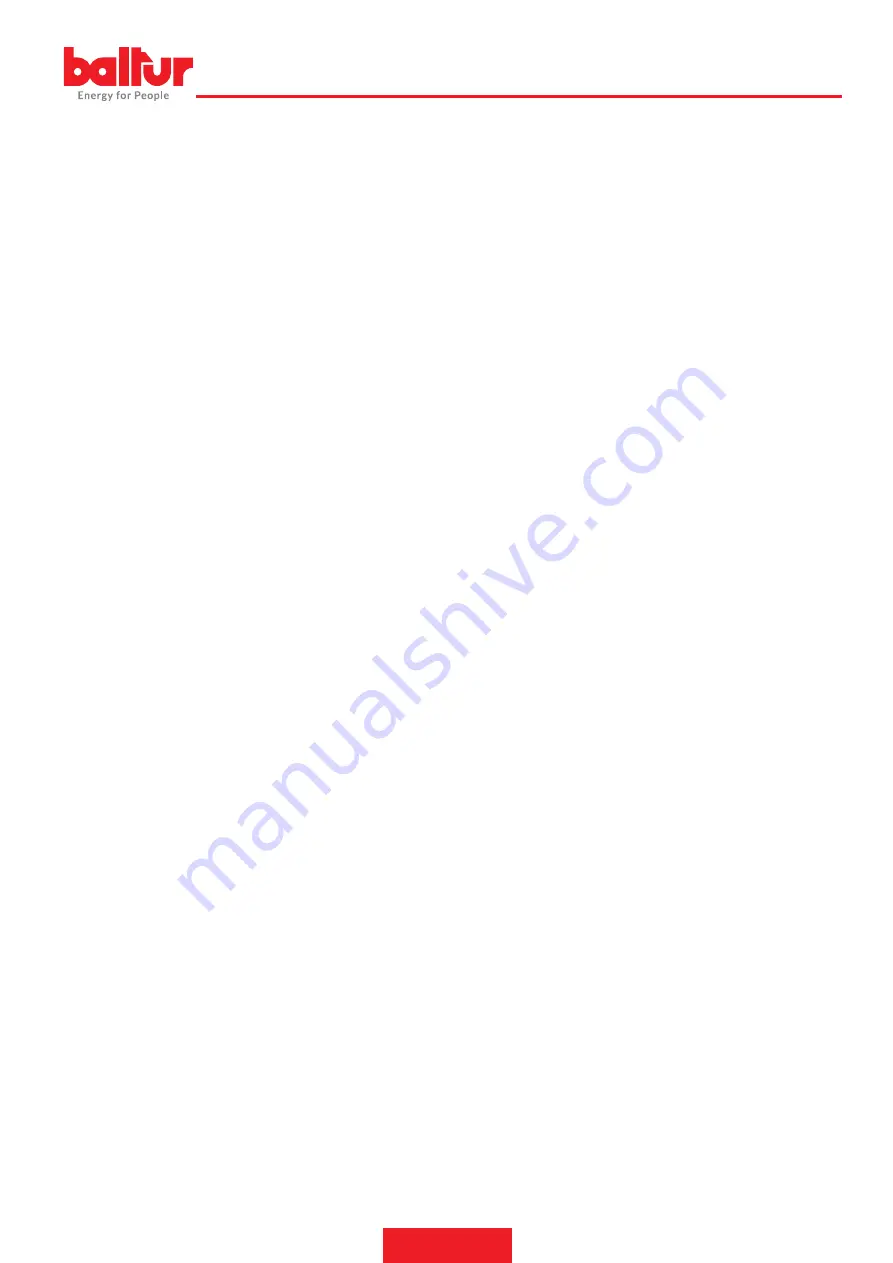
TO BE CARRIED OUT BY THE INSTALLER
•
Install a suitable disconnecting switch for each burner supply line.
•
The disconnection must be carried out by means of a device
complying with the following requirements:
-
A disconnecting switch - circuit breaker, according to IEC 60947-
3 for at least the equipment category AC-23 B (non-frequent
operations on highly inductive loads or AC motors).
-
A control and protection switching device suitable for isolation
according to IEC 60947-6-2.
-
A switch suitable for isolation according to IEC 60947-2.
• The disconnecting device must:
-
Ensure the isolation of the electrical equipment from the power
supply line when in the stable OFF position indicated with “0”,
and be in a stable ON position indicated with “1”.
