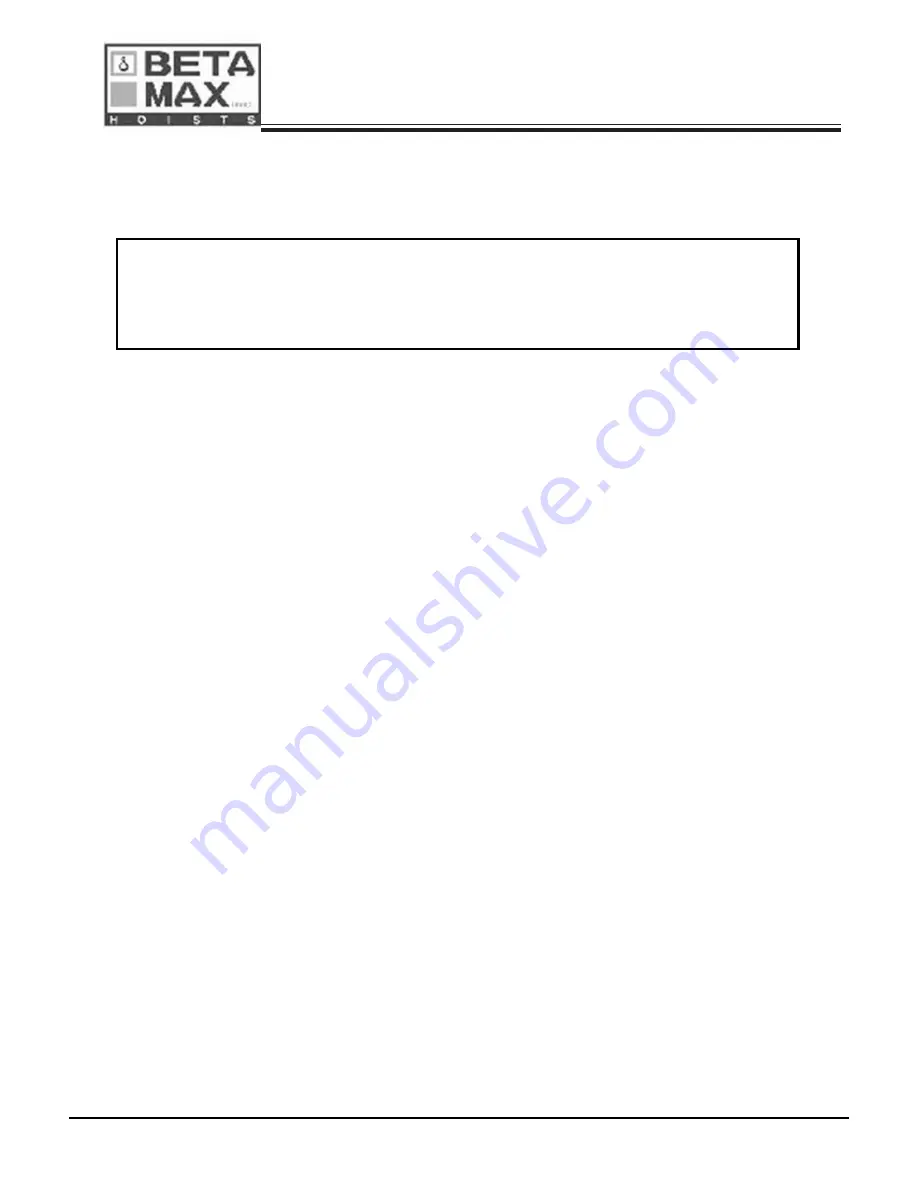
Use and Maintenance Instruction Manual
MAXIAL TRACK HOIST
REV. 2.2 (2017)
MAINTENANCE AND REPAIR
Page | 10-8
10.3.4 Wire rope cable
Ensure the wire rope cable is not bent, kinked, corroded, knotted, or damaged in any way. If
the wire rope shows any of these conditions, immediately replace the wire rope.
10.3.4.1
R
emoving the wire rope cable
1. Remove the wire rope guard
2. Connect the hoist to the correct power source
3. Press the DOWN button on the handheld control pendant to be gin to spool
out the wire rope from the drum. During the unspooling process maintain a pulling
force on the cable so that the cable does not build up in the drum housing.
Continue unspooling the cable until the end that is attached to the drum is
reached.
4. Align the hole in the side of the drum housing with the two bolt heads located
through the hole on the drum.
5. Disconnect the power source for safety
6. Release the wedge plate clamping the rope to the drum by loosening the two
bolts through the side of the drum. Do not remove bolts.
7. Remove the wire rope cable.
8. Reinstall the wire rope guard
10.3.4.2
Installing wire rope cable
1. Remove the wire rope guard
2. Connect the hoist to the correct power source
3. Align the hole in the side of the drum housing with the two bolt heads located
through the hole on the drum housing.
4. Disconnect the power source for safety
5. Release the wedge plate clamping the rope to the drum by loosening the two
bolts through the side of the drum. Do not remove bolts.
6. Insert the new wire rope through the top of hoist and into the space between the
wedge plate and drum
7. Apply pressure with the wedge plate on the wire rope by tightening the two bolts
through the side of the drum. Tighten the bolts evenly.
8. Connect the hoist to the correct power source
9. Press the UP button on the handheld control pendant to b e gin spooling the
wire rope onto the drum. During the spooling process maintain a pulling force on
the cable so that the cable creates tight wraps onto the drum.
10. Reinstall the wire rope guard.
DANGER
Always wear heavy gloves when handling the wire rope cable to prevent
possible hand injury.
Summary of Contents for MAXIAL TRACK HOIST
Page 2: ......
Page 117: ......
Page 118: ......
Page 121: ......
Page 122: ......
Page 123: ......
Page 124: ......
Page 127: ......
Page 128: ......
Page 129: ......
Page 130: ......
Page 131: ......
Page 132: ......
Page 133: ......
Page 134: ......
Page 137: ......
Page 138: ......
Page 139: ......
Page 140: ......
Page 141: ......
Page 142: ......
Page 143: ......
Page 144: ......
Page 145: ......
Page 146: ......
Page 149: ......
Page 150: ......
Page 153: ......
Page 154: ......
Page 157: ......
Page 158: ......
Page 159: ......
Page 160: ......