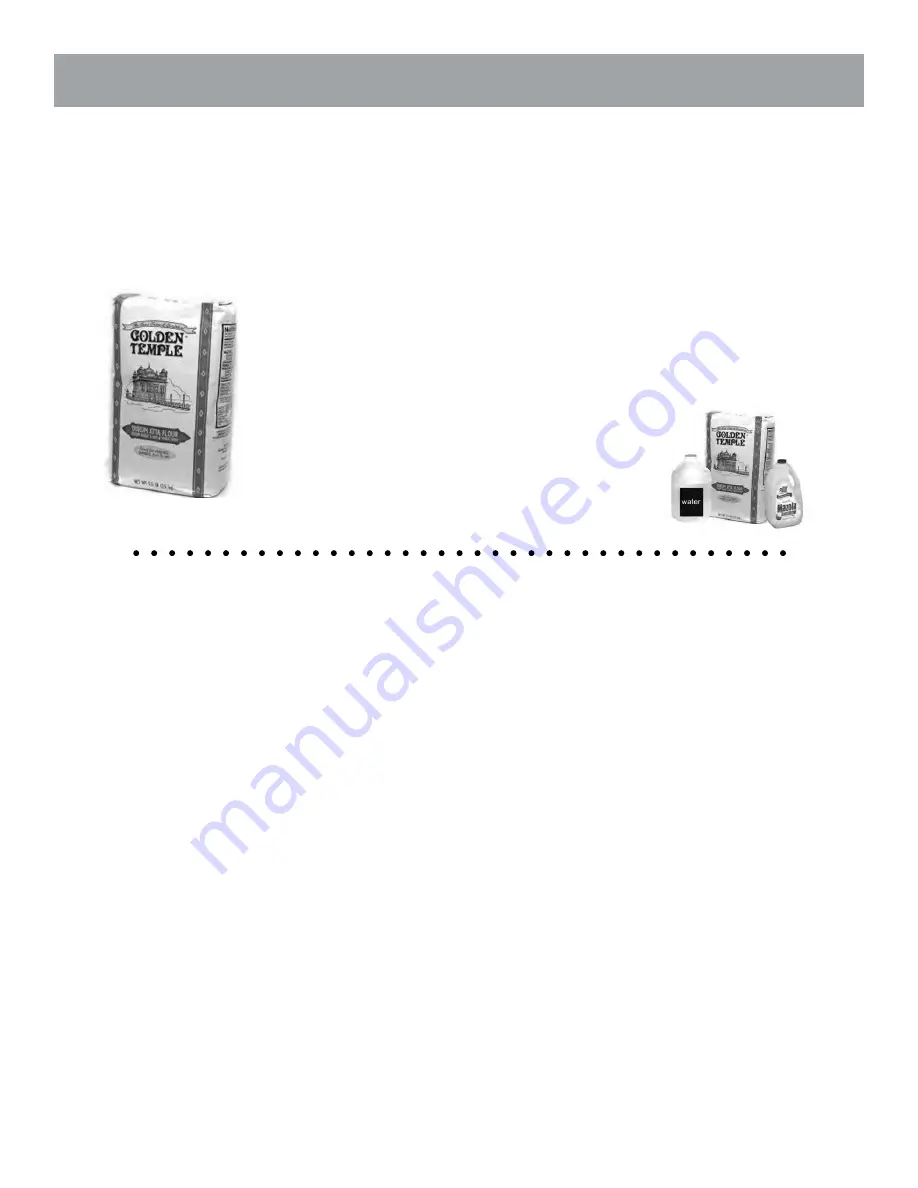
34
• 20 lbs.
Golden Temple Whole Wheat Flour
• 2 lbs.
Corn Oil, Canola Oil, Sunflower Oil or Olive Oil
• 10 lbs. 6 oz. Warm Water
Chapati Recipe Yields:
350 Chapati
Chapati Recipe
• Mix flour, oil and water together for 5-7 minutes or until fully developed
• Weigh out 3 1/2 lbs. rounds of chapati dough.
• Place chapati dough on a sheet pan and cover with plastic bun pan bag.
• Let chapati dough proof for 5 minutes.
• Select chapati dough batch and place on Divider/Rounder tray.
• Evenly spread chapati dough on tray and put it into Divider/Rounder.
• When finished, remove tray and place chapati dough balls on a sheet pan.
• Cover them with plastic bun pan bag. Place pans on rack.
• Allow chapati dough balls 30 or more minutes for proofing.
• When proofed, dust dough balls with flour and you’re ready to make chapati.
Ingredients:
Instructions:
Summary of Contents for Betamax 20
Page 2: ......
Page 4: ......
Page 6: ......
Page 8: ......
Page 58: ......
Page 59: ...54 Master Switch ITEM DESCRIPTION PART NUMBER QTY 1 Switch Push Pull 312300024 1 1...