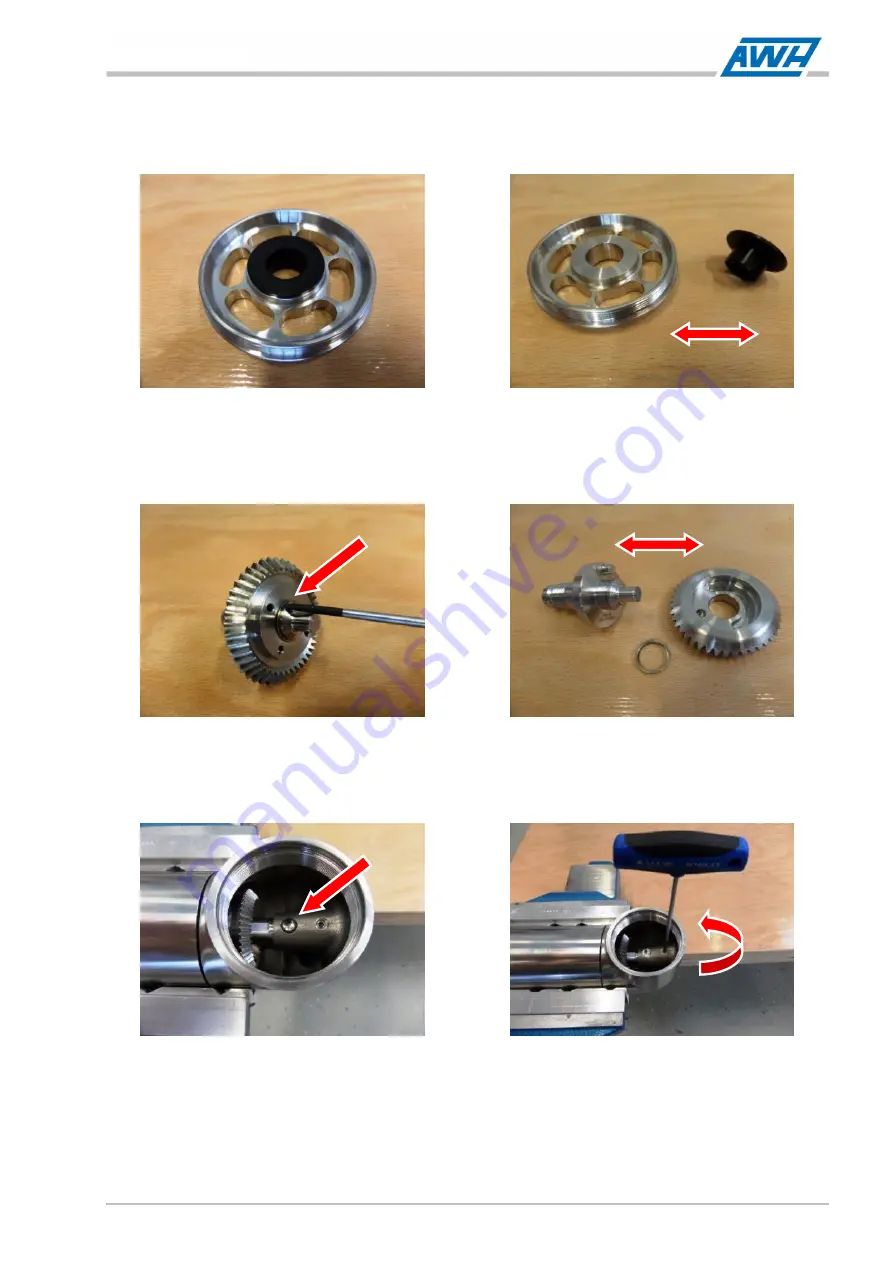
Jet Cleaner TANKO-MX
7 Maintenance
Operating/Installation Instructions 2019/08
69/102
10. Slide the bearing plate (28) with the collar bushing (08) from the driver shaft (25).
11. Push the collar bushing (08) out of the bearing plate (28) with an auxiliary tool (e.g. drift).
12. Lever the spiral circlip (31) out of the internal groove on the driver shaft (25), by inserting the flat tip
of a small screwdriver on the removal notch, and screw it out in a spiral pattern.
13. Pull the bevel gear wheel for the nozzle carrier (26) from the driver shaft (25).
14. The cylindrical pin (35) is pressed into the driver shaft (25) and should not be removed.
15. Pull the bushing (09) from the shaft-axle connection (24) with a set of pliers or lever it out with the
flat tip of a small screwdriver.
16. Unfasten the set screw (34) on the drift of the shaft-axle connection (24) with a hexagon socket
wrench size 2.5 mm and unscrew it.
17. Hold the device firmly with one hand and unfasten the vise.
18. Fasten the device vertically in the lower area of the shaft-axle connection (24) so that the
connection cover (01) faces upwards and the thread for the bearing plate (28) of the shaft-axle
connection (24) faces to the side.