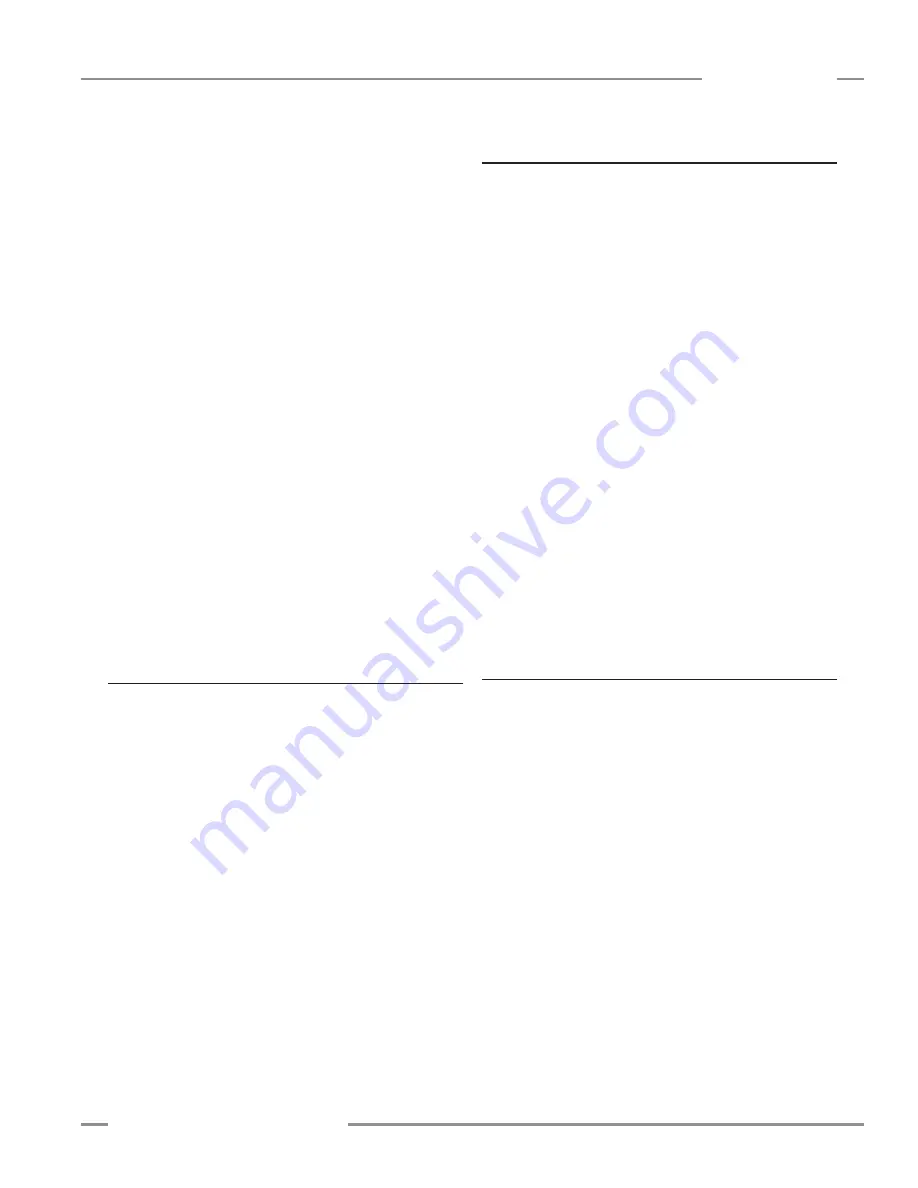
P/N 130426 Rev.
D
9
Banner Engineering Corp.
•
Minneapolis, U.S.A.
www.bannerengineering.com • Tel: 763.544.3164
A-GAGE EZ-ARRAY
Instruction Manual
Overview
•
Transitions (TRN): The number of changes from blocked to
clear status and from clear to blocked status. (If beams 6-34
are blocked, then there is a clear-to-blocked transition from
beam 5 to beam 6, and a blocked-to-clear transition from
beam 34 to beam 35.) Transition mode can be used to count
objects within the array.
• Outside Dimension (OD):
The inclusive distance (measured
in beams) from the first blocked beam to the last blocked
beam.
• Inside Dimension (ID):
The number of made beams, between
the first and last blocked beams.
• Contiguous First Beam Blocked (CFBB):
The location of
the first blocked beam in the largest group of adjacent blocked
beams.
• Contiguous Last Beam Blocked (CLBB):
The location of
the last blocked beam in the largest group of adjacent blocked
beams.
• Carpet Nap and Carpet Edge:
These measurement modes
are used to measure the location of carpet backing and tuft,
and are selectable only via the PC interface, and only when
the Scan Type “
Carpet Nap
” is selected. The modes can be
measured from either end of the sensor, but at least 10 beams
(2") must be blocked from one edge.
• Special:
This mode is reserved for specialized applications;
contact the factory for information.
1.11 Analog Output Configuration
Analog output configuration assigns analog outputs 1 and 2 to
one of the measurement modes described in Section 1.10. When
the selected measurement mode involves first or last beam
blocked or made (unblocked), the assigned output will vary in
proportion to the beam number identified during a scan. When the
measurement mode involves total beams blocked or made, that
assigned output will vary in proportion to the total beams counted
during a scan.
Analog outputs may have Null and Span values set in the PC
interface, in addition to a filter setting (to smooth the output) and
Zero Value (to specify the output value when the measurement
mode value is zero). See Section 5.8 for more information.
1.12 Discrete Output Configuration
Discrete Output 1; Receiver Interface
When the receiver interface is used for configuration, the
measurement mode assigned to discrete output 1 is the same
as that assigned to analog output 1. When the analog output
detects a target present, discrete output 1 conducts (normally
open).
Discrete Output 2; Receiver Interface
Discrete output 2 (only) has two options: alarm and
complementary (measurement) operation.
Alarm:
Output 2 energizes when the receiver detects a sensor
error (such as a disconnected cable) or whenever the excess
gain of one or more beams becomes marginal.
Complementary (Measurement):
Discrete output 2 operation
is complementary to discrete output 1 (when output 1 is ON,
output 2 is OFF, and vice versa).
Discrete Output 1 and 2 Configuration; PC Interface
When the PC interface is used for configuration, the discrete
outputs have more options: either discrete output can be
assigned to any of the measurement modes, high and low set
points can be added, the outputs can be inverted, and hysteresis
values can be set, as well as a scan number to smooth output
performance. Discrete output 2 can be assigned to alarm mode
via the PC interface also. See Section 5.9 for more information.
1.13 Serial Communication
When the PC interface is used, the receiver communicates
with a process controller via a Modbus RTU-485 interface. The
PC interface software has a Communications Settings menu
that includes the selected sensor communications port, options
(either leave this field set at
DPB1
, or change it to
No Echo
Suppression
), and a read-only window that provides current
communications status. Advanced settings are also accessible,
including baud rate, timeout (in milliseconds), message delay (in
milliseconds), sensor address, parity, retry and byte delay. See
Section 5.10 and the Appendix for more information.