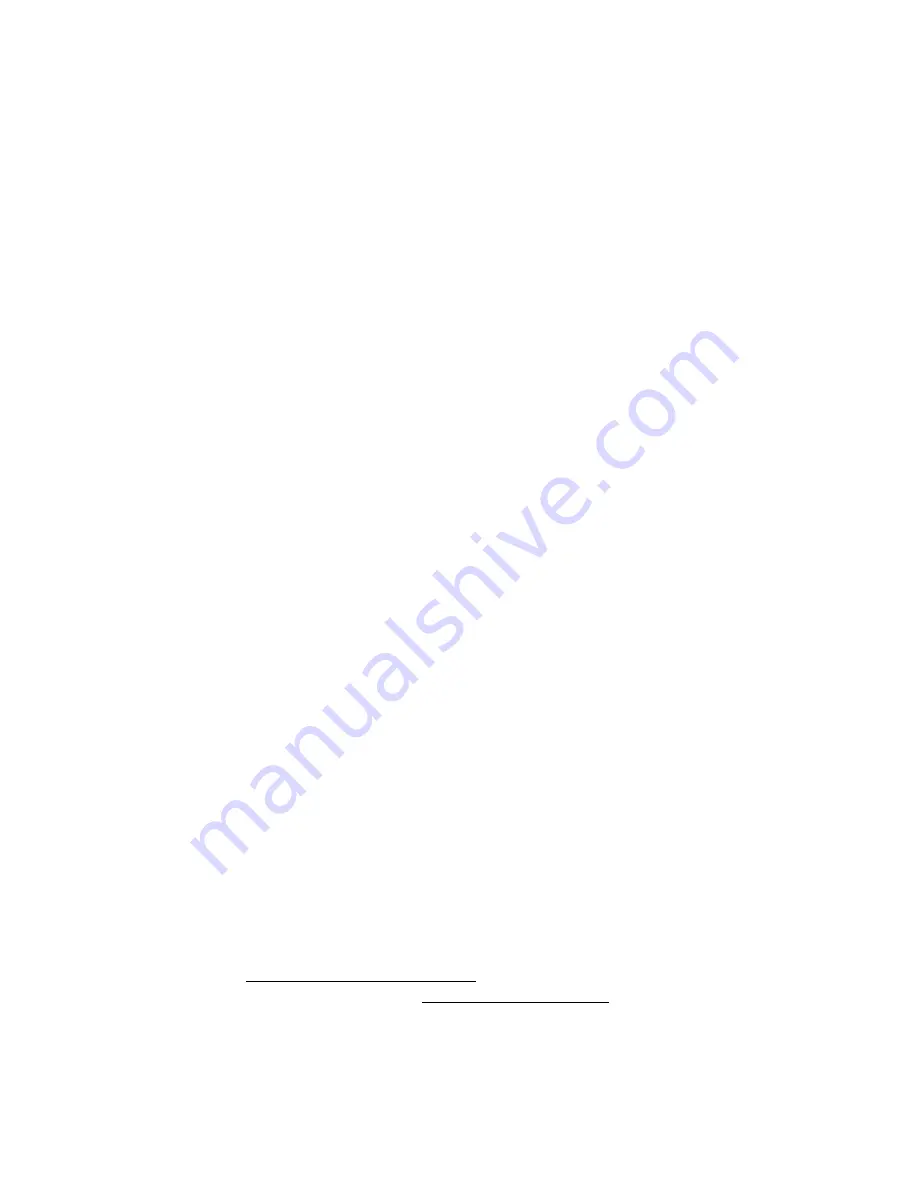
UMAX140610. LIN
– J1939 CAN Protocol Converter with PWM Output. Version 1
Page: 30-81
(i.e. transmitted over CAN), then Xmin would be -20 and Xmax would be 125 when used the
linear formula.
In all cases, the controller looks at the
entire range
of the data in the Y-Axis setpoints and
selects the lowest value as the MinOutRange and the highest value as the MaxOutRange.
They are passed directly to other function blocks as the limits on the Lookup Table output. (i.e
used as Xmin and Xmax values in linear calculations.)
However, if some of the data points are
‘Ignored’
as described in Section 3.4.4, they will not be
used in the Y-Axis range determination. Only the Y-Axis values shown on EA will be
considered when establishing the limits of the table when it is used to drive another function
block, such as an PWM Output.
3.4.3 Default Configuration, Data Response
By default, all Lookup Tables in the ECU are disabled (
“X-Axis Source”
equals
‘Control
Source Not Used’.
) If they were to use the default settings for CAN Receive messages instead
as the X-Axis and output Duty cycle (percentages), they could be used to control the PWM
Output. If a non-linear response for one or more of the outputs is required, the user can easily
use the table(s) to create the desired response profiles.
Recall, any controlled function block which uses the Lookup Table as an input source (not only
the PWM Output) will also apply a linearization to the data.
Therefore, for a 1:1 control
response, ensure that the minimum and maximum values of the output (Ymin and Ymax
in Figure 3
) correspond to the minimum and maximum values of the table’s Y-Axis
(Xmin and Xmax in Figure 3).
To control
“PWM Output” by “CAN Received Message 1” modified by “Lookup Table 1”, it is
recommended to do so in the following order:
a) Change PWM Output
“Output at Minimum Command”
and
“Output at Maximum
Command”
to the desired limits.
b) Configure the desired Control Source (i.e. CAN Receive Message) and set the appropriate
limits.
c) Change the Lookup Table 1
“X-Axis Source”
setpoints. (If applicable)
At this point, the X-Axis limits will match the control source, and the Y-Axis limits and the Y-
Axis limits would correspond to the PWM Output range, as a percentage.
d) Update the X and Y setpoints for the application
Note: Order (b) to (d) holds true for all configuration done using any Lookup Table function
block.
All tables (1 to 10) are disabled by default (no control source selected). However, should an
“X-Axis Source”
be selected, the Y-Axis defaults will be in the range of 0 to 100% as
described in the “Y-Axis, Lookup Table Output” section above. X-Axis minimum and maximum
defaults will be set as described in the “X-Axis, Data Response” section above.
By default, the X and Y axes data is setup for an equal value between each point from
the minimum to maximum in each case.