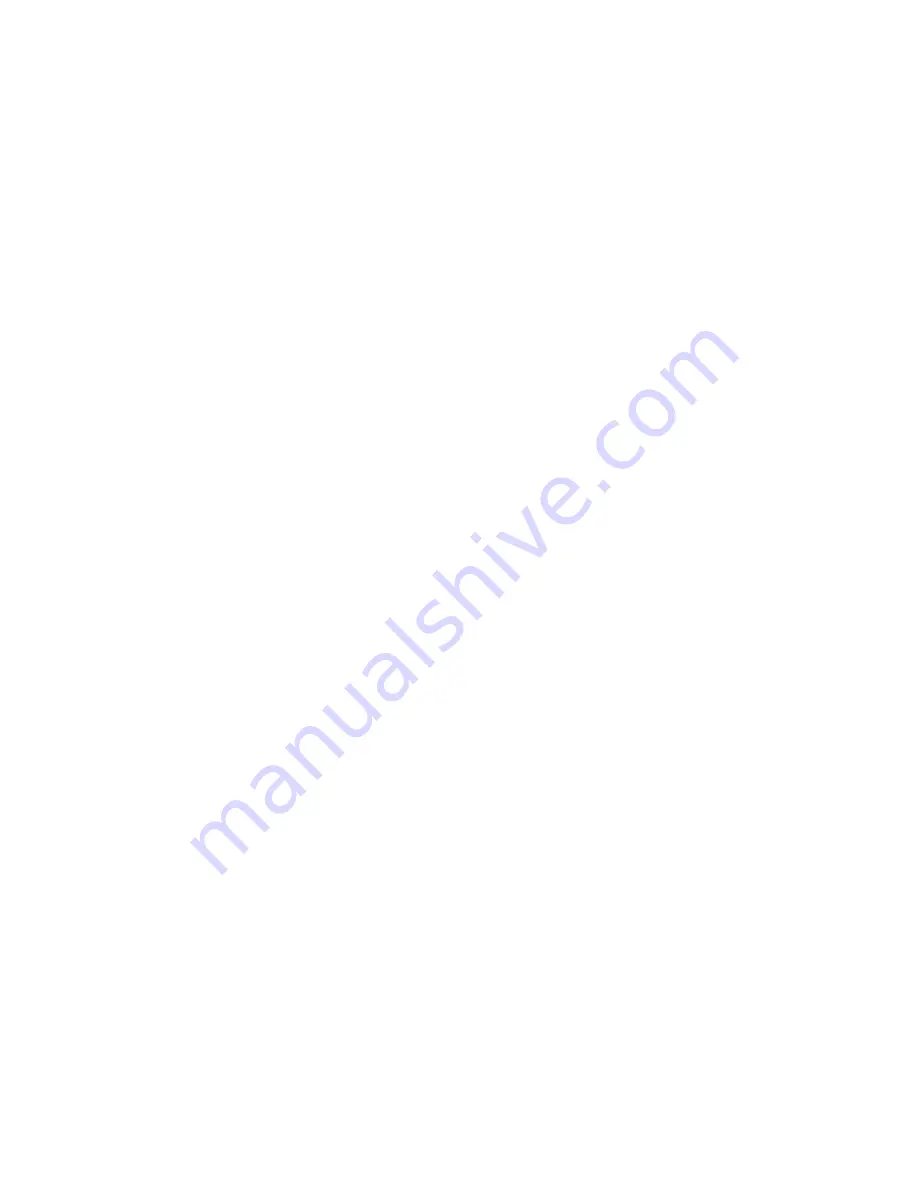
WAM Arm – User’s Manual
www.barrett.com
© 2008 Barrett Technology®, Inc.
Document: D1001, Version: AH.00
52 of 80
on the CANbus is approximately 850 uS for a 7-DOF and 500 uS for a 4-DOF. This
takes up a significant amount of the total control loop time.
c)
If you built your own WAM PC, a system hardware interrupt might be causing a
realtime glitch. Check your installation against: http://www.rtai.dk/cgi-
bin/gratiswiki.pl?Latency_Killer
d)
Extra getProperty() or setProperty() calls could be exceeding the CANbus bandwidth.
setProperty() takes 75 uS without verification, getProperty() takes 150 uS. You might
try staggering these function calls across multiple control cycles.
2.
CANbus communication problem
Solution(s):
a)
Use the btutil utility application to verify that the Puck firmware versions match for all
motor Pucks. Load matching firmware onto all motor Pucks, if necessary.
b)
Ensure that CANbus is properly terminated to minimize signal reflections. There is a
120 Ohm termination resistor in the wrist module (7-DOF) and blank outer link (4-
DOF). If you are using the internal WAM PC, switches 1-2 and 1-3 should be “out”
(see Section 3.5). This terminates the CANbus at the Safety Board with a 120 Ohm
resistor. If you are using an external WAM PC, the purple CANbus cable has a 120
Ohm resistor in the connector at the PC end. In this case, switches 1-2 and 1-3 should
be “in”.
c)
Use btutil to ensure that there are no conflicting Puck IDs on the CANbus. Each Puck
must have a unique ID. If the Pucks are not enumerating correctly, disconnect them
from the CANbus on-by-one until you find the one causing the conflict. Use btutil to
set a new Puck ID for that puck.
3.
Grounding problem
Solution(s):
a)
Eliminate CANbus ground loops. The CANbus shield is connected to Earth ground on
the Safety Board. If your PC is also grounded, you should use an opto-isolated
CANbus card to prevent ground loops.
b)
Eliminate power bus ground loops. The frame of the WAM is connected to Earth
ground through the blue DC power cable. The frame of the 48 VDC supply is also
Earth-grounded. If there is an additional electrical connection between the frame of the
WAM and the frame of the power supply (such as a metal table or mounting bracket),
this can cause a ground loop and undesired operation.
Problem:
Running “sh makeall” causes a number of error messages appear, including
“cannot find –lntcan”.
Reason(s):
1.
The linker is looking for the wrong CAN driver
Solution(s):
a)
Edit your btclient/config.mk file to specify the correct CAN driver
2.
The CAN driver is not installed
Solution(s):
a)
Install the correct CAN driver for your CAN hardware
Problem:
A mechanical cable is fraying, birdnesting, or has come loose
Reason(s):
1.
The maximum recommended payload was exceeded
Solution(s):
a)
Note that the payload specification does not take into account accelerated loads. If you
attach a 3 kg load to the 4-DOF and accelerate it at 2 g’s, the WAM experiences a 6 kg
load, exceeding the recommended payload. The cable should be replaced before
further use.
2.
A brass termination slipped off the end of the cable.
Solution(s):
a)
This is a manufacturing defect. Contact Barrett to get the cable replaced.