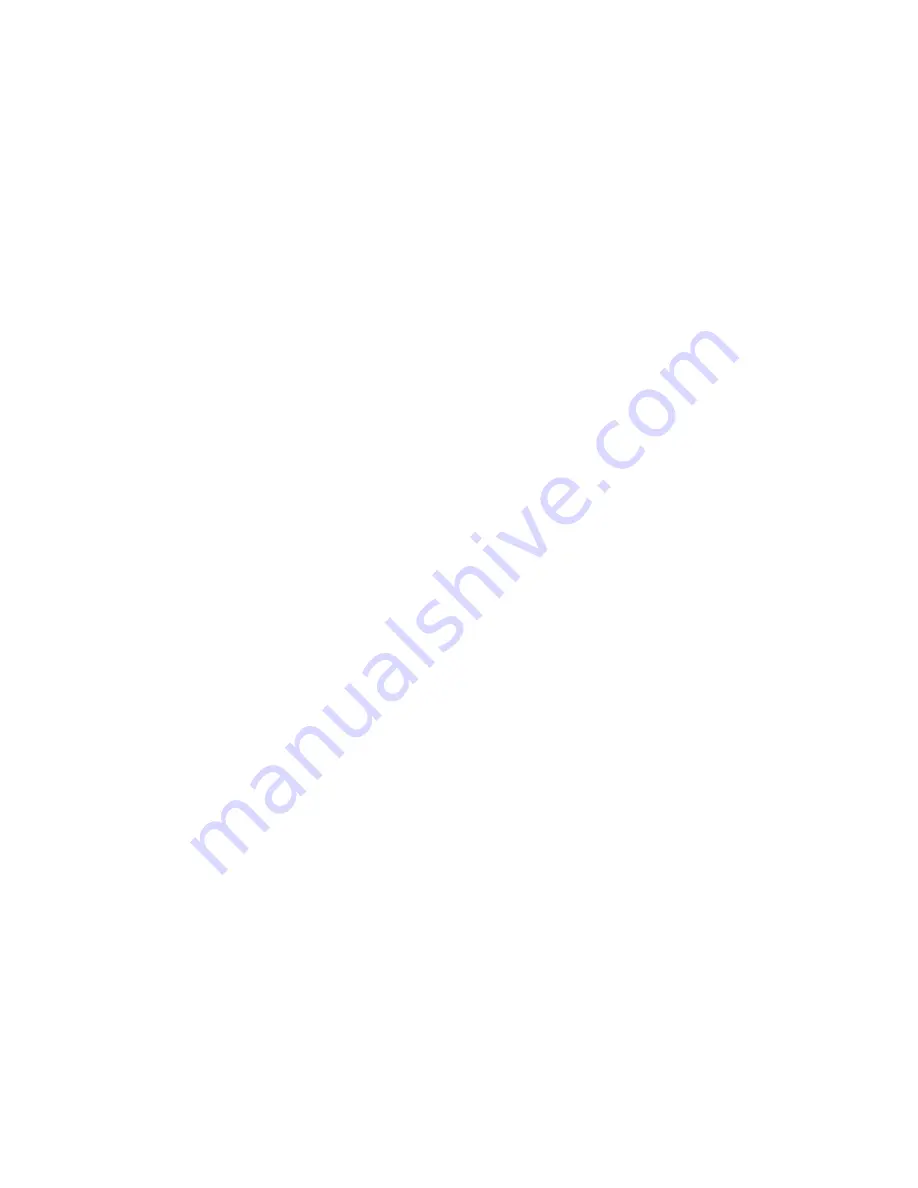
WAM Arm – User’s Manual
www.barrett.com
© 2008 Barrett Technology®, Inc.
Document: D1001, Version: AH.00
54 of 80
WAM’s M4 configuration. Basically, the sign changed from + to – for the M4
transmission.
•
The latest files in config/ will not necessarily match your WAM. You should
always use the config file that shipped with your WAM. Update that file with *new
features* from the latest config files, but be careful not to change the kinematic and
dynamic constants that are specific to your WAM.
3.
Mass parameters are inaccurate due to model errors, unmodeled parts, or machinist
tolerances.
Solution(s):
a)
On-line calibration (either static or dynamic) can yield better data than the model.
Barrett is working on calibration software and will notify the WAM User List when it
is released.
4.
Electrical wiring stiffness requires additional joint torque to overcome pulling effect near
joint limits
Solution(s):
a)
This requires complex modeling algorithms that Barrett has not yet developed.
5.
We depend on a sampled motor torque constant to be accurate across a batch of motors in a
manufacturing run. In fact, the torque constants could vary slightly.
Solution(s):
a)
Calibration software could reduce errors due to inaccurate torque constants. Barrett is
working on calibration software and will notify the WAM User List when it is
released.
Problem:
Safety Board is randomly rebooting. The pendants reinitialize themselves.
Reason(s):
1.
There are electrical noise spikes/dips in the power circuitry of the Safety Board.
Solution(s):
a)
Contact Barrett for a replacement board.
Problem:
Pendant lights do not come on (specifically the IDLE light), but Pucks are online
anyways, but do not make PWM sound when <SHIFT+ACTIVATE> is pressed.
Reason(s):
1.
The pendant is electrically damaged
Solution(s):
a)
Contact Barrett for repair.
Problem:
One or more joints of the WAM vibrate during trajectory following.
Reason(s):
1.
The PID control gains for the joint are too high. The default PID control gains assume
some non-zero payload in gravity. If you have no payload, or the joint is facing the floor or
the ceiling (that is, if gravity is not a factor and there is no externally-applied torque on the
joint), then the joint control gains could be too high.
Solution(s):
a)
Lower the PID gains for that joint (in the wam.conf file). Start by cutting P and D in
half.
Problem:
One or more joints of the WAM oscillate or otherwise go unstable during
trajectory following.
Reason(s):
1.
The PID control gains for the joint are too low.
Solution(s):
a)
Raise the PID gains for that joint (in the wam.conf file).
2.
The payload is too heavy, the motor torque is saturating at Max Torque (MT), and the
control can not keep up.
Solution(s):