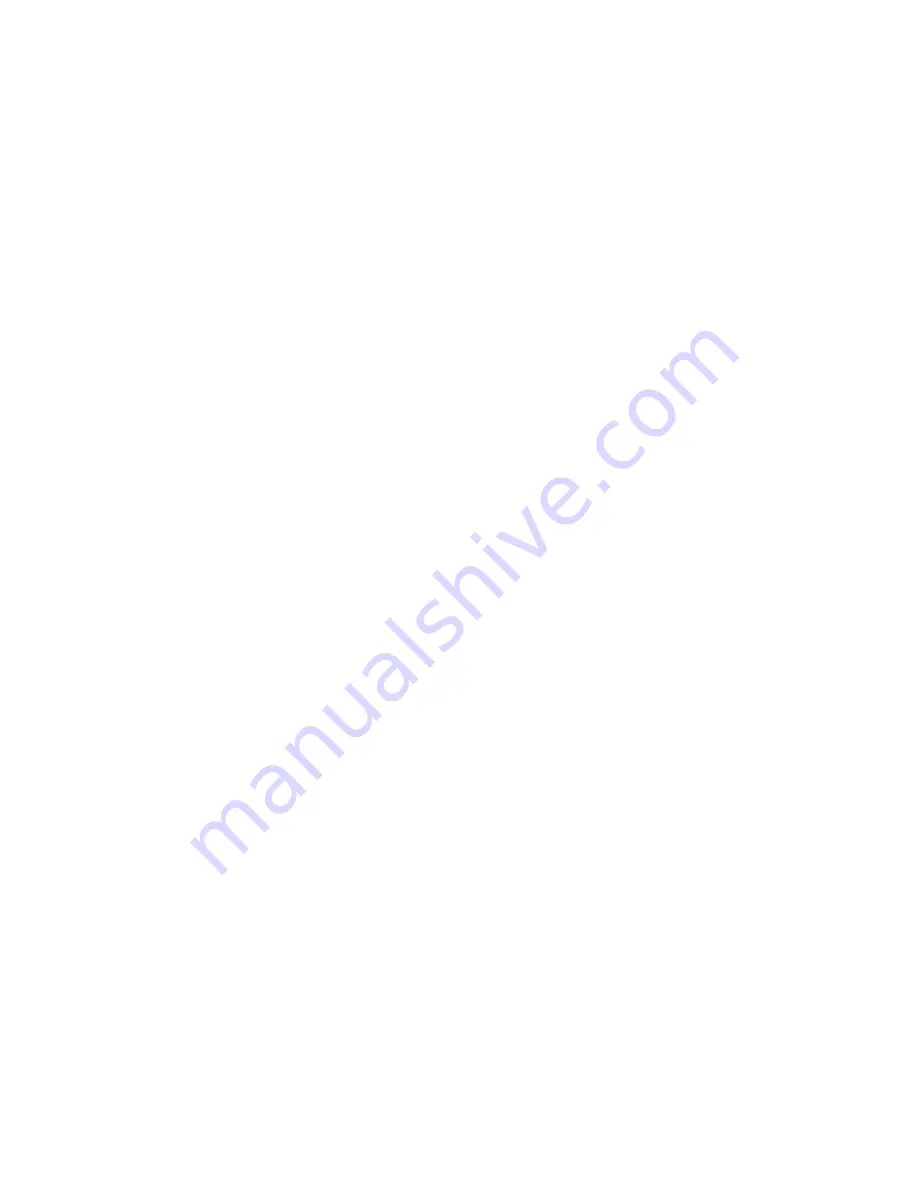
11
Shortcut:
RA
Format:
[Addr#]RA [X] [Y] [Z] [F]
Function:
Returns the present values on the MS2000's 4-channel ADC. The X and Y channels are
used for the joystick. The Z and F channels may be used for special applications, e.g.
Autofocus or
ADC_LOCK
and
ADC_FOLLOW
modes of controlling the stage. Special
firmware is required for these applications. It’s a
Card-Addressed command.
Example:
1
RA X Y
:A 128 128
Command: RDSBYTE
Shortcut:
RB
Format:
RDSBYTE axis [axis] [axis]…
Function:
Requests the TG-1000 and MS-2000 to respond with the Status Byte. It’s an
Axis-Specific
Command.
The number is one byte, which can be broken down into 8 bits that represent the
following internal flags:
Bit 0: 0 = No commanded move is in progress. 1 = A commanded move is in progress.
This bit is synonymous with the STATUS command. If the bit is set, then STATUS
returns '
B
', otherwise STATUS returns '
N
'.
Bit 1: 0 = The axis is disabled. It can be renabled by one of the following: High Level
command
MC <axis>+
, cycling the clutch switch for the Z-axis, Low Level
StartMotor command (hex 47), or a system reset. This feature is available in
versions 6.2c and later; 1 = The axis is enabled.
Bit 2: 0 = Motor is inactive (off), 1 = Motor is active (on).
Bit 3: 0 = Joystick/Knob disabled, 1 = Joystick/Knob enabled
Bit 4: 0 = Motor not ramping, 1 = Motor ramping
Bit 5: 0 = Ramping down, 1= Ramping up
Bit 6: Upper limit switch: 0 = open, 1 = closed
Bit 7: Lower limit switch: 0 = open, 1 = closed
Reply:
:
<byte as hexadecimal>
Summary of Contents for Tiger TG-1000
Page 12: ...11 Change log 53...