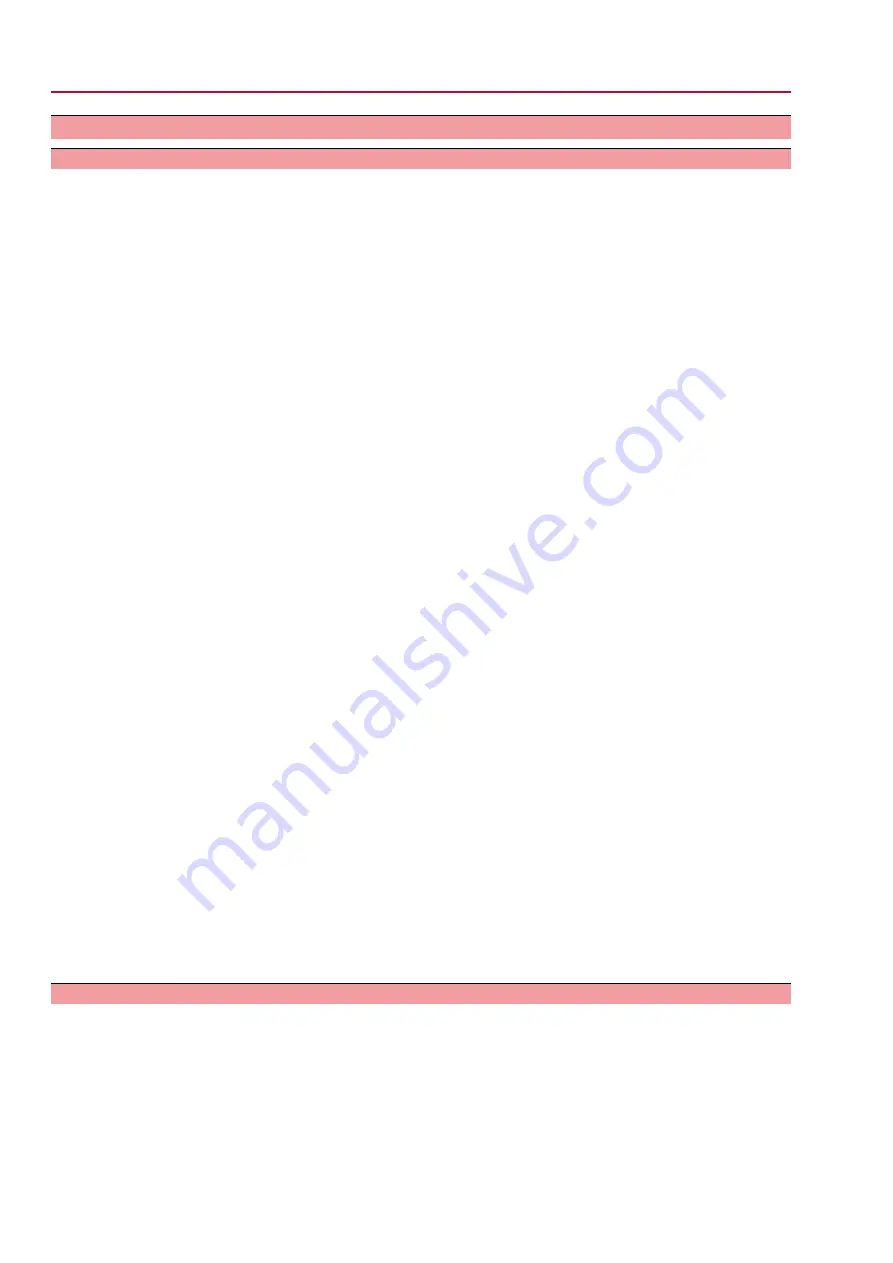
1.
Safety instructions
1.1.
Prerequisites for the safe handling of the product
Standards/directives
The end user or the contractor must ensure that all legal requirements, directives,
guidelines, national regulations and recommendations with respect to assembly,
electrical connection, commissioning and operation are met at the place of installation.
They include among others:
●
Applicable configuration guidelines for fieldbus applications.
Safety instructions/
warnings
All personnel working with this device must be familiar with the safety and warning
instructions in this manual and observe the instructions given. Safety instructions
and warning signs on the device must be observed to avoid personal injury or property
damage.
Qualification of staff
Assembly, electrical connection, commissioning, operation, and maintenance must
be carried out by suitably qualified personnel authorised by the end user or contractor
of the plant only.
Prior to working on this product, the staff must have thoroughly read and understood
these instructions and, furthermore, know and observe officially recognised rules
regarding occupational health and safety.
Commissioning
Prior to commissioning, imperatively check that all settings meet the requirements
of the application. Incorrect settings might present a danger to the application, e.g.
cause damage to the valve or the installation. The manufacturer will not be held
liable for any consequential damage. Such risk lies entirely with the user.
Operation
Prerequisites for safe and smooth operation:
●
Correct transport, proper storage, mounting and installation, as well as careful
commissioning.
●
Only operate the device if it is in perfect condition while observing these instruc-
tions.
●
Immediately report any faults and damage and allow for corrective measures.
●
Observe recognised rules for occupational health and safety.
●
Observe national regulations.
●
During operation, the housing warms up and surface temperatures > 60 °C may
occur. To prevent possible burns, we recommend checking the surface temper-
ature prior to working on the device using an appropriate thermometer and
wearing protective gloves.
Protective measures
The end user or the contractor are responsible for implementing required protective
measures on site, such as enclosures, barriers, or personal protective equipment
for the staff.
Maintenance
To ensure safe device operation, the maintenance instructions included in this manual
must be observed.
Any device modification requires prior written consent of the manufacturer.
1.2.
Range of application
AUMA part-turn actuators are designed for the operation of valves, e.g. butterfly
valves and ball valves. For actuators made of bronze, the deployment on military
vessels is restricted.
Other applications require explicit (written) confirmation by the manufacturer.
The following applications are not permitted, e.g.:
●
Industrial trucks according to EN ISO 3691
●
Lifting appliances according to EN 14502
●
Passenger lifts according to DIN 15306 and 15309
4
SGM 04.1 – SGM 14.1 / SGMR 04.1 – SGMR 14.1
Safety instructions
Profibus DP