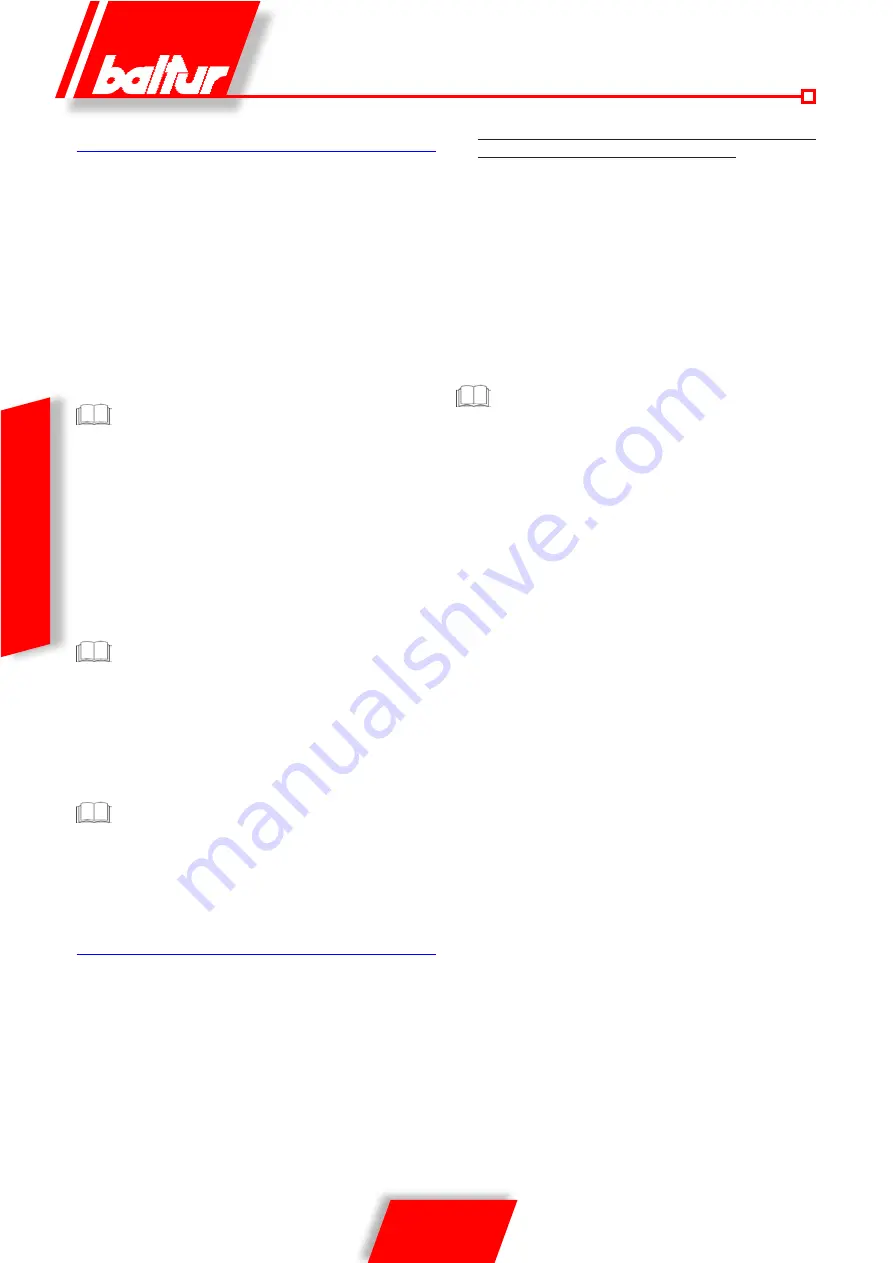
19 / 34
0006081545_201305
ENGLISH
FIRST FILLING UP OF PIPELINES
After making sure that the protective plastic caps inside the pump
fittings have been removed, proceed as follows:
• Set the burner switch on “O” to prevent an automatic connection
of the burner.
• Make sure, in case of a three-phase burner, that the motor
revolves anti-clockwise when watching it from the pump side.
The rotation direction can be determined also looking at the
direction of fan rotation through the inspection window on the
back of the scroll. To start the motor, close the remote control
switch manually (pressing on the mobile part) for a few seconds
and watch the direction of the rotation of the fan. If it is necessary
to change the rotation direction, reverse the two phases to the
motor contactor terminals K1.
