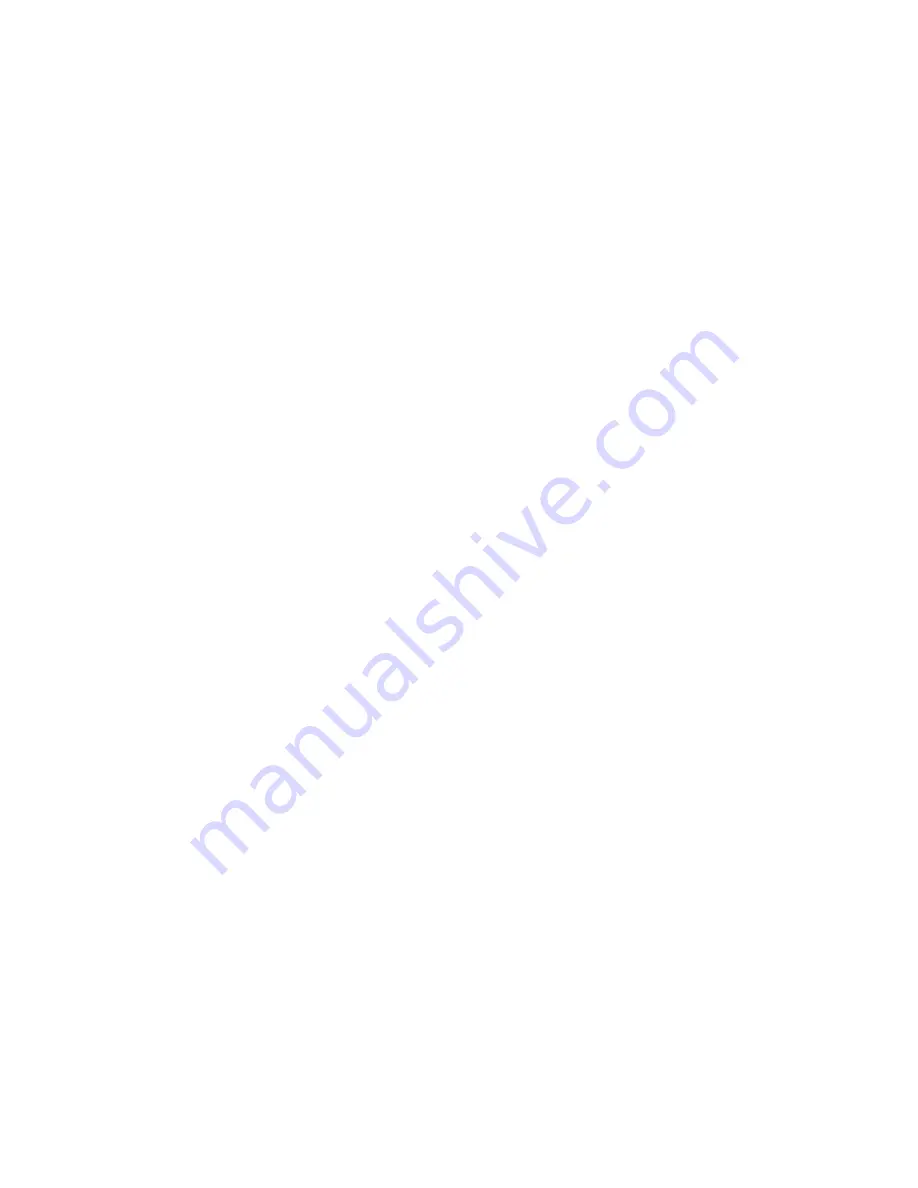
WAM Arm – User’s Manual
www.barrett.com
© 2008 Barrett Technology®, Inc.
Document: D1001, Version: AH.00
17 of 80
•
Remove/replace the WAM Wrist only as instructed in Section 3.4.
•
Monitor the operating temperature of the WAM so that it remains between 0
°
C and 70
°
C.
Under normal conditions, the Pucks operate between 40 and 60
˚
C. Idling the motors, when
possible, will help keep the temperature lower.
2.2 Safety System: Pendants
2.2.1 Safety
States
The WAM Arm has three safety states: E-STOP, IDLE, and ACTIVATED:
E-STOP
means there is no motor bus voltage, in fact the motor bus power and ground lines are
tied together, resulting in a “resistive braking” effect on the joints of the WAM Arm. The motor
controllers are off line and do not keep track of their motor positions in this state. E-STOP is
achieved by pressing the E-STOP button on either pendant. In this state, neither the IDLE nor
ACTIVATE button lights are lit on the control pendant.
IDLE
means there is voltage applied to the motor bus and the motor controllers are on line and
keeping track of their motor positions, but they are commanded to tie their motor phase leads
together (also resulting in a braking effect), and they will ignore any command torque sent to
them. To put the WAM Arm into the IDLE state (which will also reset any existing faults), press
and hold the Shift button on the control pendant, then press the Reset/Idle button (yellow) and
release both buttons. The yellow Idle button will light up, indicating that the WAM Arm is now in
the IDLE state. Make sure both E-STOP buttons are reset (popped up) before attempting to change
modes.
ACTIVATED
means the motor controllers are actively applying any commanded torque they
receive from the control PC. To put the WAM into the ACTIVATED state, press and hold the
Shift button on the control pendant, then press the Activate button (green) and release both
buttons. This state may only be reached when
all
of the status lights are showing OK (green). All
warnings or faults must be cleared before activating the WAM. The green Activate button will
light up, indicating that the WAM Arm is now in the ACTIVATED state.
2.2.2 Status
Lights
The WAM Arm has five sets of status lights: Velocity, Torque, Voltage, Heartbeat, and Other.
Velocity:
Before the WAM Arm’s joint positions are initialized by the PC control software, the
velocity status lights indicate the state of the WAM’s angular joint speed. By default, there is a
yellow LED warning when any joint exceeds 0.5 radians/sec and a red LED fault when any joint
exceeds 2 radians/sec. The joint number responsible for the warning/fault is indicated by the
single-character display on each pendant. After the WAM Arm’s joint positions are initialized, the
safety system begins calculating and monitoring the WAM’s elbow and arm endpoint velocities in
Cartesian space instead of monitoring individual joint velocities. By default, there is a warning
when either the elbow (single-character “E”) or arm endpoint (single-character “A”) exceeds 0.5
m/s and a fault when either one exceeds 2 m/s. These defaults are modifiable in software (see 6.3).
Torque:
The torque status lights indicate the state of the torque commands being received by the
WAM Arm from the PC control software. If the PC sends non-zero torques while the WAM is in
the IDLE state (the yellow Reset/Idle button is lit), the safety system will display a torque
warning- prohibiting the WAM Arm from being activated. If the WAM Arm is in the
ACTIVATED state (the green Activate button is lit) and the PC sends torques which exceed the
default torque warning or fault levels, the torque warning or fault light will be lit- and the
offending motor number will be shown in the single-character display. If a torque limit is