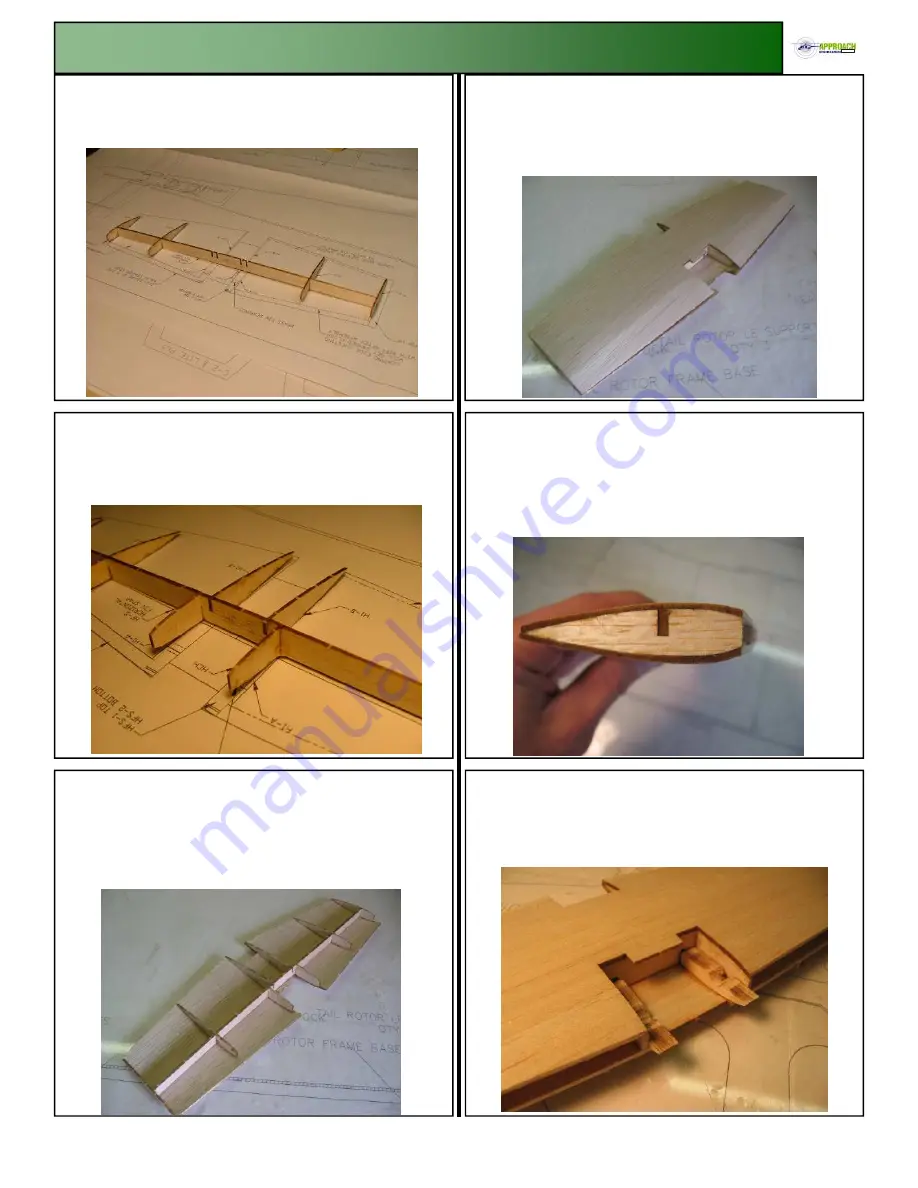
APACHE-E SWIFT/LOGO10 PAGE # 18
DAWSON’S
APPROACH E GI EERI G
AH-64A ELECTRIC
15.1
Punch out the 3/32” horizontal fin spar, HF-S, and hori-
zontal fin ribs H-2, and H-3. Glue the ribs to the spar in their
corresponding notches.
15.2
Punch out the 3/32” horizontal fin ribs H-1A, H-1B.
Glue the two H1-A ribs in the outside notches facing toward the
front edge. H1-B ribs are glued to the inside notches facing
toward the trailing edge.
15.3
Punch out the horizontal fin lower sheeting, HF-1, and
place the spar assembly in the proper place. The wing spar will
line up with the center sheeting cut out and be flush with the
edge. Start by applying CA+ to the lower surface of the spar.
Once dried apply CA+ to the lower surface of the ribs behind
the spar to the trailing edge. Press the sheeting up into place.
15.4
Punch out the 1/16” balsa upper sheeting HF-2. Sheet
the top of the horizontal fin by aligning the trailing edge of the
upper and lower sheeting. Apply CA+ to the upper surface of
the spar, the ribs behind the spar and trailing edge. Press the
sheeting back and hold the trailing edge together.
15.5
Glue the upper and lower surfaces of the balsa leading
edge and press the sheeting down into place. Cut off the excess
sheeting along the leading edge. Using a flat sanding block
sand the leading edge flat.
15.6
Turn the horizontal fin assembly over to expose the box
bay. Punch out the two ¼” light ply horizontal fin supports
HFS-1. Using CA+ glue the supports up against the upper
sheeting, H1-A, and the wing spar.
15.0 HORIZO TAL FI
ASSEMBLY
Summary of Contents for AH-64A APACHE SWIFT/LOGO 10
Page 1: ...A H 6 4 A A P A C H E S W I F T L O G O 1 0 APPROACH E GI EERI G www ApproachEngineering com ...
Page 36: ...23 0 FI AL ASSEMBLY APPE DIX A HELLFIRE LAU CHER ASSEMBLY ROCKET LAU CHER ASSEMBLY ...
Page 37: ...23 0 FI AL ASSEMBLY APPE DIX B 30 MM GU ASSEMBLY E GI E ACELLE ASSEMBLY ...
Page 38: ...23 0 FI AL ASSEMBLY F 1 SECTIO APPE DIX C VERTICAL FI ASSEMBLY ...
Page 39: ...23 0 FI AL ASSEMBLY F 3 SECTIO APPE DIX D VERTICAL FI ASSEMBLY ...
Page 40: ...23 0 FI AL ASSEMBLY HORIZO TAL FI ASSEMBLY APPE DIX E WI G ASSEMBLY ...
Page 41: ...23 0 FI AL ASSEMBLY APPE DIX F ...
Page 42: ...THREE VIEW DRAWING ...
Page 43: ...DOOR LOCATIONS AND DESCRIPTION ...
Page 44: ...WEAPONS PYLONS HORIZONTAL STABALIZER ENGINE EXHAUST ...