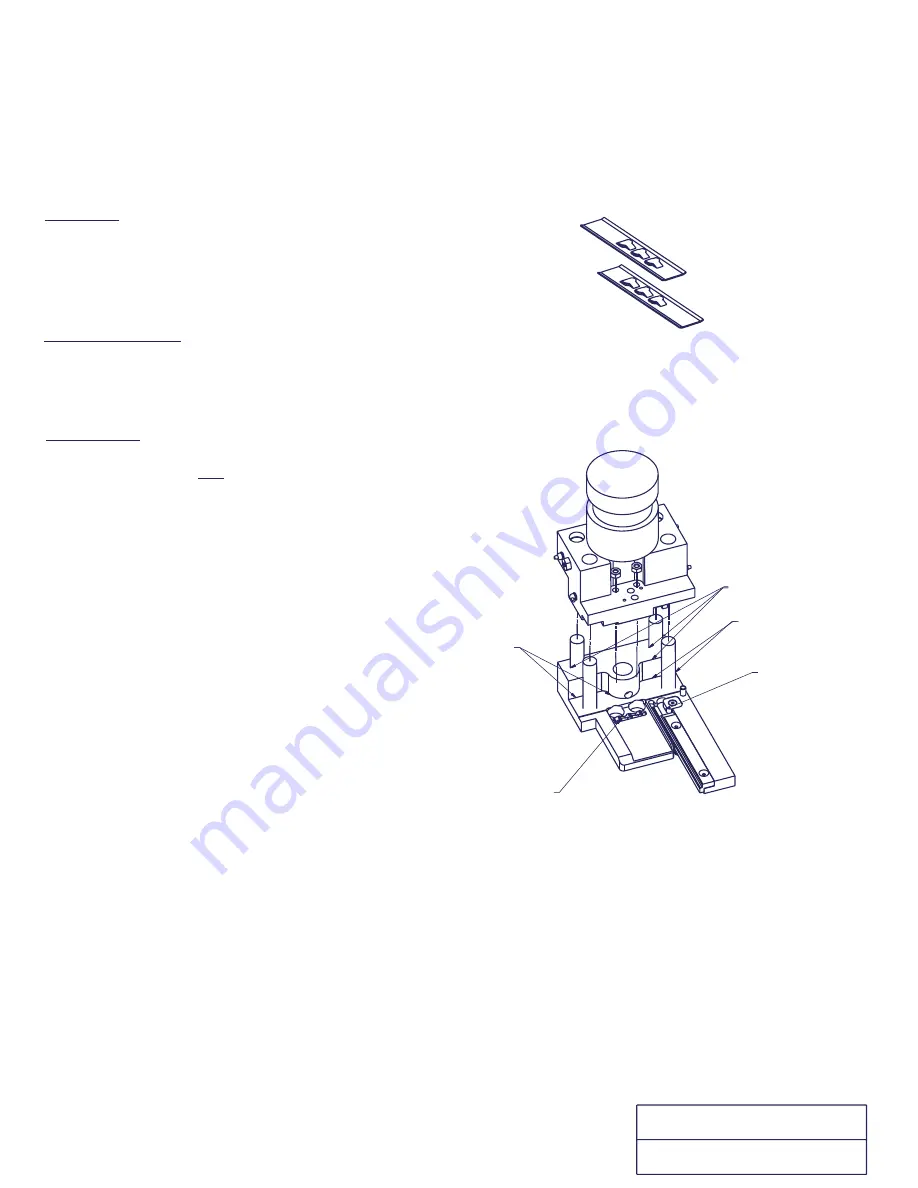
TroubleShootingStrapping
Both seals are stamped in center of strapping.
Crimps are correct, but seals do not stay together.
Problem #1
Possible Cause
Correction
Banders are not allowed to go to full stroke.
There is an obstruction.
Note: Banders do not have to be
disassembled. Drawing is
disassembled for ease of viewing.
Clean Area #1
Clean Area #1
Clean Area #1
Clean Area #3
Clean Area #2
There is hay obstruction that is not
allowing banders to go full stroke.
Area's are indicated that must be
cleaned daily.
Most people clean Area # 2 regularly,
but Area #1 and Area #3 must also be
cleaned reguarly. Hay packed in
these areas have proved suffecient
enough to cause banders to fail.
Strapping Troubleshooting
If a bundle has a miss tie, the first step is to look at both ends of the
failed strapping and refer to the possible options below.
Summary of Contents for GFC 100
Page 2: ......
Page 4: ......
Page 8: ...Operator s Manual 3 Serial Number Location...
Page 10: ...Operator s Manual 5 Safety Decals...
Page 11: ...Operator s Manual 6 Safety Decals...
Page 12: ...Operator s Manual 7 Safety Decals...
Page 13: ...Operator s Manual 8...
Page 31: ...Operator s Manual 26 Hydraulic Manifold Layout Front Manifold...
Page 32: ...Operator s Manual 27 Inside Banding Box Manifold...
Page 33: ...Operator s Manual 28 Outside Banding Box Manifold...
Page 34: ...Operator s Manual 29 Electrical Layout Front Relay Box located behind banding drums...
Page 35: ...Operator s Manual 30 Band Relay Box located in Banding Box...
Page 52: ...Operator s Manual 47 If the Vertical Plunger cylinder is fully retracted...