-
Feature a visible gap between contacts or a position indicator
that cannot indicate OFF (isolated) until all contacts are actually
open and the requirements for the isolation function are met.
-
Feature a grey or black actuator which can be easily identified.
-
Be padlockable in the OFF position. In case of lock-out, remote
and local activation will not be possible.
-Disconnect all the active conductors of its power supply circuit.
For TN power supply systems, the neutral conductor can be
disconnected or not, except in the countries where the discon
-
nection of the neutral conductor (if used) is mandatory.
•
Both disconnecting controls must be located at a height between
0,6 m ÷ 1, 7 m with respect to the working plane.
•
Since circuit breakers are not emergency devices, they can
feature an additional cover or a door, which can be easily opened
without any key or tool. Its function must be clearly indicated, e.g.
with the relevant symbols.
•
The burner can be installed only in TN or TT systems. It cannot
be installed in isolated system of IT type.
•
Do not reduce the section of the conductors. A maximum
short-circuit current of 10kA is required at the connection point
(before protection devices) in order to ensure the correct interven
-
tion of protection devices.
• The automatic reset function on the thermal device which protects
the fan motor cannot be enabled (by irreversibly removing the
relevant plastic label) for any reason.
•
As for the connection of cables to the terminals of the electrical
equipment, make sure that the earth conductor length is such as
to ensure that it is not subject in any way to accidental discon
-
nection following any mechanical stress.
•
Provide for a suitable emergency stop circuit able to perform a
simultaneous stop in category 0 both on 230Vac single-phase
line and on 400Vac three-phase line. The disconnection of both
power supply lines ensures a “safe” transition in the shortest time
possible.
•
The emergency stop will have to be performed complying with the
following requirements:
-
The electrical emergency stop device must fulfil the “special
requirements for control switches with direct opening” (refer to
EN 60947-5-1: 2016, Attachment K).
-It is recommended that the emergency stop device is red and
the surface behind it is yellow.
-
The emergency action must be of the hold-to-run type and
require a manual operation to be restored.
-
When the emergency device is restored, the burner must not
be able to start autonomously, but a further “run” action by the
operator must be required.
-
The emergency activation device must be clearly visible and
easily reachable and actionable in the immediate vicinity of the
burner. It must not be enclosed within protection systems or
behind doors that can be opened with keys or tools.
•
In the case that the burner is positioned in such a way that it
cannot be easily reached, activated and serviced, provide for a
suitable service plane in order to ensure that the control panel is
positioned between 0.4 ÷ 2.0 metres with respect to the service
plane. This is to ensure an easy access by the operator for main
-
tenance and adjustment operations.
•
When installing the input power and control cables of the burner
electrical equipment, remove the protection plugs and provide
for suitable cable glands so that an “IP” protection degree equal
to or higher than that indicated on the burner nameplate can be
ensured.
5 / 38
0006160334_202305
ENGLISH
Summary of Contents for TBML 900 ME
Page 2: ......
Page 35: ...SCHEMI ELETTRICI TBML 600 ME 800 ME 900 ME BT 335 33 38 0006160334_202305 ITALIANO...
Page 36: ...TBML 600 ME 800 ME 900 ME BT 335 34 38 0006160334_202305 ITALIANO...
Page 37: ...TBML 600 ME 800 ME 900 ME BT 335 35 38 0006160334_202305 ITALIANO...
Page 38: ...TBML 600 ME 800 ME 900 ME BT 335 36 38 0006160334_202305 ITALIANO...
Page 39: ...I1 I2 BA I4 I3 TBML 600 ME 800 ME 900 ME BT 335 37 38 0006160334_202305 ITALIANO...
Page 73: ...WIRING DIAGRAMS TBML 600 ME 800 ME 900 ME BT 335 33 38 0006160334_202305 ENGLISH...
Page 74: ...TBML 600 ME 800 ME 900 ME BT 335 34 38 0006160334_202305 ENGLISH...
Page 75: ...TBML 600 ME 800 ME 900 ME BT 335 35 38 0006160334_202305 ENGLISH...
Page 76: ...TBML 600 ME 800 ME 900 ME BT 335 36 38 0006160334_202305 ENGLISH...
Page 77: ...I1 I2 BA I4 I3 TBML 600 ME 800 ME 900 ME BT 335 37 38 0006160334_202305 ENGLISH...
Page 79: ......