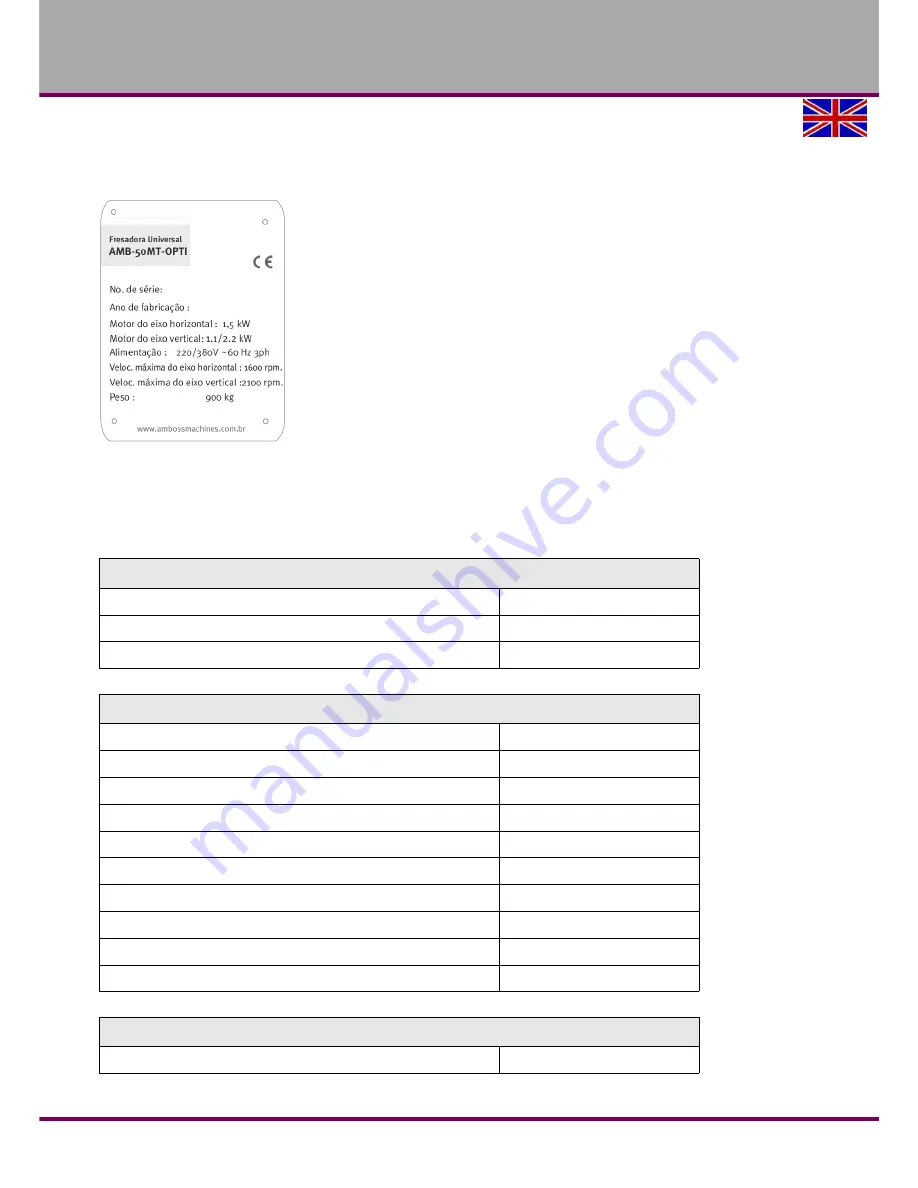
Version 1.1.1 dated February 25th, 2013
Page 17
Original operating instructions
MT50
GB
2
Technical data
2.1
Type plate
Fig. 2-1:
Type plate
The following information are the dimensions and indications of weight and the manufacturer‘s
approved machine data.
2.2
Electrical connection
z
H
0
6
~
V
0
8
/3
220
W
K
5
.
4
d
a
o
l
d
e
t
c
e
n
n
o
c
l
a
t
o
T
W
k
5
.
1
e
l
d
n
i
p
s
l
a
t
n
o
z
ir
o
h
r
e
w
o
p
r
o
t
o
M
Motor power vertical
W
k
2
.
2
/
1
.
1
e
l
d
n
i
p
s
2.3
Dimensions
0
4
K
S
)
g
n
ill
i
m
l
a
c
it
r
e
v
,
g
n
il
li
m
l
a
t
n
o
z
ir
o
h
(
t
a
e
s
e
l
d
n
i
p
S
m
m
0
4
2
x
m
m
0
0
8
e
l
b
a
t
s
s
o
r
C
Height
2270 mm
Width
1500 mm
Depth
2100 mm
g
k
0
0
9
t
h
g
i
e
w
l
a
t
o
T
g
k
0
5
0
1
g
n
i
g
a
k
c
a
p
g
n
i
d
u
l
c
n
i
t
h
g
i
e
W
m
m
0
0
1
2
x
0
2
2
1
x
0
9
2
1
H
x
W
x
L
g
n
i
g
a
k
c
a
p
f
o
s
n
o
i
s
n
e
m
i
D
g
k
0
6
1
e
l
b
a
t
s
s
o
r
c
f
o
d
a
o
l
.
x
a
M
4
/
m
m
4
1
r
e
b
m
u
n
/
e
z
i
s
t
o
l
s
-
T
2.4
Adjustment travels/ Slewing ranges/ Distances
m
m
0
2
1
e
k
o
rt
s
e
l
d
n
i
p
S