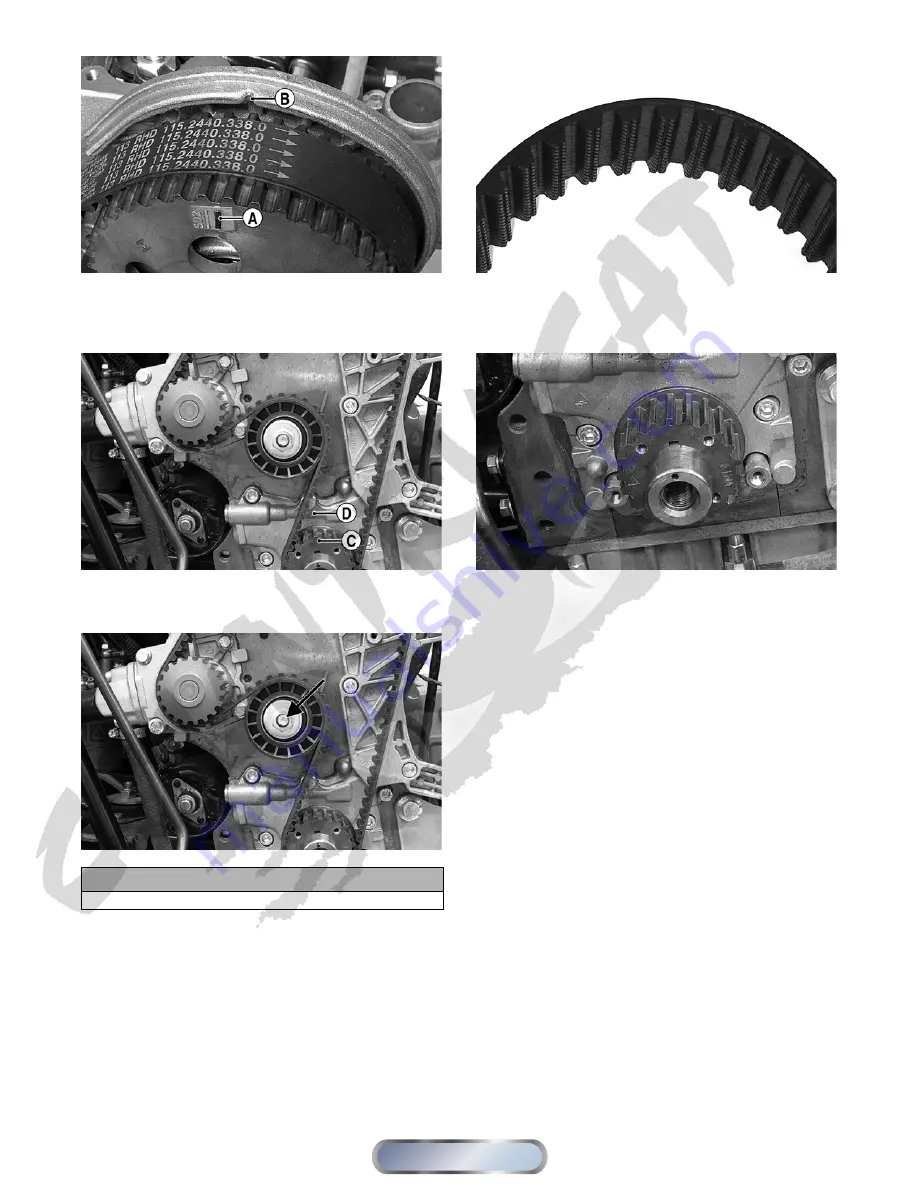
53
DE269A
9. Check that the reference mark (C) on the timing belt
drive pulley aligns with the reference mark (D) on
the oil pump housing.
DE230A
10. Loosen the retaining nut on the timing belt idler pul-
ley; then loosen the belt and remove from the engine.
DE230B
Inspecting
1. Check the timing belt for missing cogs, cracks, or
bare cords showing. Replace if any of the conditions
are present.
DE273
2. Inspect the drive and driven pulleys for wear, burrs,
or dirt build-up between cogs. Clean and remove
burrs as required.
DE232
3. Inspect the timing belt cover for cracks, seal damage,
or signs of oil leakage. If oil is present, locate and
repair any leaks. Thoroughly clean all oil from the
timing belt cover and pulleys.
Installing
1. Check that the reference mark (C) on the timing belt
drive pulley is aligned with the reference mark (D)
on the oil pump housing and the reference mark (A)
on the camshaft drive pulley is aligned with the ref-
erence mark (B) on the cylinder head.
NOTE: If the camshaft or crankshaft has been
rotated, use the following procedure to safely realign
the reference marks.
A. Carefully rotate the crankshaft until the reference
mark (C) on the timing belt drive pulley is
approximately 90° from the reference mark (D)
on the oil pump housing.
CAUTION
Do not rotate the camshaft or valve damage could occur.
Manual
Table of Contents