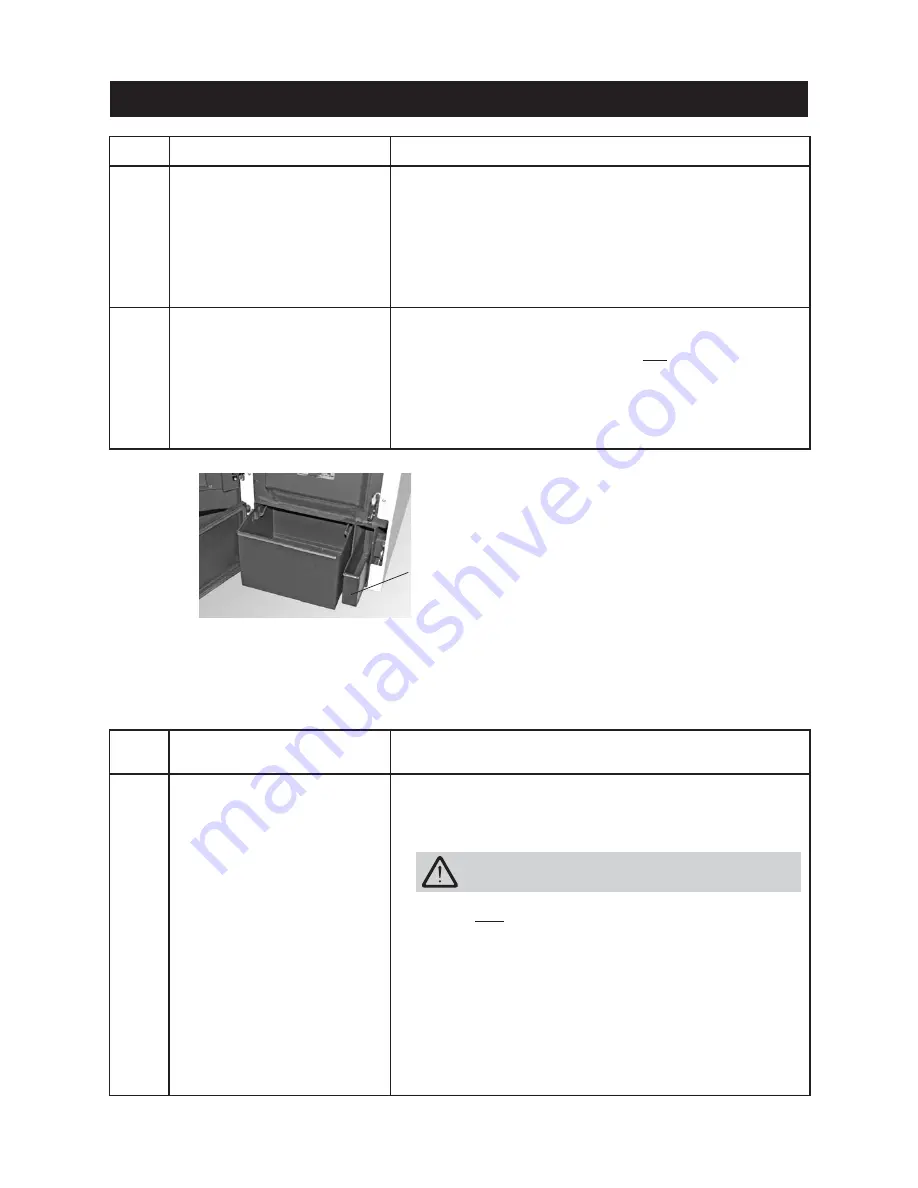
54
Troubleshooting
4.4
Alarm messages
Code Meaning/effect
Cause/remedy
FE 382
Fill level switch in reserve supply
container defective
Check the switch in the reserve supply
container. Press Reset.
The boiler does not operate.
a) Fill level switch (proximity switch) dirty, remove the dust (see section 3.7),
press the Reset button.
b) Fill level switch (proximity switch) in the reserve supply container defecti-
ve – inform Windhager Customer Service or a heating technician.
Emergency operation:
Switch off the feed unit (see section 2.8.1.3). Fill the reser-
ve supply container with pellets by hand, boiler may continue operating without
feed.
FE 390
Emergency operation!
Clean boiler and burner
Perform cleaning and confirm in operator
level.
The boiler is in cyclic operation, i.e. has idle times.
a) Boiler and burner must be cleaned or the both ash pan(s) (see Fig. 162)
emptied (see sections 3.4, 3.5 and 3.6). Following cleaning, confirm clea-
ning on the InfoWIN operator level (see section 2.8.1.1).
b) Motor or limit switch of ash compactor defective, inform Windhager Custo-
mer Service or a heating technician.
Fig. 162
Empty the ash pan(s) or remove the
ash from the heating surface duct
Ash pan for
heating surfaces
(accessories)
Code Meaning/effect
Cause/remedy
AL 005
Shake-out defective
Shake-out defective or sticking.
Clean the burner pot. Press Reset.
Shake-out motor no longer moves or no longer reaches the end position, boi-
ler switches to burnout mode.
a) Burner contamination; close combustion chamber doors, press reset but-
ton; once the alarm message is rectified, clean the burner pot as descri-
bed in section 3.6.
If the alarm message remains active, clean the burner pot as described in
section 3.6. Note: Grate plate at top can only be raised and removed when
closed. If the grate plate is not fully closed, vacuum it out. Close combus-
tion chamber door, press reset button, if the alarm message remains in
place, repeat the process or inform Windhager Customer Service or a hea-
ting technician.
b) Grate plate not inserted correctly or check correct installation position (see
section 3.6).
c) Motor for shake-out defective, inform Windhager Customer Service or a
heating technician.
d) Limit switch defective, inform Windhager Customer Service or a heating
technician.
The glow ignition is located in the primary air tube so avoid sha-
king the burner pot violently – risk of breakage!