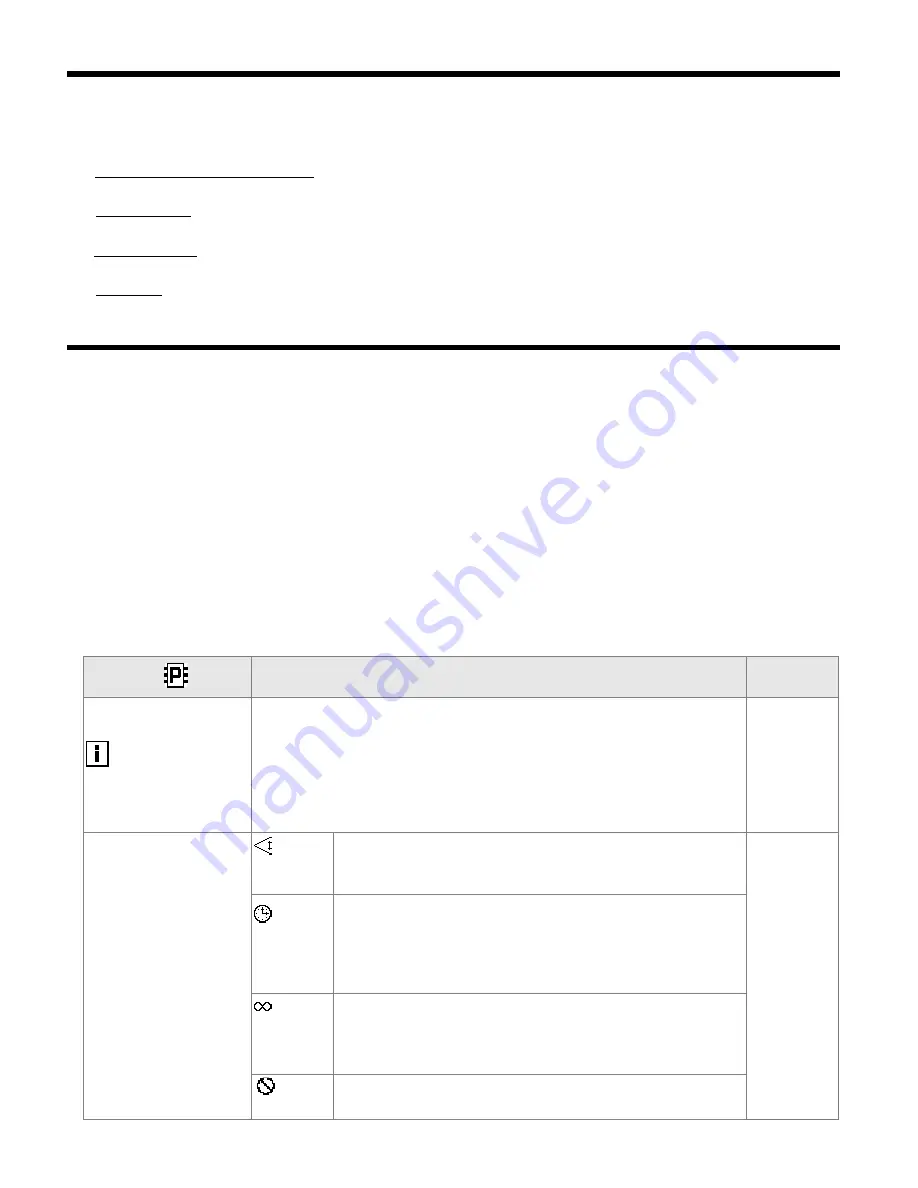
28
12.4.2.3. CORRECTION OF PID PARAMETERS
The automatic tuning function correctly selects the PID regulation parameters for most processes; however,
sometimes it may be necessary to correct them. Due to the strong correlation between those parameters, only
one parameter should be changed in the selected
Set of PID parameters
and the impact of the change on the
process should be observed:
a) oscillations around the threshold - increase the
Proportional band Pb
or the
Integration time constant Ti
,
decrease the
Differentiation time constant Td
(or reduce by a half the
Pulsing period Tc for the output
)
b) slow response - decrease the
Proportional band Pb
, the
Differentiation time constant Td
, and the
Integration
time constant Ti
c) over-regulation - increase the
Proportional band Pb
, the
Differentiation time constant Td
, and the
Integration time constant Ti
d) instability - increase the
Integration time constant Ti
12.4.3. SETS OF PROGRAM CONTROL PARAMETERS
The controller makes it possible to create 4 independent control programs, each consisting of a maximum of 12
sections. The programs can be freely assigned to individual control outputs with the parameters
Setpoint (SP)
selection
set to
Setpoint value from Program 1
÷
4
(chapter 12.4.1). Also, it is possible to define auxiliary outputs
and sound alarms for individual sections of the program, which may be used for indicating the operation status
and for switching on additional devices (fans, additional heating sections, etc.) The option of power control (when
the
Auxiliary output state
parameter is set to
Manual mode with a set value
); a description is given in the table
12.4.3. The diagram with an example of a configuration of a program consisting of 4 sections is shown in chapter
12.4.3.1. The program is started at the time of start of the control (automatically or manually, chapter 12.4.1.1) and
is always performed from the start (the 1st section). In the
CONTROL
type window (chapter 11.2) and in the
Quick
configuration screen
, the status of operation of the program is shown in the line starting with the phrase PRGx
(where x is the number of the program; the meaning of the individual fields is the following:
PRGx: the number of
the current section/the number of all sections: the type of the stage
, e.g.
PRG1:4/5:60m
(program 1, section four out of
the five sections used, remaining time of the section 60 minutes). Depending on the
Stage type
parameter, the
stage type
field can have the values described in the table below (12.4.3).
Table 12.4.3. The parameters in the
Control and alarms options
menu for the selected section (1
÷
12) of the program (1
÷
4)
Parameter
Range of variability of the parameter and description
Factory
settings
Assigned and active
outputs
the numbers (
1
÷
4
or
None
) are displayed of the control outputs to which the
presented program is related (using the parameters
Setpoint (SP) selection
)
and of the auxiliary outputs for the current section of the program (set with
the
Assignment of the control signal
parameter for the outputs and the
Selection of auxiliary output
parameter for the section); a description of the
parameters is given in chapter 12.4.1 and in this table; if the value is
None
, the
program is not used or the outputs are disabled.
None
Stage type
Gradient
(PV/min)
achievement of the
Set point value SP
with the set gradient
(ramping) defined by the parameter
Gradient (PV/min)
, the
stage
type
field in the operation status has the value of
PV/min
Gradient
(PV/min)
Stage
time after
reaching of
the SP
the time countdown starts after the measured value reaches the
band defined by the parameter
Hysteresis and band for the start
of the stage time
, the
stage type
field in the status shows
PV->SP
(achievement of the
Setpoint value SP
) or the remaining
Stage
time
(in minutes or seconds when time<1 min.)
Continuous
(without a
time limit)
the
stage type
field in the status always has the value
PV->SP
(achievement of the
Setpoint value SP
), at the same time this is
the last section of the program with constantly enabled control
End
(stop)
the last section of the program, control stopped, status field
stage
type
=
Stop