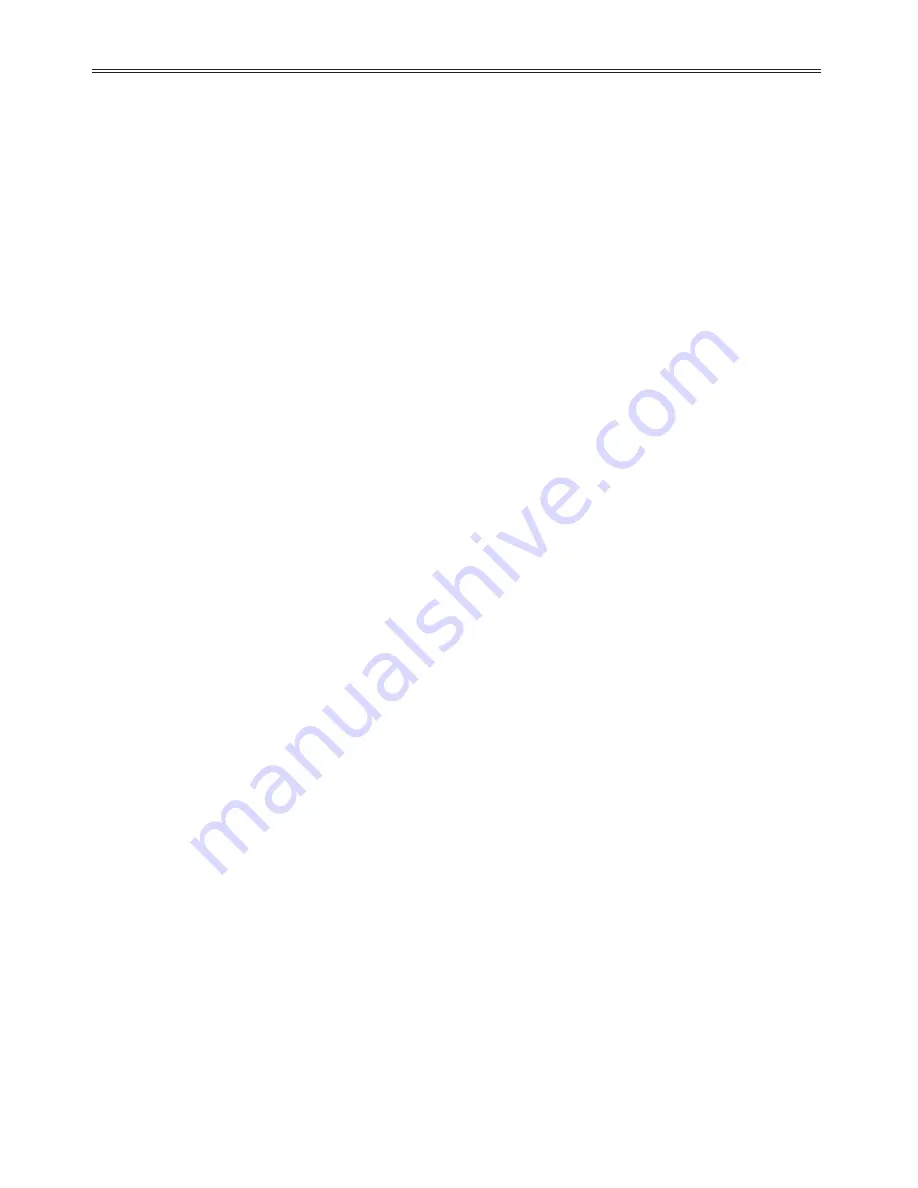
When selecting shielded cable for use as motor leads it is important to select a cable that is
designed for operation at the frequencies and power levels involved with a variable
frequency drive. Improper selection of motor cables can cause high potential to exist on
the shield. This could cause damage to the drive or other equipment and can pose a safety
hazard.
Many cable manufactures have shielded drive cable available. The following cables are
acceptable for this purpose: OLFlex Series 150CY, 110CY, 110CS, 100CY, 100CS, and
540CP. Siemens CordaflexSM is also acceptable. Some of these cables are
VDE-approved only; others carry VDE, UL, CSA, or a combination of these ratings. Be
sure to confirm that the cables meet the appropriate local regulatory requirements.
OLFlex cables are available from OLFlex Wire & Cable, 30 Plymouth Street, Fairfield NJ
07004, 800-774-3539
Cordaflex cables are available from Siemens Energy and Automation, Inc., Power Cables,
3333 State Bridge Road, Atlanta GA 30202, 800-777-3539
•
If the installation requires the use of an output reactor, the reactor, as with a line filter,
should be placed as close as possible to the drive.
•
Low voltage control wires longer than 1 meter (3ft) must use shielded cable and the
shield must be terminated at the proper CM connection. Note that the connection to the
CM rather than earth ground is allowed because the RSi SG drive has isolated control
inputs. If the signal run exceeds 9 meters (30ft), a 0-20mA or 4-20mA signal should be
used as it will have better noise immunity than a low-level voltage signal.
•
Other loads connected to the power source may produce voltage transients (spikes) that
may interfere with or damage the drive. Input line reactors or input filters can be used to
protect the drive from these transients.
•
If the drive is operated from switchgear devices or is in close proximity to switchgear
devices (in a common cabinet), the following procedures are recommended as a
precaution to prevent these devices from interfering with the drives operation.
•
Wire the coils of DC devices with freewheeling diodes. The diodes should be placed as
close as possible to the physical coil of the device.
•
Wire the coils of AC devices with RC type snubber networks. Place the snubber as close
as possible to the physical coil of the device.
•
Use shielded cables on all control and monitoring signals.
•
Route distribution cables (for example, power and contactor circuits) separately from the
drive's control and monitoring signal cables.
3.6.3
Wires and Terminal lugs
The input power and motor cables must be of the appropriate type and dimensions
according to the applicable national and local (NEC, etc) regulations to carry the rated
current of the drive. It is recommended that the cables be at least the size listed below in
the following table.
z
Note:
Strip the sheaths of the wire insulation 7mm when a ring terminal is not used for
power connection.
30
3 - RECEIVING AND INSTALLATION
Summary of Contents for RSi GX Series
Page 7: ...1 Introduction 1...
Page 15: ...2 Technical Specifications 9...
Page 24: ...Notes 18 2 TECHNICAL SPECIFICATIONS...
Page 25: ...3 Receiving and Installation 19...
Page 41: ...4 Operation 35...
Page 53: ...5 Parameter List 47...
Page 62: ...Notes 56 5 Parameter List...
Page 63: ...6 Parameter Descriptions 57...
Page 135: ...7 Remote Communication 129...
Page 149: ...8 Troubleshooting Maintenance 143...
Page 162: ...Notes 156 8 Troubleshooting Maintenance...
Page 163: ...9 Options 157...
Page 165: ...10 Appendices 159...