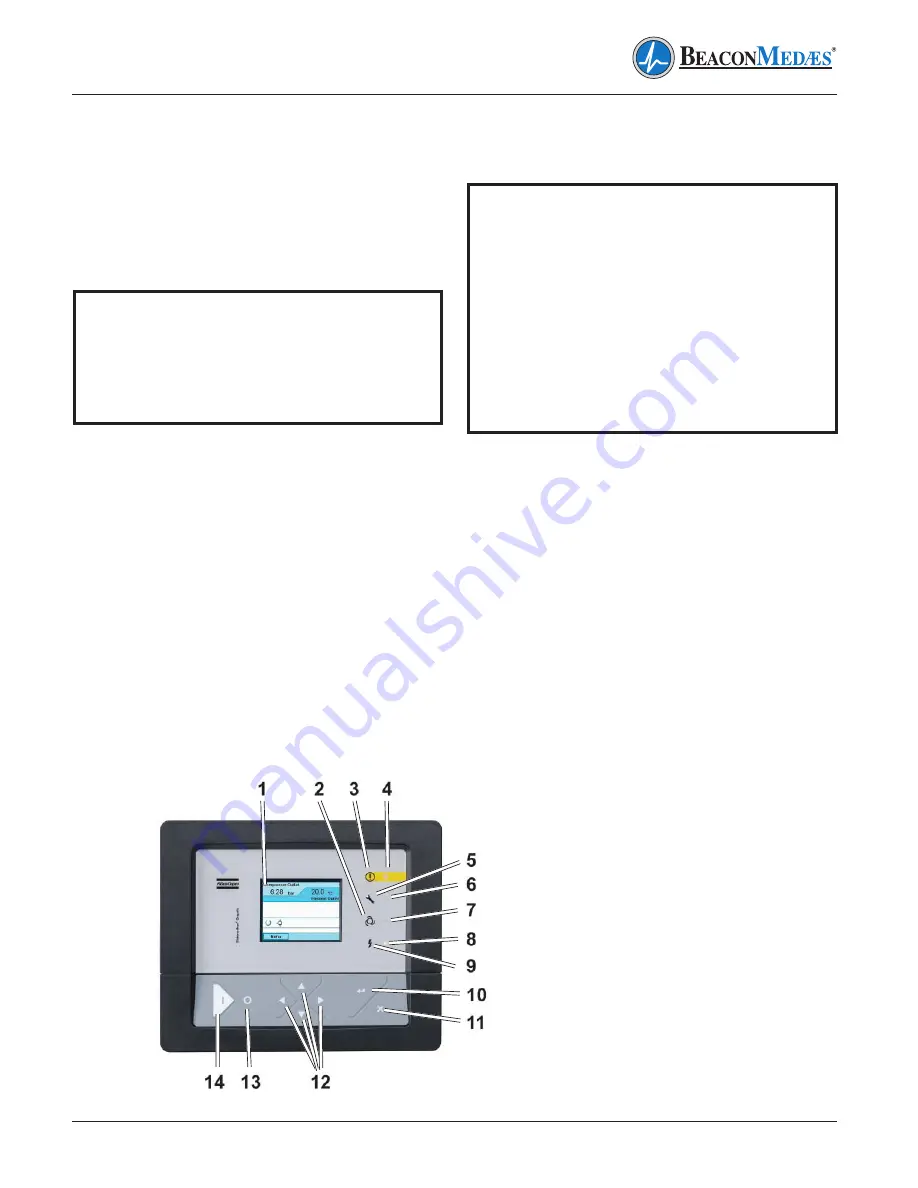
3-4
Z MED Medical Air System
4107 9022 67.00
3.2.3 Dryer Initial Start-Up
Refer to Section D.4.1 – Initial Start-Up section in
Appendix D Desiccant Dryer.
3.3 System Normal Start-Up
1.
Hospital shut-off valve – CLOSED
2. Dryer Outlet isolation valve – CLOSED
3. Receiver bypass valve – CLOSED
4. Compressor outlet valve – OPEN
5.
One dryer off-line – VALVES CLOSED
6. One dryer on-line – VALVES OPEN
7. Main electrical power on to system
8. Compressor disconnect switched turned on
9. Check that voltage LED light is “ON”, each
compressor and Central Control System pan-
el on dryer
13.
Stop the compressor. If necessary, top off
the gear casing with oil to the middle of the
sight glass (FIG 3.2.1b).
3.2.2 Compressor Start-Up
3.0 System Operation
WARNING!
The operator must apply all relevant
safety precautions, including those men-
tioned in the “Operation & Maintenance
Manual” supplied with each compressor.
1. Check the oil level, which must be in the mid-
dle of the sight glass (SG - FIG 3.2.1b) top off,
if necessary, with the correct type oil.
2.
On “ZR”
, check the setting of the valves (1, 2
& 3 - FIG 3.2.1c) as described in section 3.2.1.
This can be overlooked if, after previous op-
eration, the settings of these valves have not
been disturbed.
3. Close the manual condensate drain.
4. Open the air outlet valve (customer installed).
5. Switch on the voltage and check that the volt-
age on LED (8) lights up (FIG 3.2.2).
6. Press start button (14). The compressor
starts running and automatic operation LED
(7) lights up (FIG 3.2.2).
WARNING!
When the compressor is stopped and
automatic operation LED (8) is on, the
compressor may start automatically. If
the start/stop timer is active, the com-
pressor may start automatically, even if it
was stopped manually. Consult the user
manual for Elektronikon Regulator, sec-
tion “Programming Clock Function” in the
“Operation & Maintenance Manual” sup-
plied with each compressor.
FIG 3.2.2 Compressor Control Panel