotation:
The rotational direction switch
3
is not
pressed.
–
Left rotation:
Press the rotational direction switch
3
.
Turn the rotational direction switch
3
to lock its position.
0 607 460 400/... 401
(see figure E)
–
Right rotation:
Push the rotational direction switch
3
rightward to the stop.
–
Left rotation:
Push the rotational direction switch
3
left-
ward to the stop.
Setting the Torque (see figure F)
0 607 460 001/ ... 401
For high torque settings, appropriately high counter-
force is required.
– Turn the torque sleeve
2
until the desired torque is set.
The torque sleeve
2
engages every quarter turn.
Turning in the clockwise direction results in a higher torque, in
the counterclockwise direction, a lower torque.
Start with low setting values.
Note:
For soft screwdriving applications, the safety clutch
does not disengage for low torque settings.
After Setting the Torque
– Adapt the torque to the respective screwdriving applica-
tion (hard, medium, soft) through practical testing.
– Check the torque with an electronic torque measuring de-
vice or a torque wrench.
OBJ_BUCH-2098-002.book Page 17 Wednesday, September 21, 2016 9:50 AM