To determine the rotation direction, wait until the fan turns
very slowly, because it is quite easy to misinterpret the
rotation direction.
• Disconnected, if already connected, the flexible pipes from both
suction and return lines.
• Dip the end of the suction flexible pipe into a vessel containing
either lubrication oil or fuel oil (do not use low viscosity products
such as gas-oil, light oil, kerosene. etc).
• Now press key (9) on the control panel to start the motor and the
pump. Wait until the pump has sucked in an amount of lubricant
equal to 1 or 2 glassfuls, then stop. This operation will prevent
the pump from operating dry and will increase the suction power.
Pump operating at 2800 r.p.m. must not work dry otherwise
they will jam (seizure) within a very short time.
• Now connect the flexible pipes to the suction line and open
all the gate valves fitted on this line and any other similar fuel
cut-off device.
• Press key 9 again to start the pump, which will suck fuel from
the tank. When fuel is seen coming out of the return pipe (not
yet connected), stop.
If the pipe is long, it may be necessary to bleed the air out
through the cap; if the pump is not fitted with a cap, remove
the pressure gauge connector cap.
• Connect the flexible return hose to the pipe and open any gate
valves fitted on this pipe. The burner is now ready to start up.
IGNITION AND REGULATION
Before starting up the burner make sure that:
• The right type of fuel has been selected.
• Feeding line connections to thermostats or pressure switches
are made exactly according to electric diagram of the control box.
• There is fuel oil in the tank and water in the boiler.
• All the gate valves fitted on the fuel oil suction and return pipes
should be open; the same thing applies to any other fuel cut-off
device.
• Make sure that discharge of combustion products takes place
freely (boiler and chimney gate valves open).
• Make sure that the combustion head penetrates the furnace to
the extent requested by the boiler manufacturer. Make sure the
air shut-off device on the combustion head is in the right position
to ensure a correct combustion; the air passage between disk
and head should be significantly reduced in case of reduced
fuel delivery. When fuel delivery is high, the air passage should
be consequently increased, see chapter “COMBUSTION HEAD
ADJUSTMENT”.
• The nozzles fitted on the burner must be suitable for the
boiler capacity. If necessary, replace them with suitable ones.
In no case should the quantity of fuel delivered exceed the
maximum amount required by the boiler and the maximum
amount allowed for the burner.
To start the burner proceed as follows:
The burners have a switch to pass manually from the 1st to
the 2nd stage.
• To prevent ignition of the second flame, turn the 1
st
and 2
nd
stage
switch on the printed circuit to the 1
st
stage position.
• Adjust the air in the amount presumed to be necessary for the
1
st
stage ignition using the special cam of the air adjustment
servomotor.
• Set the air adjustment device on the combustion head in
an intermediate position (see “AIR ADJUSTMENT ON THE
COMBUSTION HEAD”).
• Activate the main switch and the control panel switch.
• The programmer starts to operate and activates the burner
devices according to the pre-set program. The burner will start
operation as described in the Chapter “DESCRIPTION OF
OPERATION”.
• When the burner is operating in the 1
st
stage, adjust the amount
of air necessary to ensure an efficient combustion, see “AIR
ADJUSTMENT ON THE BURNER HEAD” and 000293 for 1
st
flame diesel oil adjustment cam.
• After adjusting the air for the 1
st
stage, stop the burner by cutting
off the current from main switch. Activate the electrical circuit that
controls the activation of the second flame by turning the 1
st
and
2
nd
stage switch on the printed circuit to the 2
nd
stage position
• Adjust the air in the amount presumed necessary for
the maximum capacity (2nd stage) using the
screw(s) corresponding to the bearing (13).
- in a clockwise direction the air flow increases,
- in an anti-clockwise direction the air flow decreases.
• Now connect the burner again; it will start and automatically
switch to the 2
nd
stage according to the pre-set program.
Summary of Contents for TBML 80 MC
Page 2: ......
Page 33: ...31 34 0006081545_201305 ENGLISH WIRING DIAGRAM...
Page 34: ...32 34 0006081545_201305 ENGLISH...
Page 35: ...33 34 0006081545_201305 ENGLISH...
Page 67: ...31 34 0006081545_201305 ESPA OL ESQUEMA EL CTRICO...
