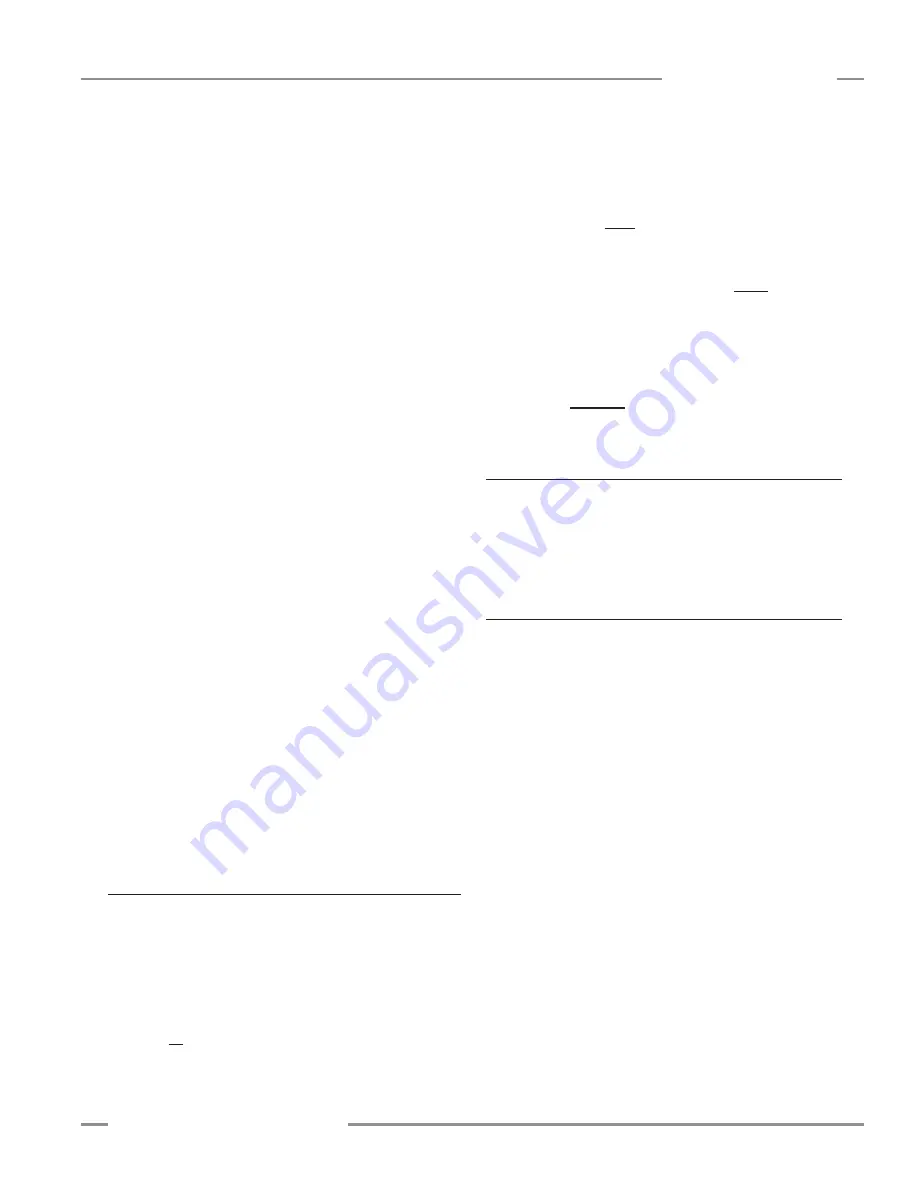
P/N 130426 Rev.
D
29
Banner Engineering Corp.
•
Minneapolis, U.S.A.
www.bannerengineering.com • Tel: 763.544.3164
A-GAGE EZ-ARRAY
Instruction Manual
PC Interface
use the up/down arrows to the left of the field. If a new sensor
address is selected, update the GUI address via
Options
> Communications Settings
(Ctrl + M) to enable further
communication.
• Parity:
Select
Odd
,
Even
, or
None
.
• Baud Rate
is the data communication rate between the
sensor and the computer used for configuration or the process
controller. Choose from three values:
9600
,
19200
, and
38400
.
• Modbus Timeout
can be used to relax communication timing.
The Modbus standard (
Compliant
setting) defines spacing
between words within a message to be no longer than the time
required to transmit 1.5 bytes of information. However, the
time between successive bytes within a serial message can
be extended (
Extended
setting) to allow communication with a
slower device.
5.11 Part Number and Version Info View
This view provides basic read-only reference information about
the connected emitter and receiver. Information includes the
receiver part number, firmware version numbers, and hardware
date codes.
5.12 System Diagnostics View
This view provides read-only information about the connected
emitter and receiver, for diagnostic purposes. This information
may be useful if factory-assisted troubleshooting is required.
Refer to Section 4.6 for possible error codes and corrective
action.
• Channel Status fields
display the number of emitter and
receiver channels (which should be identical), the location of
the first bad emitter channel, if any, and the level of optical
power being delivered by the emitter.
• Operational Status fields
display the overall Error Code (or
System Status), plus the status of each receiver DIP switch
position, regardless of whether they are enabled.
• Output Status fields
display the status of each output
individually.
• Service Status
displays the sensor time of service, updated
every two hours.
Health:
Output is normally active, becomes inactive when an
error occurs.
Alarm:
Output is normally inactive, becomes active when an
error occurs.
• Demodulation
is used to smooth the discrete output response.
Each discrete output can respond after each sensor scan,
or the response time can be increased by increasing the
demodulation. Increasing the demodulation increases the
required number of consecutive qualifying scans (that have a
measurement mode value within the prescribed window and
hysteresis values) to change the discrete output state. The
maximum demodulation value is 250 scans and is selected
independently for each output.
• Threshold Low and Threshold High Values
are used to
“window” the measurement values that control a discrete
output. The values each identify a beam in the array (beam 1
being closest to the sensor display). At each scan, the sensor
processes the status of the optical channels and determines
values for the selected measurement modes. For the Discrete
Output analysis, the measurement values are compared to the
low and high threshold. If the selected measurement value is
between the low and high threshold values (including the low
and high limit), then the sensor will register a valid condition.
After the specified number of consecutive scan response
values (see “
Demodulation
”), the sensor will recognize that
the conditions specifying the discrete output are met and the
output will change state.
Hysteresis
prevents unstable output conditions when the scan
analysis value exactly matches the threshold.
• Hysteresis Low
value determines the amount of change that
must occur beyond the low threshold to cause that output to
change state. The default
Hysteresis Low
setting is one beam
less than the
Threshold Low
setting.
• Hysteresis High
value determines the amount of change that
must occur beyond the high threshold to cause that output
to change state. The default
Hysteresis High
setting is one
beam more than the
Threshold High
setting.
5.10 Comm Config View
This view is used to define the serial communication parameters
that the sensor uses for communication with the GUI or the
process controller. If any changes are made to fields in this view,
update the fields accordingly in
Options > Communications
Settings
(Ctrl + M
)
to enable further communication.
• Address
determines the sensor location (from
1
to
247
;
default is
65
) on the process controller network. Adjust by
highlighting the existing number and overtype a new value, or