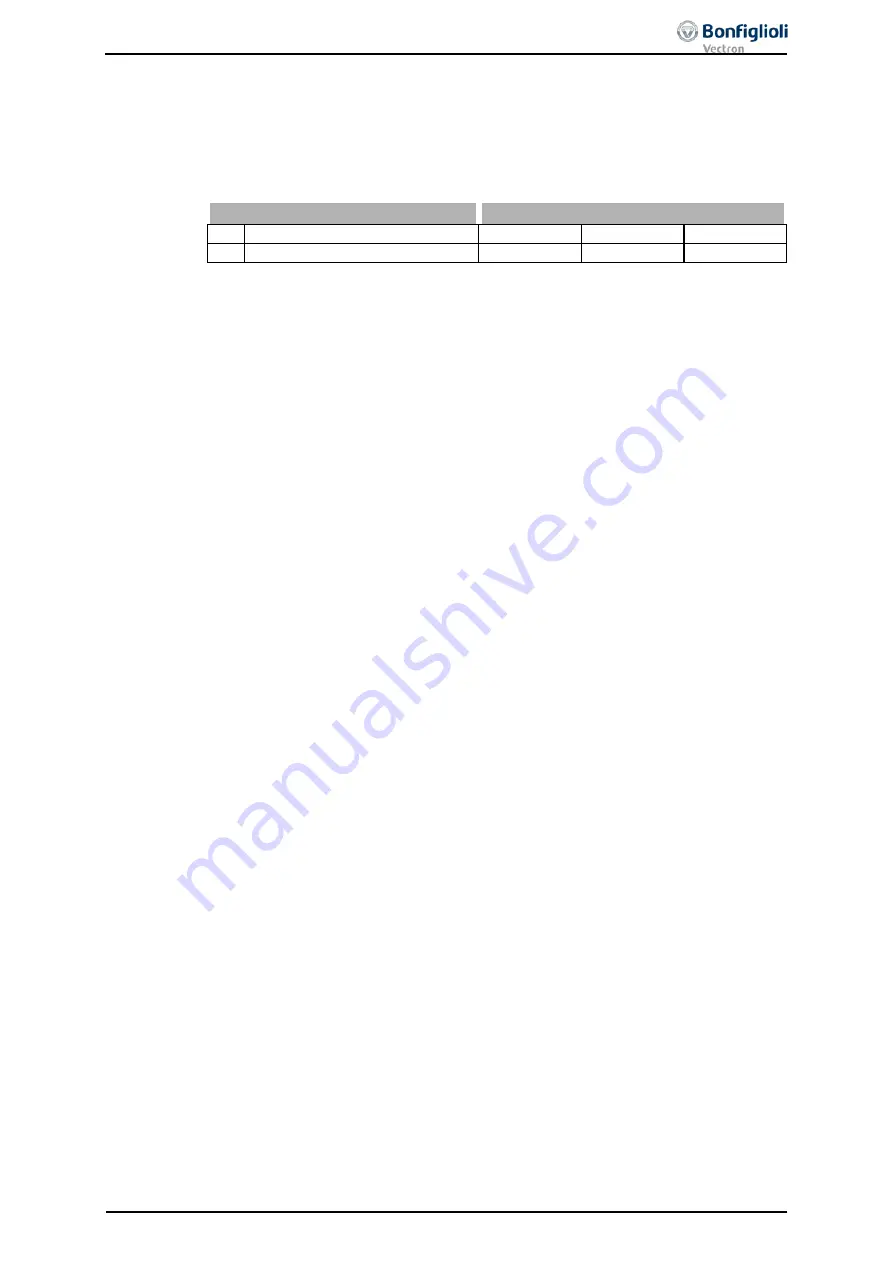
9.5
Control Level
The
Control level
28 defines the scope of the functions to be parameterized. The op-
erating instructions describe the parameters on the third control level. These parame-
ters should only be set by qualified users.
Parameter
Settings
No.
Description
Min.
Max.
Fact. sett.
28 Control level
1
3
1
9.6
User Name
The
User name
29 can be entered via the optional control software VPlus. The plant
or machine designation cannot be displayed completely via the control unit.
32 alphanumeric characters
9.7
Configuration
The
Configuration
30 determines the assignment and basic function of the control
inputs and outputs as well as the software functions. The software of the frequency
inverters offers various configuration options. These differ with respect to the way in
which the drive is controlled. Analog and digital inputs can be combined and com-
plemented by optional communication protocols. The operating instructions describe
the following configurations and the relevant parameters in the third
Control level
28
(adjustment of parameter
Control level
28 to value 3).
Configuration 110, sensorless control
Configuration 110 contains the functions for variable-speed control of a 3-phase ma-
chine in a wide range of standard applications. The motor speed is set according to
the V/f characteristic in accordance with the voltage/frequency ratio.
Configuration 111, sensorless control with technology controller
Configuration 111 extends the functionality of the sensorless control by software
functions for easier adaptation to the customer's requirements in different applica-
tions. Depending on the application, the technology controller may be used, which
enables the control of flow rate, pressure, contents level or speed.
Configuration 410, sensorless field-oriented control
Configuration 410 contains the functions for sensorless, field-oriented control of a
3-phase machine. The current motor speed is determined from the present currents
and voltages in combination with the machine parameters. In this configuration, par-
allel connection of several 3-phase motors is possible to a limited extent only.
Configuration 411, sensorless field-oriented control
with technology controller
Configuration 411 extends the functionality of Configuration 410 by a Technology
Controller, which enables a control based on parameters such as flow rate, pressure,
contents level or speed.
Configuration 430, sensorless field-oriented control
with speed/torque control
Configuration 430 extends the functionality of Configuration 410 by functions for
torque-dependent, field-oriented control. The reference torque is represented as a
percentage and it is transmitted into the corresponding operational performance of
the application. Change-over between variable-speed control and torque-dependent
control is done jerk-free during operation.
06/13
Operating Instructions ACU
119
Summary of Contents for ACTIVE Cube ACU 201-01
Page 1: ...ACTIVE CUBE Operating Instructions Frequency inverter 230 V 400 V 0 25 kW 132 kW...
Page 2: ......
Page 291: ......