Page 68: ...32 34 0006081545_201305 ESPA OL...
Page 69: ...33 34 0006081545_201305 ESPA OL...
Page 101: ...31 34 0006081545_201305 ITALIANO T RK E DEUTSCH SCHALTPLAN...
Page 102: ...32 34 0006081545_201305 ITALIANO T RK E DEUTSCH...
Page 103: ...33 34 0006081545_201305 ITALIANO T RK E DEUTSCH...
Page 135: ...31 34 0006081545_201305 T RK E ELEKTR K EMASI...
Page 136: ...32 34 0006081545_201305 T RK E...
Page 137: ...33 34 0006081545_201305 T RK E...
Page 140: ...2 34 0006081545_201305 5 8 SUNTEC 14 15 LME 73 16 17 19 19 21 21 22 24 25 26 28 31...
Page 141: ...3 34 0006081545_201305 BALTUR...
Page 142: ...4 34 0006081545_201305 3 2 RC B...
Page 146: ...8 34 0006081545_201305 5 6 0002934670 3 2 4 1 7...
Page 147: ...9 34 0006081545_201305 10 11 12 000293640 65 80...
Page 148: ...0002911090 10 34 0006081545_201305 EN 676 1 2 3 4 5 6 7 1200 8 9 10 11 12 13...
Page 154: ...16 34 0006081545_201305 LME 73 1 EK EK 2 1 2 BCI AZL2 1 TW...
Page 157: ...19 34 0006081545_201305 O K1 9 2800 9 1 2 1 2 1 1 1 000293 1 1 1 2 2 2...
Page 158: ...13 12 acc_reg001 psd TBML 80MC 003 psd 20 34 0006081545_201305 2 13 2 2 CO2 10 13 2...
Page 159: ...1 7 8 2 3 4 5 6 10 9 Display TBML 80 PN GAS L 21 34 0006081545_201305 1 2 3 4 5 3 7 8...
Page 161: ...23 34 0006081545_201305 1 8 1 1 2 LME 73 200 500 1 3 50 C 5 10 C...
Page 164: ...26 34 0006081545_201305 TBML 80 MC 1 2 3 4 5 6 7 8 9 10 4 0002936380...
Page 169: ...31 34 0006081545_201305...
Page 170: ...32 34 0006081545_201305...
Page 171: ...33 34 0006081545_201305...
Page 174: ...2 34 0006081545_201305 5 8 10 11 SUNTEC 14 15 LME 73 16 17 19 19 21 21 22 24 25 26 28 31...
Page 175: ...3 34 0006081545_201305 a b c a b c d e f g...
Page 176: ...4 34 0006081545_201305 3mm 2 RC a b c d e a b a b c d...
Page 180: ...8 34 0006081545_201305 6 5 0002934670 3 2 7 4 1...
Page 181: ...9 34 0006081545_201305 M 10 11 4 12 0002936400 DN65 DN80...
Page 182: ...0002911090 10 34 0006081545_201305 E N 6 7 6 1 2 3 4 5 6 7 1200 kW 8 9 10 11 12 13...
Page 188: ...16 34 0006081545_201305 LME 73 1 EK LED EK LED 1 2 BCI AZL2 1 LED TW...
Page 191: ...19 34 0006081545_201305 O K1 9 1 2 2800 rpm 9 000293 13 CO2 10 13...
Page 192: ...13 12 acc_reg001 psd TBML 80MC 003 psd 20 34 0006081545_201305...
Page 193: ...1 7 8 2 3 4 5 6 10 9 Display TBML 80 PN GAS L 21 34 0006081545_201305 1 2 3 L E D 3 4 5 3 7 8...
Page 195: ...23 34 0006081545_201305 UV UV UV UV UV UV LME 73 200 500 1 1 50 C 5 10 C...
Page 198: ...26 34 0006081545_201305 TBML 80 MC 1 2 3 4 5 6 7 8 9 10 4 0002936380...
Page 199: ...27 34 0006081545_201305 TBML 120 160 200 MC 1 2 3 4 5 6 7 8 9 3 TBML 200 MC 10 4 0002936380...
Page 203: ...31 34 0006081545_201305...
Page 204: ...32 34 0006081545_201305...
Page 205: ...33 34 0006081545_201305...
Page 207: ......