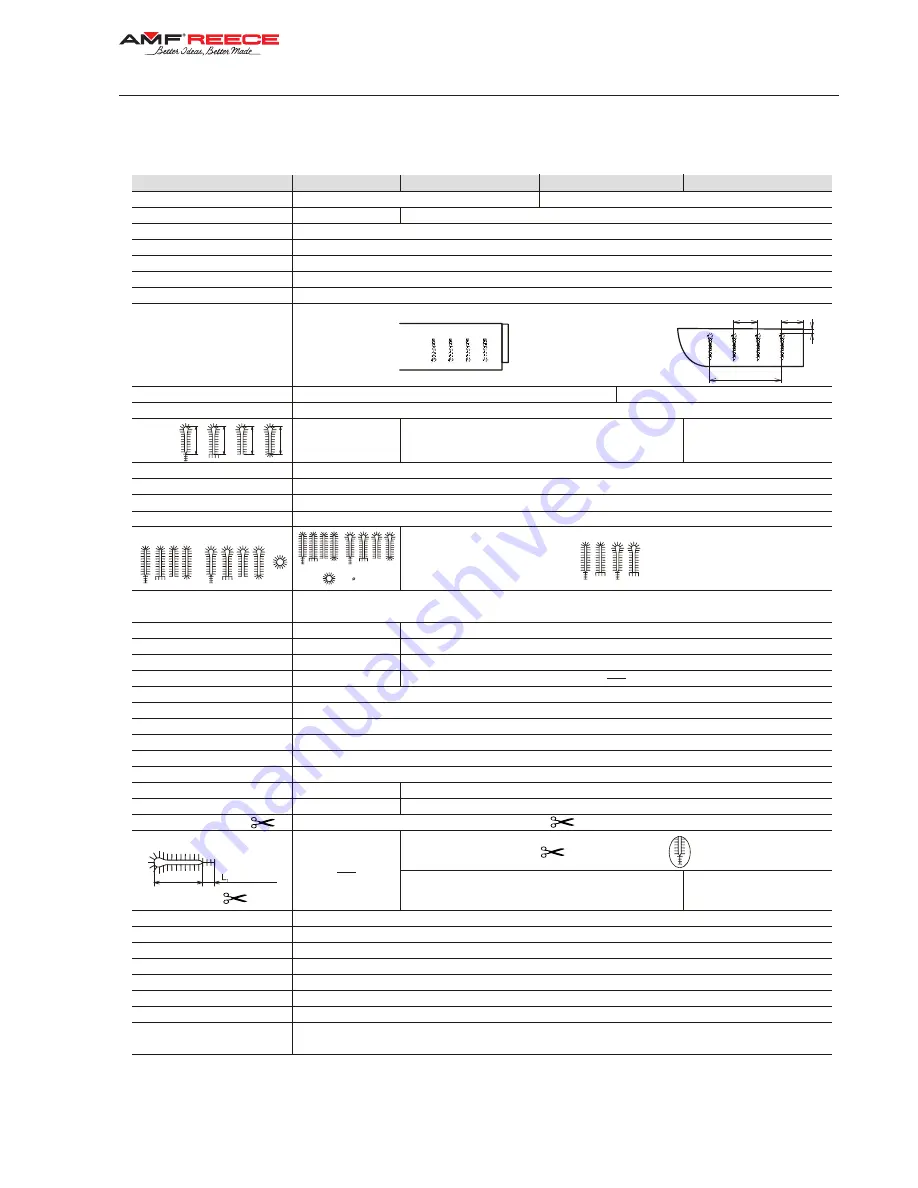
S-311+I
1-7 I
A - INTRODUCTION
Released: 01/2014
E-mail: [email protected]; webside: amfreece.com
Phone: +420 582 309 146; Fax: +420 582 360 606
3. SPECIFICATIONS
* Note:
If a customer uses thread size 100 and less, the manufacturer recommends to use the left looper 17.0069.4.019
If you use poor quality threads on the machine, the thread can burn at the needle (producer recommend decrease machine´s speed).
Machine models
AF ST JT
10 - 50 mm
3,0 - 20,0 mm
4 - 8 mm
4 to 20
4 to 20
12 mm
in 8,0 mm
Cut before (CB), cut after (CA), no cut (OFF)
- 0,50 to + 1,2 mm
See section D 3.3 - manual S-311
4-6 mm
0,5-1,5 mm
No Eye; 2,2 x 3,0 mm; 2,8 x 4,2 mm; 3,0 x 4,6 mm; 3,2 x 5,0 mm; 3,4 x 4,2 mm
2,1 mm (
± 0,3 mm electronic adjustment); 2,7 mm (± 0,3 mm electronic adjustment)
± 1,5 mm
64 mm
02.0558.0.111 (Nm 100)
02.0558.1.112 (Nm 110)
80, 100, 120, gimp size 10-30 standard **.
80, 100, 120, gimp size 30-100
L = 16 to 20 mm
L+L = 23 to 27 mm
1
0,55 MPa = 80 PSI
530 mm (height) x 370 mm (width) x 560 mm (depth)
730 mm (height) x 1100 mm (width) x 700 mm (depth) + 150 mm distance
64 kg
180 kg
1NPE~60Hz 230 V/TN/S; 1NPE~50Hz 230 V/TN/S
Min. 10A Characteristic C (EN60947-2)
L =86,9db; L =74,8 db; Noise measurement according to EN ISO 3746:1995
wA
pfA
According to IEC 364-3, IEC 364-5-51 temperature from +5°C do 40°C, relative air humidity from 30 to 80%
16 - 20 mm
1000 - 2000 stitches/min (500 - 1000 rev/min of the drive shaft)
Jacket Sleeve
Single chainstitch
Jeans Fly Front
1 - 6 buttonhole
8 - 160 mm
31 mm
9 - 19 mm
160 mm
Yes
No
Double chainstitch with or without gimp
Jeans Fly Front
0,5 to 2,0 mm (increments of 0,1 mm)
Sewing Speed
Application
Stitch Type
Number of Buttonholes
Distance between Buttonholes
Distance from Fabric Edge
(horizontal)
Distance from Fabric Edge
(vertical)
Max. Horizontal Feed Amount
Thread Nipper
Stitch Density
Buttonholes style
Eye type
Fly Bar Length
Length of Crossbar
Number of Stitches in the eye
Number of Stitches in the round end
Clamp Foot Height
Sewing Thickness
Buttonhole Cutting
Cutting Space
Cut position (Y axis)
Bedplate movement
Needle system
Recommended threads*
Upper thread trimming
Lower thread and gimp trimming
Cutting space
Operating Condition
Air pressure
Machine db Level
Machine Head Dimension
Machine Head Weight
Table Dimensions
Machine Weight
Electrical requirements
Line Circuit Breaker
Stitch Bite
CT 16 - 20 mm DT JT
CT 16 - 20 mm DT JS
L
= 3 to 7 mm
(short ends)
max 3,5 mm
0,5 - 1,5 mm
Crossbar density
Jacket Sleeve
A
B
C
D
A
B
C
D
S-311+I
Buttonhole
Length
CT 20 - 24 mm DT JS
20 - 24 mm
2,1 mm (
± 0,3 mm electronic adjustment); 2,7 mm (± 0,3 mm electronic adjustment)
Stitch Bite (Crossbar)
L = 20 to 24 mm
L+L =
mm
1
27 - 31